Have you ever wondered about the differences between carbon and silicon carbide mechanical seals? In this blog post, we’ll dive into the unique properties and applications of each material. By the end, you’ll have a clear understanding of when to choose carbon or silicon carbide for your sealing needs, empowering you to make informed decisions in your projects.
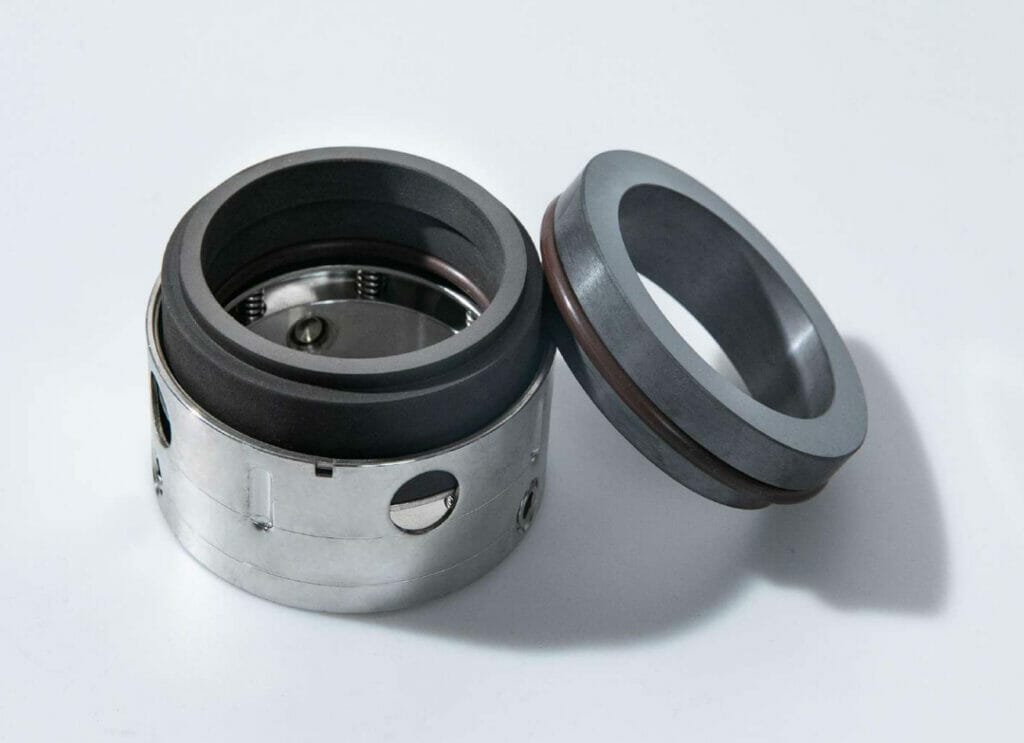
Properties of Carbon Seal Faces
Carbon is a commonly used material for mechanical seal faces due to its unique properties. It offers excellent lubricating characteristics, which help reduce friction and wear between the seal faces during operation. Carbon also exhibits good thermal conductivity, allowing it to dissipate heat efficiently and prevent excessive temperature buildup at the sealing interface.
Another advantage of carbon seal faces is their ability to conform to slight imperfections or misalignments in the mating surface. This adaptability ensures a tight seal and minimizes leakage. Carbon is also resistant to a wide range of chemicals, making it suitable for use in various industrial applications.
Properties of Silicon Carbide Seal Faces
Silicon carbide (SiC) is another popular choice for mechanical seal faces due to its exceptional hardness and wear resistance. SiC seal faces can withstand harsh operating conditions, including high pressures, temperatures, and abrasive media. The material’s high thermal conductivity helps dissipate heat, preventing thermal distortion and maintaining seal integrity.
SiC seal faces also offer excellent chemical resistance, making them suitable for use in corrosive environments. The smooth surface finish of SiC reduces friction and wear, prolonging the life of the mechanical seal. Additionally, SiC’s high modulus of elasticity provides dimensional stability, ensuring the seal faces remain flat and parallel during operation.

Difference Between Carbon and Silicon Carbide
Composition and Structure
Carbon mechanical seals are made from graphite, a form of carbon known for its self-lubricating properties and resistance to heat and chemical attack. The graphite is typically impregnated with resin or metal to enhance its mechanical properties.
Silicon carbide (SiC) is a hard, wear-resistant ceramic material composed of silicon and carbon. It has a crystalline structure that contributes to its excellent hardness, thermal conductivity, and chemical stability.
Hardness and Wear Resistance
Silicon carbide is significantly harder than carbon, with a Mohs hardness of 9-9.5 compared to 1-2 for graphite. This high hardness makes SiC highly resistant to abrasive wear, even in demanding applications with abrasive media.
Carbon seals, while softer, still provide good wear resistance in non-abrasive environments. The self-lubricating nature of graphite helps to reduce friction and wear between the seal faces.
Temperature Resistance
Both carbon and silicon carbide have excellent high-temperature properties. Carbon seals can typically operate at temperatures up to 350°C (662°F), while silicon carbide seals can withstand even higher temperatures, often exceeding 500°C (932°F).
The thermal conductivity of silicon carbide is higher than that of carbon, allowing SiC seals to dissipate heat more effectively and maintain a lower operating temperature at the sealing interface.
Chemical Resistance
Silicon carbide is chemically inert and resistant to attack from most acids, bases, and solvents. It is an excellent choice for sealing highly corrosive or aggressive media.
Carbon also offers good chemical resistance, particularly to organic compounds and non-oxidizing acids and bases. However, it may be less suitable for strongly oxidizing environments or applications with high-pH media.
Cost and Availability
Carbon mechanical seals are generally less expensive than silicon carbide seals due to the lower cost of raw materials and simpler manufacturing processes. Carbon seals are widely available and can be produced in a variety of grades and configurations.
Silicon carbide seals are more specialized and typically come at a higher price point. The production of high-quality SiC components requires advanced manufacturing techniques and strict quality control, contributing to the increased cost.
When to Use Carbon Seal
Carbon seal faces are ideal for applications involving low to moderate pressures and temperatures. They are commonly used in water pumps, mixers, and agitators where the sealing media is not highly abrasive or corrosive. Carbon seals are also suitable for sealing liquids with poor lubricating properties, as the carbon material itself provides lubrication.
In applications with frequent start-stop cycles or where the shaft experiences axial movement, carbon seal faces can accommodate these conditions due to their self-lubricating properties and ability to conform to slight irregularities in the mating surface.
When to Use Silicon Carbide Seal
Silicon carbide seal faces are preferred in applications involving high pressures, temperatures, and abrasive or corrosive media. They are commonly used in demanding industrial processes, such as oil and gas production, chemical processing, and power generation.
SiC seals are also suitable for sealing high-purity fluids, as they do not contaminate the media being sealed. In applications where the sealing media has poor lubricating properties, SiC’s low coefficient of friction and wear resistance make it an excellent choice.
When the mechanical seal is subjected to frequent temperature fluctuations or thermal shocks, SiC’s high thermal conductivity and dimensional stability help maintain seal performance and longevity. Additionally, SiC seals are ideal for applications requiring long service life and minimal maintenance due to their exceptional durability and resistance to wear.
FAQs
Which mechanical seal material is more commonly used?
Carbon is more commonly used in mechanical seals due to its lower cost and adequate performance in many applications.
Can carbon and silicon carbide seals be used interchangeably?
In some cases, yes, but it depends on the specific application requirements, such as temperature, pressure, and fluid compatibility.
In conclusion
When selecting between carbon and silicon carbide mechanical seals, consider the specific application requirements. Silicon carbide offers superior hardness and chemical resistance, while carbon provides better dry running capabilities. For expert guidance on choosing the right seal for your needs, contact a trusted mechanical seal supplier today.