Have you ever wondered about the difference between buffer fluid and barrier fluid in industrial applications? These fluids play a crucial role in ensuring the efficiency and longevity of mechanical seals.
In this blog post, we’ll break down their functions, benefits, and key differences. By the end, you’ll have a clear understanding of how to choose the right fluid for your specific needs.
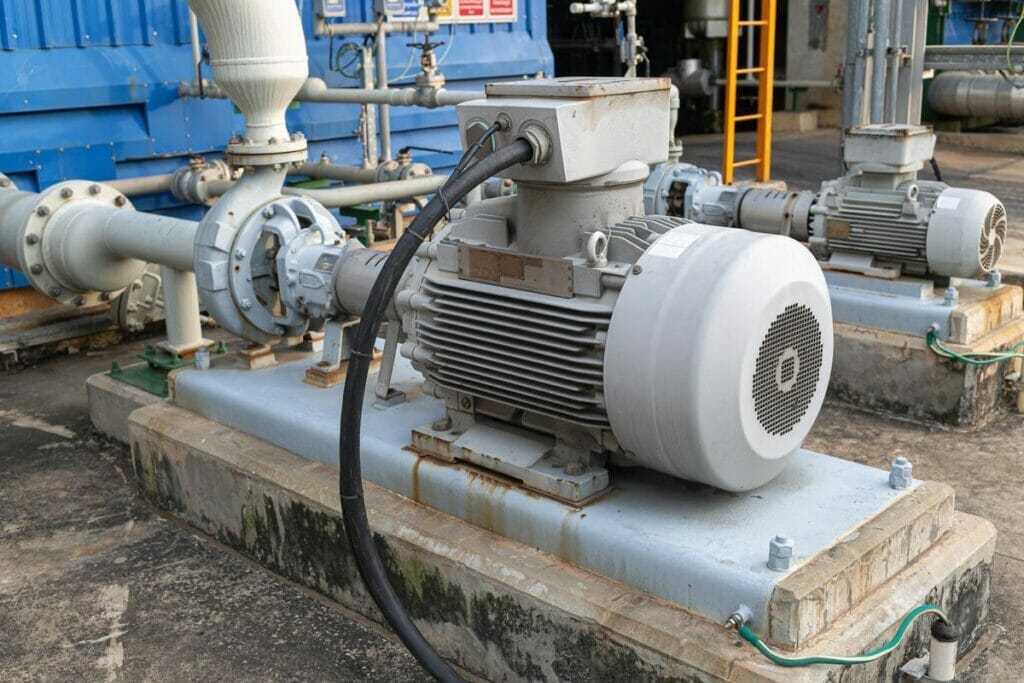
What is Buffer Fluid
Buffer fluid is a type of fluid used in mechanical seal systems, particularly in dual seals and tandem seals. In mechanical seal design, buffer fluid is typically introduced into the seal chamber between the primary seal and the outer seal. This unpressurized seal fluid helps in lubricating the seal faces, reducing frictional heat, and maintaining the integrity of the seal materials.
What is Barrier Fluid
Barrier fluid is a crucial component in mechanical seal systems, specifically used in dual seals or double seals. It serves as a protective fluid layer between the process fluid and the atmosphere, ensuring stable seal performance and preventing fluid leakage.
Barrier fluids are typically pressurized to a level higher than the process fluid. This pressure differential ensures that the barrier fluid remains in the seal chamber, providing superior lubrication to the seal faces. The fluid also acts as a medium for heat transfer, absorbing frictional heat generated between the seal faces and dissipating it away from the seal interface.
Key Differences Between Buffer and Barrier Fluids
Purpose
Buffer fluids are used to maintain pressure in a system. They prevent process fluid from entering the sealing system.
Barrier fluids provide a physical barrier between two fluids. They keep the fluids separated to avoid contamination or mixing.
Pressure
Buffer fluids are typically unpressurized or at a lower pressure than the process fluid.
Barrier fluids are maintained at a higher pressure than the process fluid. This positive pressure differential prevents process fluid from entering the barrier fluid system.
Fluid Composition
Buffer fluids are often compatible with the process fluid. They can be the same fluid or a fluid with similar properties.
Barrier fluids are usually different from the process fluid. They are selected based on their ability to prevent mixing and maintain separation.
System Design
Buffer fluid systems typically have a reservoir to store the buffer fluid. The reservoir is connected to the sealing system.
Barrier fluid systems have a pressurized reservoir or an external pressure source. They also have a circulation system to maintain the barrier fluid’s cleanliness and properties.
Monitoring
Buffer fluid systems require monitoring of fluid levels and pressure. Low levels or pressure changes can indicate seal leaks or other issues.
Barrier fluid systems need monitoring of pressure, temperature, and fluid condition. Changes can indicate process fluid ingress or degradation of the barrier fluid.
Applications
Buffer fluids are commonly used in mechanical seals for pumps and other rotating equipment. They help extend seal life and prevent process fluid leakage.
Barrier fluids are used in double mechanical seals and other critical sealing applications. They provide an extra layer of protection against process fluid leaks and contamination.
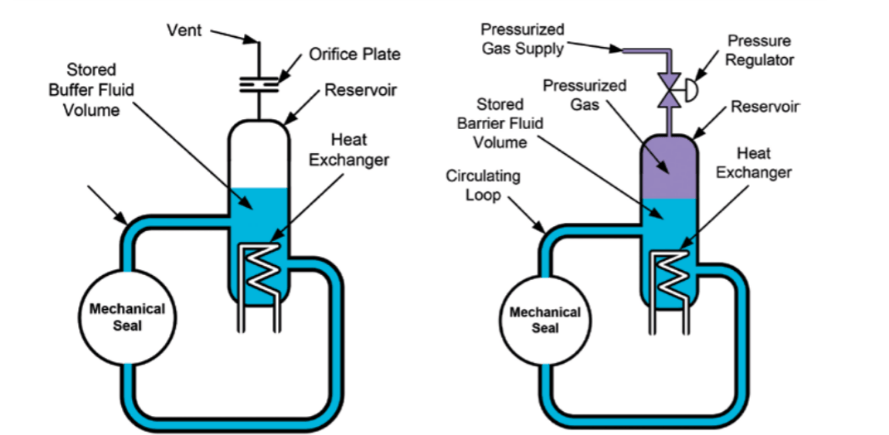
Ideal Characteristics of Buffer and Barrier Fluids
- Safe to Use and Store: Buffer fluids and barrier fluids must be safe for handling and storage. They should not pose any significant health risks to personnel.
- Low Toxicity and Eco-Impact: These fluids should have low toxicity levels and minimal environmental impact.
- Non-Flammable and Chemically Compatible: Fluids must be non-flammable to reduce fire hazards. They should also be chemically compatible with the process fluid and mechanical seal materials.
- Good Viscosity, Lubricity, and Heat Transfer Properties: Ideal buffer and barrier fluids should have appropriate viscosity and superior lubrication qualities. They must also possess good heat transfer properties to manage the frictional heat generated between seal faces.
- Low Foaming, Gas Solubility, and Reactivity: Fluids should exhibit minimal foaming and gas solubility to maintain efficient circulation within the seal chamber. Low reactivity is essential to prevent chemical reactions with seal components and the process fluid.
- Stable Across Operating Temperature Range: These fluids must remain stable across a broad range of temperatures, from ambient conditions to elevated temperatures. Stability ensures consistent performance and prevents fluid degradation, which can lead to seal leakage and premature failure.
- Cost-Effective: Cost-effectiveness is a key consideration. Fluids should provide the necessary properties without excessive cost. This includes considerations for fluid change intervals and maintenance intervals to ensure economic efficiency.
Common Types of Buffer and Barrier Fluids
Water and Water-Glycol Mixtures
Water is a common choice for buffer and barrier fluids. It is readily available and inexpensive. However, plain water may cause corrosion in some systems.
Water-glycol mixtures are used to improve the properties of water as a buffer or barrier fluid. The addition of glycol lowers the freezing point and increases the boiling point of the mixture. This extends the operating temperature range.
Oils (Mineral, Synthetic, PAO, etc.)
Mineral oils are derived from crude oil and are commonly used. They are relatively inexpensive and have good lubricating properties.
Synthetic oils are chemically synthesized and offer superior performance compared to mineral oils. They have better thermal and oxidative stability, allowing for extended fluid life.
Polyalphaolefin (PAO) oils are a type of synthetic oil. They have excellent low and high-temperature properties and are commonly used in demanding applications.
Other Fluids (Alcohols, Thermal Oils, etc.)
Alcohols, such as ethanol and methanol, can be used as buffer or barrier fluids. They have good low-temperature properties and are compatible with many materials.
Thermal oils are used in high-temperature applications. They have high boiling points and provide efficient heat transfer. Thermal oils are often used in heat exchange systems.
The selection of these specialty fluids depends on the unique requirements of the application, such as temperature range, chemical compatibility, and heat transfer properties.
Selection Considerations of Buffer and Barrier Fluids
Mechanical Seal Design and Compatibility
When selecting buffer and barrier fluids, consider the mechanical seal design. The fluid must be compatible with the seal materials and process fluid. This ensures stable seal performance and minimizes fluid leakage. Both buffer and barrier fluids should offer superior lubrication to the seal faces, reducing friction and wear.
Operating Temperature Range
Evaluate the fluid’s ability to perform across a wide range of temperatures. Fluids should remain stable from ambient temperatures to elevated temperatures encountered in the process. Ideal buffer and barrier fluids should have good thermal conductivity and heat transfer properties to manage absorbed heat and frictional heat effectively.
Chemical Properties
The fluid must be chemically compatible with the process streams and seal components. Non-reactive and pure fluids are preferred to avoid chemical reactions that could degrade the seal materials or process fluid. Fluids with low toxicity and minimal environmental impact are ideal, especially in applications involving hazardous air pollutants.
Viscosity and Lubricity
The fluid should have good viscosity and lubricity to maintain adequate seal face lubrication. A range of viscosities is available, and the choice depends on the specific mechanical seal systems and operational temperatures. Fluids with low foaming and gas solubility are preferred to maintain consistent fluid flow and prevent seal leakage.
Pressure Conditions
Consider the fluid pressures in the seal chamber and the mechanical seal configuration. Fluids must withstand extreme pressures without breaking down. Pressure regulators and accumulators like bladder and piston accumulators help maintain consistent pressure levels, ensuring efficient circulation and seal performance.
Heat Transfer Properties
Fluids should have excellent heat transfer properties to manage the heat generated by the seal faces. This includes a high thermal conductivity and the ability to operate within the temperature limits of the seal system. Heat exchangers can be used to maintain optimal fluid temperatures, ensuring peak efficiency and preventing excessive heat buildup.
Cost-Effectiveness
While selecting buffer and barrier fluids, consider the cost-effectiveness of the fluid. This includes not only the initial cost but also the maintenance intervals and the fluid’s lifespan. Fluids that offer a compromise between heat transfer and operational efficiency are preferred for long-term use.
Environmental and Safety Considerations
Safety and environmental impact are crucial. Select fluids that are safe to use and store, with low toxicity and eco-impact. Non-flammable fluids are ideal to reduce the risk of fire hazards. Fluids should also be compliant with environmental regulations and guidelines, such as those outlined in the
In Conclusion
In conclusion, both buffer and barrier fluids play crucial roles in maintaining the efficiency and longevity of mechanical seals in various industrial applications.
For more insights on optimizing your equipment performance, subscribe to our newsletter. Don’t miss out on our expert tips and industry updates!