Have you ever wondered about the different types of double mechanical seal arrangements? In this blog post, we’ll explore the various configurations and their unique advantages.
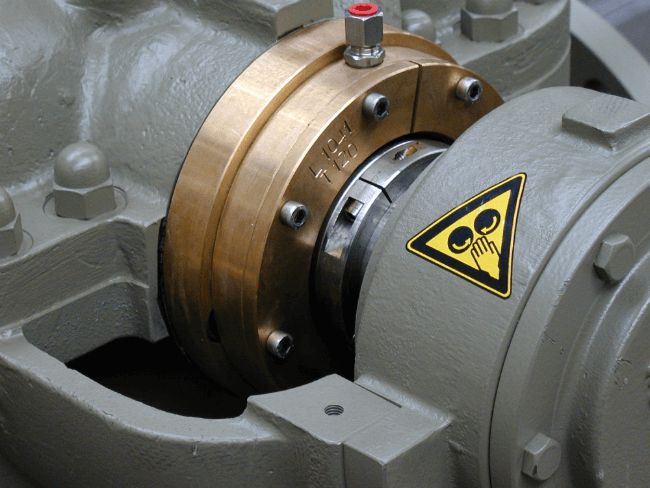
Tandem Mechanical Seal Arrangement
A tandem mechanical seal arrangement consists of two mechanical seals mounted on the same shaft, with both seals facing the same direction. The seals are arranged in series, with the primary seal (closest to the process fluid) and the secondary seal (furthest from the process fluid) working together to provide enhanced sealing performance and reliability.
How Tandem Mechanical Seal Arrangement Works
In a tandem mechanical seal arrangement, the primary seal serves as the main barrier between the process fluid and the atmosphere. The secondary seal acts as a backup, containing any leakage from the primary seal and preventing it from escaping to the environment.
A buffer fluid, typically at a higher pressure than the process fluid, is introduced between the two seals. This buffer fluid lubricates the seals, reduces heat generation, and helps to prevent process fluid from reaching the secondary seal in case of primary seal failure.
Advantages of Tandem Mechanical Seal Arrangement
- Enhanced safety: In the event of primary seal failure, the secondary seal contains any leakage, minimizing the risk of process fluid escape and increasing overall system safety.
- Improved reliability: The presence of a backup seal and the use of a buffer fluid increase the overall reliability of the sealing system, reducing the likelihood of complete seal failure.
- Longer seal life: The buffer fluid helps to lubricate the seals and reduce heat generation, which can extend the life of both the primary and secondary seals.
Disadvantages of Tandem Mechanical Seal Arrangement
- Increased complexity: Tandem seals require additional piping, valves, and instrumentation for the buffer fluid system. This makes the sealing system more complex and potentially harder to maintain.
- Higher cost: The added complexity and components of tandem seals result in higher initial costs and maintenance expenses compared to simpler double seal arrangements.
Applications of Tandem Mechanical Seal Arrangement
- Hazardous or toxic fluids: Industries use tandem seals to minimize leakage risk and protect personnel and the environment when handling dangerous chemicals or pollutants.
- High-pressure or high-temperature processes: Tandem seals manage heat and maintain seal integrity in demanding conditions due to the buffer fluid.
- Critical equipment: Tandem seals provide added protection and reliability, preventing significant downtime or production losses in case of seal failure.
Back-to-Back Double Seal Arrangement
A Back-to-Back double seal arrangement consists of two mechanical seals mounted in the same direction, with the inboard seal (closest to the product) and the outboard seal (farthest from the product) oriented away from each other. The space between the two seals is typically filled with a buffer fluid, which is maintained at a higher pressure than the process fluid.
How Back-to-Back Double Seal Arrangement works
In a Back-to-Back arrangement, the inboard seal prevents the process fluid from escaping the pump or equipment. The buffer fluid, kept at a higher pressure than the process fluid, creates a barrier that prevents process fluid from reaching the outboard seal. This buffer fluid absorbs any leakage that may occur from the inboard seal, protecting the outboard seal and the environment.
Advantages of Back-to-Back Double Seal Arrangement
- Increased safety: The high-pressure buffer fluid prevents process fluid from leaking to the atmosphere, making it suitable for hazardous or toxic applications.
- Improved seal life: The outboard seal operates in a clean, controlled environment, extending its lifespan.
- Versatility: Back-to-Back seals can handle a wide range of process fluids and operating conditions.
Disadvantages of Back-to-Back Double Seal Arrangement
- Higher cost: The additional components and complexity of Back-to-Back seals make them more expensive than other arrangements.
- Increased maintenance: Monitoring and maintaining the buffer fluid requires more attention and resources.
- Potential for heat buildup: In some cases, the high-pressure buffer fluid can generate excess heat, which may require cooling systems.
Applications of Back-to-Back Double Seal Arrangement
- Petrochemical and oil & gas industries: Where flammable or toxic fluids are handled.
- Chemical processing plants: Dealing with aggressive or hazardous substances.
- Pharmaceutical manufacturing: Requiring strict containment and sterility.
Face-to-Face Double Seal Arrangement
In a face-to-face double seal arrangement, two mechanical seals are mounted with their faces pointing towards each other. This configuration allows the seals to share a common cavity, which is typically filled with a barrier fluid or buffer fluid.
How Face-to-Face Double Seal Arrangement Works
The barrier fluid in the common cavity between the two seals is pressurized to a level higher than the process fluid pressure. This prevents the process fluid from entering the seal cavity. The inboard seal serves as the primary seal, while the outboard seal acts as a secondary seal, providing additional protection against leakage.
The barrier fluid absorbs any leakage from the inboard seal, preventing it from escaping to the atmosphere. The barrier fluid can be circulated through a cooling system to remove heat generated by the seals, maintaining a stable operating environment.
Advantages of Face-to-Face Double Seal Arrangement
- Enhanced leakage control: The barrier fluid prevents process fluid from leaking to the atmosphere, providing superior leakage control.
- Increased seal life: The barrier fluid helps lubricate and cool the seals, reducing wear and extending seal life.
- Simplified piping: Face-to-face arrangements require less complex piping compared to back-to-back and tandem configurations.
- Easier maintenance: The common cavity design allows for easier seal maintenance and replacement.
Disadvantages of Face-to-Face Double Seal Arrangement
- Higher initial cost: The additional components and piping required for the barrier fluid system increase the initial installation cost.
- Potential for barrier fluid contamination: If the inboard seal fails, process fluid can contaminate the barrier fluid, compromising the system’s effectiveness.
- Limited pressure capabilities: Face-to-face seals may not be suitable for high-pressure applications compared to tandem arrangements.
Applications of Face-to-Face Double Seal Arrangement
- Chemical processing: Face-to-face seals are ideal for handling hazardous or toxic chemicals that require maximum containment.
- Pharmaceutical industry: The improved leakage control provided by face-to-face seals is essential in maintaining product purity and preventing contamination.
- Food and beverage processing: Face-to-face arrangements help maintain product quality and safety by minimizing the risk of contamination.
FAQs
Which double seal arrangement is the most common?
The tandem seal arrangement is the most common due to its simplicity and effectiveness in many applications.
In conclusion
Understanding the three types of double mechanical seal arrangements is crucial for selecting the most suitable sealing solution for specific applications. To learn more about double mechanical seals and how they can benefit your operations, contact a trusted seal manufacturer or supplier today.