Have you ever wondered about the differences between balanced and unbalanced mechanical seals? In this blog post, we’ll dive into the key distinctions between these two types of seals, exploring their design, applications, and performance.
By the end of this article, you’ll have a clear understanding of when to choose a balanced or unbalanced seal for your specific needs, ensuring optimal efficiency and reliability in your mechanical systems. Get ready to discover the world of mechanical seals!
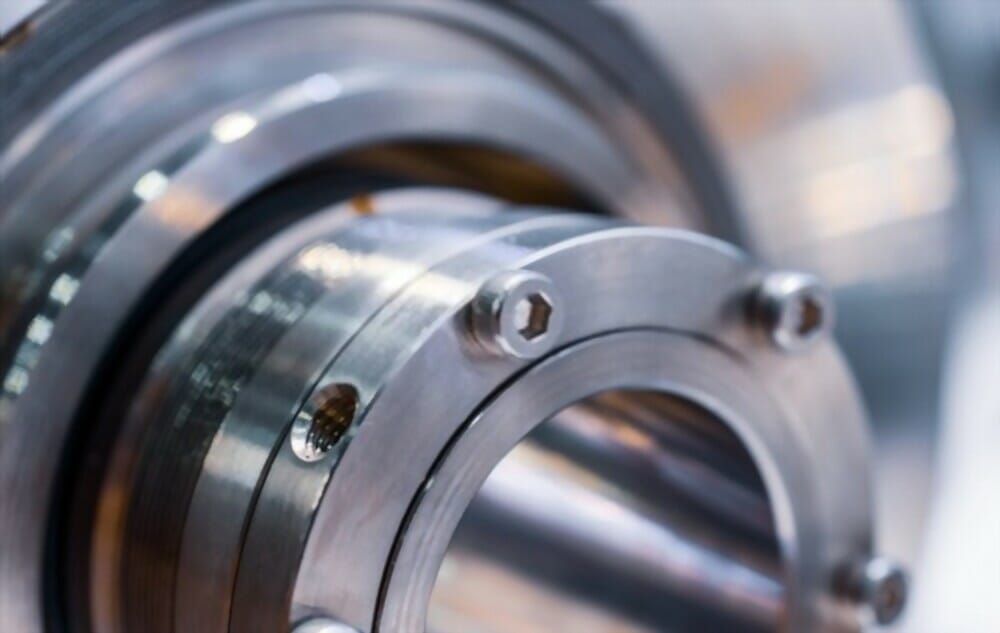
Fundamentals of Mechanical Seal Balance
Definition of seal balance and balance ratio
In mechanical seals, balance refers to the distribution of hydraulic forces acting on the seal faces. The balance ratio is a key parameter that quantifies the degree of balance in a mechanical seal. It is defined as the ratio of the hydraulic closing force to the hydraulic opening force acting on the seal faces.
The hydraulic closing force is the force that pushes the seal faces together, while the hydraulic opening force tends to separate the seal faces. A well-designed mechanical seal must strike a balance between these two forces to ensure optimal performance and longevity.
How balance ratio is calculated for seals pressurized at the outer vs inner diameter
The balance ratio calculation differs depending on whether the seal is pressurized at the outer or inner diameter. For seals pressurized at the outer diameter, the balance ratio is calculated as follows:
Balance ratio = (Seal face area exposed to pressure) / (Total seal face area)
In this case, the hydraulic closing force is greater than the hydraulic opening force, resulting in a balance ratio greater than 1.
For seals pressurized at the inner diameter, the balance ratio is calculated as:
Balance ratio = (Total seal face area – Seal face area exposed to pressure) / (Total seal face area)
Here, the hydraulic opening force is greater than the hydraulic closing force, resulting in a balance ratio less than 1.
Typical balance ratios for unbalanced and balanced seals
Unbalanced seals have a balance ratio greater than 1, typically ranging from 1.1 to 1.5. In unbalanced seals, the hydraulic closing force is significantly higher than the hydraulic opening force. This results in higher face contact pressure, which can lead to increased wear and heat generation. Unbalanced seals are generally used in low-pressure applications or when the sealed fluid is clean and non-abrasive.
Balanced seals have a balance ratio close to 1, usually between 0.65 and 0.85. In balanced seals, the hydraulic closing force and opening force are more evenly matched, resulting in lower face contact pressure. This reduces wear and heat generation, making balanced seals suitable for high-pressure applications or when sealing abrasive or dirty fluids. Balanced seals also offer better performance and longer seal life compared to unbalanced seals in most applications.

What is Unbalanced Mechanical Seals
Unbalanced mechanical seals are a type of seal designed with a larger surface area on the process side compared to the atmospheric side. This asymmetrical design results in a net hydraulic force that pushes the seal faces together during operation.
The unequal surface areas of the seal faces create a pressure differential, which helps to maintain proper sealing under various operating conditions. The higher pressure on the process side acts upon the larger surface area, generating a closing force that keeps the seal faces in contact.
Advantages of Unbalanced Mechanical Seals
- Strong Sealing Force: Maintains strong sealing under high-pressure conditions due to a larger surface area on the process side.
- Improved Stability: Offers better stability and resistance to opening forces, reducing leakage risk.
- Simpler Design: Easier to install, maintain, and replace, lowering downtime and maintenance costs.
Disadvantages of Unbalanced Mechanical Seals
- Higher Face Loading: Unbalanced seals have higher face loading, leading to increased wear and shorter seal life compared to balanced seals.
- Increased Wear and Maintenance Costs: The higher closing force causes the seal faces to wear down more quickly, resulting in more frequent replacements and higher maintenance costs.
- Limitations in High-Speed Applications: The higher face loading increases friction and heat generation, making unbalanced seals unsuitable for high-speed operations or applications with significant axial movement.
- Not Ideal for Low-Pressure Applications: In low-pressure applications or those with frequent pressure fluctuations, the higher closing force of unbalanced seals can cause premature wear or damage to the seal faces.
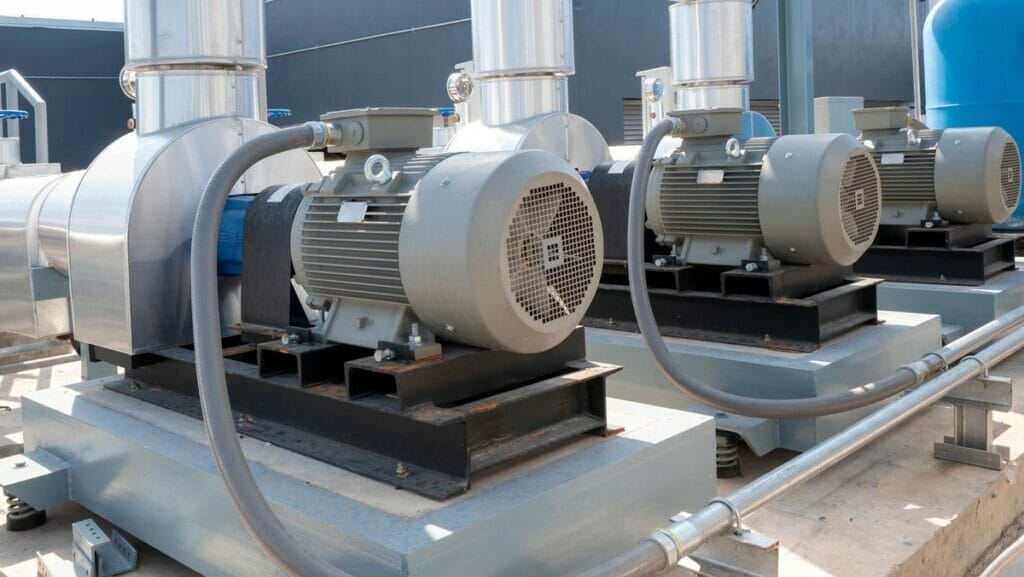
What is Balanced Mechanical Seals
A balanced mechanical seal is a type of seal designed to minimize the axial forces acting on the seal faces. In a balanced seal, the hydraulic forces are distributed more evenly across the seal faces, reducing the net closing force. This is achieved by incorporating a step or groove in the rotating seal face, which allows the process fluid pressure to act on a larger area, counterbalancing the hydraulic closing force.
Advantages of Balanced Mechanical Seals
- Extended seal life: Less wear due to reduced closing force, resulting in a longer operating life.
- Reduced heat generation: Lower face loading means less friction and heat, preserving sealing components and process fluid integrity.
- Higher pressure capabilities: Can handle higher pressures, suitable for demanding applications.
- Improved performance in variable conditions: Better at managing pressure and temperature fluctuations for consistent sealing.
- Reduced power consumption: Lower friction leads to energy savings in rotating equipment.
Disadvantages of Balanced Mechanical Seals
- Increased complexity: Balanced seals have a more intricate design, making them harder to manufacture and install.
- Higher initial cost: The complex design and precision needed for balanced seals make them more expensive than unbalanced seals.
- Sensitivity to contamination: Balanced seals are more prone to clogging and damage from contaminated fluids, needing cleaner environments.
- Limited low-pressure performance: Balanced seals may not seal properly in low-pressure situations, leading to potential leakage.
- Reduced adaptability to misalignment: The design of balanced seals makes them less tolerant of shaft misalignment or installation errors.
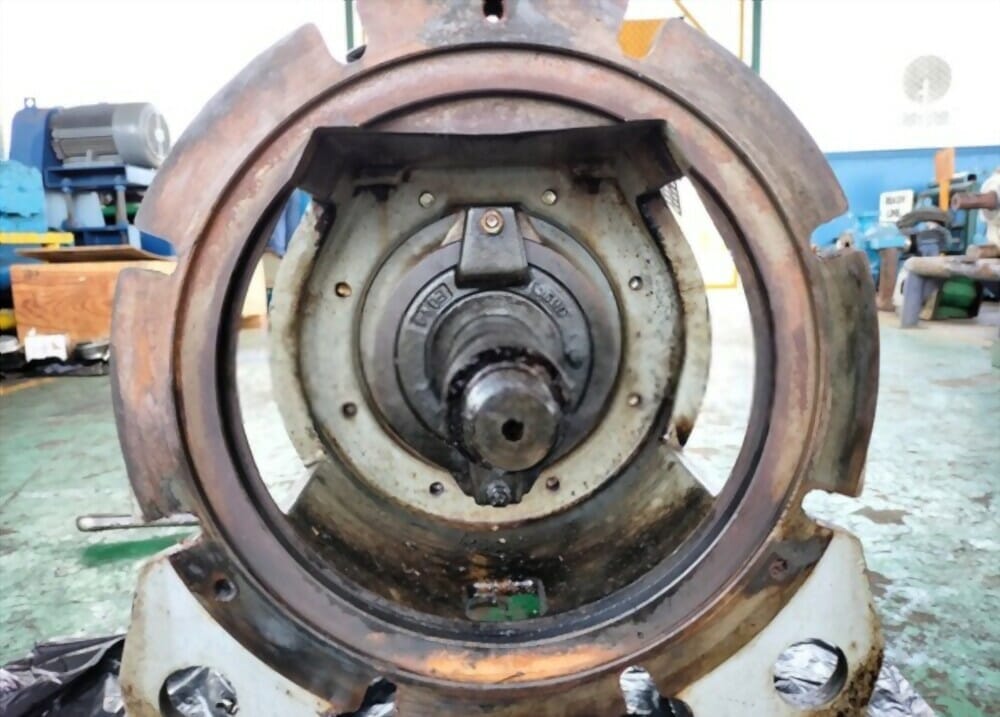
Key Differences Between Balanced and Unbalanced Seals
- Force Distribution: In an unbalanced seal, the closing force acts on the entire seal face area, while in a balanced seal, the closing force acts on a smaller effective area.
- Pressure Handling: Balanced seals are better suited for high-pressure applications, as they can effectively manage the hydraulic forces. Unbalanced seals are more appropriate for lower-pressure applications.
- Wear and Lifespan: Balanced seals experience less wear due to the reduced closing force, resulting in a longer lifespan compared to unbalanced seals.
- Complexity and Cost: Balanced seals have a more complex design and are generally more expensive than unbalanced seals.
Factors to Consider When Selecting Between Balanced and Unbalanced Seals
System Pressure and Pressure Variations
The choice between a balanced and unbalanced mechanical seal depends heavily on the system pressure and its variations. Balanced seals are designed to handle higher pressures and significant pressure fluctuations more effectively than unbalanced seals.
In systems with high pressures or frequent pressure spikes, balanced seals distribute the pressure evenly across the seal faces, reducing the risk of seal failure and leakage. Unbalanced seals, on the other hand, are better suited for lower pressure applications with minimal pressure variations.
Fluid Properties (Viscosity, Lubricity, Vapor Pressure)
Balanced seals are generally preferred for fluids with high viscosity or low lubricity, as they can maintain a stable fluid film between the seal faces, reducing wear and increasing seal life.
Fluids with high vapor pressures may cause flashing or cavitation at the seal faces, leading to premature seal failure. In such cases, balanced seals can help mitigate these issues by reducing the pressure differential across the seal faces.
Shaft Speed and Size
High shaft speeds generate more heat and can cause thermal distortion of the seal faces, leading to leakage or failure. Balanced seals are better equipped to handle higher shaft speeds, as they maintain a more stable fluid film and reduce heat generation.
Larger shaft sizes also benefit from balanced seals, as they can accommodate the increased forces and thermal expansion associated with larger seals.
Temperature
High temperatures can cause thermal expansion and distortion of the seal components, leading to leakage or failure.
Balanced seals are more suitable for high-temperature applications, as they can maintain a stable fluid film and reduce heat generation at the seal faces. Unbalanced seals may be sufficient for lower temperature applications, where thermal effects are less significant.
Vibration and Shaft Misalignment
Vibration and shaft misalignment can cause premature seal failure by disrupting the fluid film between the seal faces and increasing wear. Balanced seals are more tolerant of vibration and shaft misalignment, as they maintain a more stable fluid film and have a higher axial flexibility.
Unbalanced seals are more susceptible to the negative effects of vibration and misalignment, which can lead to increased leakage and shorter seal life.
Seal Life and Reliability Requirements
Balanced seals generally offer longer seal life and higher reliability, especially in demanding applications with high pressures, temperatures, or shaft speeds.
Unbalanced seals may be sufficient for applications with lower performance requirements or shorter maintenance intervals.
Cost
Balanced seals are typically more expensive than unbalanced seals due to their more complex design and higher performance capabilities.
However, the initial cost should be weighed against the long-term benefits of increased seal life, reliability, and reduced maintenance costs associated with balanced seals in demanding applications. Unbalanced seals may be more cost-effective for less challenging applications with lower performance requirements.
FAQs
How does a balanced seal maintain equal pressure on both sides of the seal faces?
Balanced seals use a stepped shaft sleeve or seal ring to create a hydraulic balance, equalizing the pressure.
What is the typical pressure range for using a balanced mechanical seal?
Balanced seals are generally used for applications with pressures exceeding 100 psi (7 bar).
In conclusion
Understanding the differences between balanced and unbalanced mechanical seals is crucial for selecting the right seal for your application. Consider factors such as pressure, temperature, and media compatibility when making your choice.
Contact our experts today for personalized recommendations tailored to your specific needs.