Have you ever wondered how to keep your mechanical seals in top condition? Proper maintenance is crucial for preventing leaks and extending the life of your seals.
In this blog post, we’ll share 10 essential tips that will help you maintain your mechanical seals effectively. By following these guidelines, you’ll ensure optimal performance and minimize costly downtime.
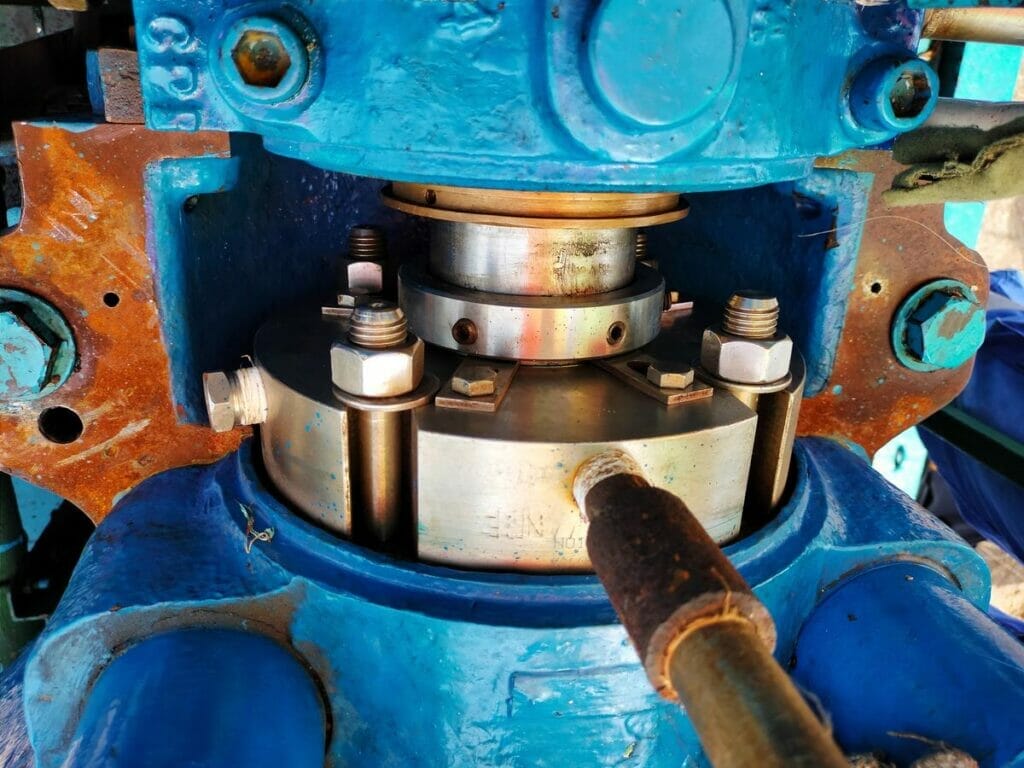
Proper Installation
Correct installation is crucial for the longevity and performance of mechanical seals. Ensure that the seal is installed according to the manufacturer’s specifications, with proper alignment and clearance. Misalignment can lead to premature wear and failure of the seal faces.
Correct Material Selection
Choose the appropriate seal material based on the application’s requirements. Consider factors such as temperature, pressure, chemical compatibility, and abrasiveness of the media being sealed. Incorrect material selection can result in rapid degradation and failure of the seal.
Adequate Lubrication
Proper lubrication is essential for the smooth operation of mechanical seals. Ensure that the seal is adequately lubricated with the recommended lubricant, which should be compatible with the seal material and the media being sealed. Insufficient or improper lubrication can cause increased friction and heat generation, leading to seal damage.
Clean Seal Faces
Maintain clean seal faces to prevent contamination and ensure proper sealing. Regular cleaning of the seal faces helps remove any debris or build-up that may interfere with the sealing process. Contaminated seal faces can cause leakage and accelerate wear.
Regular Inspection
Conduct regular inspections of the mechanical seal to identify any signs of wear, damage, or leakage. Inspections should include checking for visible cracks, chips, or irregularities on the seal faces, as well as monitoring for any unusual noise or vibration. Early detection of issues allows for timely maintenance and prevents catastrophic failures.
Appropriate Seal Pressure
Maintain the appropriate seal pressure as specified by the manufacturer. Excessive pressure can cause increased wear and damage to the seal faces, while insufficient pressure may result in leakage. Regularly monitor and adjust the seal pressure to ensure optimal performance.
Temperature Control
Control the operating temperature of the mechanical seal within the recommended range. Excessive heat can cause thermal expansion and distortion of the seal components, leading to leakage and failure. Implement proper cooling systems or heat dissipation methods to maintain a stable temperature.
Vibration Monitoring
Monitor and control vibration levels in the equipment where the mechanical seal is installed. Excessive vibration can cause misalignment, increased wear, and premature failure of the seal. Regularly check for any abnormal vibrations and address the root cause, such as imbalance or bearing issues, to minimize the impact on the seal.
Timely Repair and Replacement
Address any identified issues with the mechanical seal promptly. If the seal shows signs of excessive wear, damage, or leakage, it may require repair or replacement. Delaying necessary maintenance can lead to more severe problems and unplanned downtime. Establish a proactive maintenance schedule to ensure timely interventions.
Comprehensive Training
Provide comprehensive training to personnel involved in the installation, operation, and maintenance of mechanical seals. Proper training ensures that best practices are followed, and potential issues are identified and addressed quickly. Include training on seal handling, installation procedures, troubleshooting, and safety precautions.
In conclusion
Proper mechanical seal maintenance is crucial for optimal performance and longevity. By following these 10 tips, you can prevent costly failures and unplanned downtime.
Implement these best practices today to ensure the reliability and efficiency of your mechanical seals. Contact us for more information or assistance.