What factors should you consider when selecting mechanical seal materials? Choosing the right materials is crucial for optimal seal performance and longevity.
In this blog post, we’ll guide you through the key considerations for mechanical seal material selection, helping you make informed decisions that will maximize the reliability and efficiency of your sealing system.
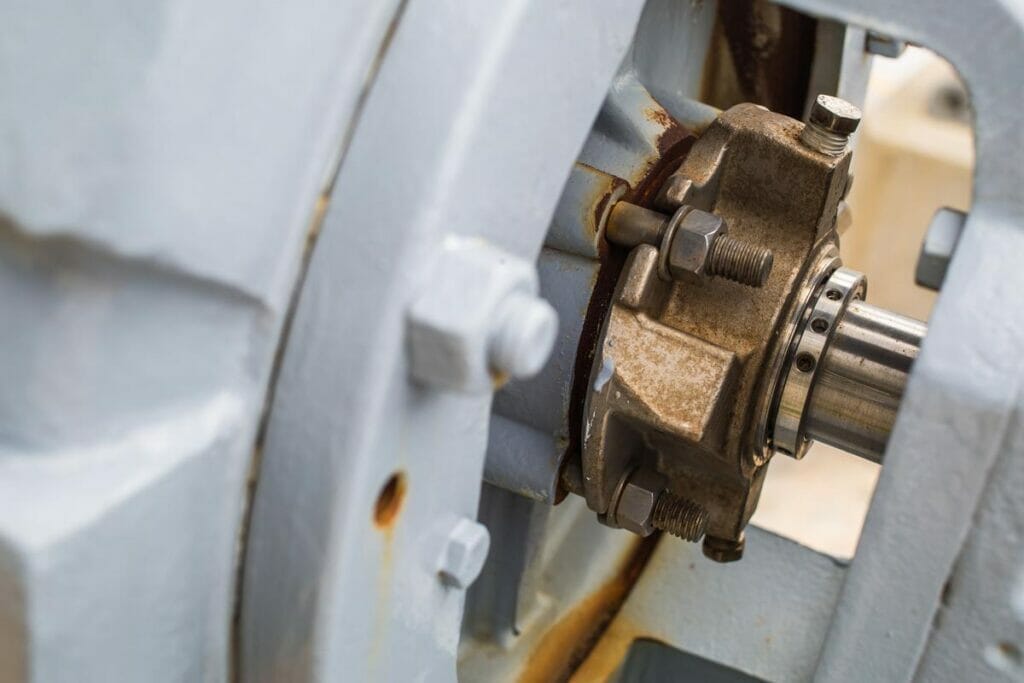
Primary Seal Face Materials
Carbon Graphite Grades
Carbon graphite is a preferred material for seal faces due to its excellent lubricating properties, which help reduce friction and wear. It also exhibits good thermal conductivity, allowing for efficient heat dissipation.
PTFE and Filled PTFE
PTFE, also known as Teflon, is a synthetic fluoropolymer renowned for its low coefficient of friction and non-stick properties. It is chemically inert and resistant to a wide range of chemicals. PTFE can be used in its pure form or filled with various additives such as glass fibers, carbon, or graphite to enhance its mechanical properties and wear resistance.
Ceramic (CER)
Ceramic materials, such as alumina and zirconia, are known for their exceptional hardness, wear resistance, and chemical inertness. They can withstand high temperatures and are suitable for use in corrosive environments. Ceramic seal faces provide excellent sealing performance and long service life.
Silicone Carbide (SiC)
Silicone carbide is a hard, abrasion-resistant material with good thermal conductivity. It offers excellent wear resistance and can operate in high-temperature applications. SiC seal faces are often paired with carbon graphite or other soft materials to form effective sealing pairs.
Tungsten Carbide (TC)
Tungsten carbide is a hard, dense material with high wear resistance and good thermal conductivity. It is often used in demanding applications that require high load-bearing capacity and resistance to abrasion. TC seal faces can be coated with other materials, such as diamond-like carbon (DLC), to further enhance their performance.
Cemented Carbides
Cemented carbides are composite materials consisting of a hard carbide phase, such as tungsten carbide or titanium carbide, bonded together with a metallic binder, typically cobalt or nickel. These materials offer a combination of high hardness, wear resistance, and toughness, making them suitable for heavy-duty sealing applications.
Ni-Resist and Cobalt Alloys
Nickel-resist and cobalt alloys are known for their excellent corrosion resistance and high-temperature stability. They are often used in sealing applications involving aggressive chemicals or elevated temperatures. These alloys provide good wear resistance and can be paired with various soft materials for optimal sealing performance.
Secondary Sealing Elements
FKM
FKM, or fluoroelastomer, is a highly resistant synthetic rubber commonly used as a secondary sealing element in various industrial applications. Known for its excellent chemical resistance, FKM can withstand exposure to a wide range of fluids, including hydrocarbons, acids, and solvents. This material also possesses outstanding heat resistance, maintaining its sealing properties at temperatures up to 400°F (204°C).
EPDM
EPDM (ethylene propylene diene monomer) is a versatile synthetic rubber widely employed as a secondary sealing element. This material offers excellent resistance to water, steam, and various polar fluids, making it suitable for applications in the automotive, HVAC, and plumbing industries.
NBR
NBR (nitrile butadiene rubber) is a popular choice for secondary sealing elements due to its excellent resistance to oils, fuels, and hydraulic fluids. This material is well-suited for applications in the automotive, aerospace, and oil and gas industries, where exposure to hydrocarbons is common.
FFKM
FFKM (perfluoroelastomer) is a high-performance synthetic rubber designed for the most demanding sealing applications. This material offers exceptional chemical resistance, withstanding exposure to aggressive fluids such as concentrated acids, bases, and solvents. FFKM’s temperature resistance is unmatched, with an operating range from -15°F to 600°F (-26°C to 316°C).

Factors Affecting Seal Material Selection
Chemical Compatibility
The primary seal face material must be compatible with the fluid being sealed. Incompatible materials can degrade, swell, or become brittle, leading to premature seal failure. Consider the chemical composition, pH, and any additives in the fluid when selecting a seal material.
Temperature
Ensure that the chosen material can withstand the expected temperature range without significant degradation or loss of sealing ability. Extreme temperatures, both high and low, can affect the material’s properties and performance.
Pressure
The seal material must be capable of withstanding the system pressure. High pressures can cause deformation or extrusion of the seal material, while low pressures may not provide adequate sealing force. Consider the maximum and minimum operating pressures when selecting a seal material.
Viscosity
The viscosity of the fluid being sealed can impact the choice of seal material. Low-viscosity fluids may require a harder, more wear-resistant material to prevent excessive wear, while high-viscosity fluids may need a softer material to conform to the sealing surfaces and maintain a proper seal.
Abrasiveness/Solids Content
Fluids containing abrasive particles or solids can accelerate seal wear. In such cases, harder, more wear-resistant materials like silicon carbide or tungsten carbide may be necessary. Alternatively, softer materials with good embedment properties, such as PTFE or graphite, can be used to prevent damage to the sealing surfaces.
Shaft Size and Speed
The size and speed of the rotating shaft can influence the choice of seal material. Larger shafts and higher speeds generate more heat and require materials with good thermal conductivity and wear resistance. Smaller shafts and lower speeds may allow for the use of softer, more conformable materials.
Seal Chamber Design
The design of the seal chamber, including its dimensions and any special features like barrier fluid ports or quench connections, can impact the choice of seal material. Ensure that the selected material is compatible with the seal chamber design and can be properly installed and maintained.
Regulations and Emissions Standards
Certain industries, such as food processing or pharmaceuticals, have specific regulations governing the materials used in sealing applications. Additionally, environmental regulations may restrict the use of certain materials or require seals with low emissions. Consider any applicable regulations when selecting a seal material.
Reliability and Life Expectations
The expected life and reliability requirements of the sealing system should be considered when choosing a seal material. Some materials may offer longer life or better resistance to specific failure modes, such as chemical degradation or thermal shock. Select a material that can meet the desired reliability and life expectations for the application.
Cost
The cost of the seal material is an important factor in the selection process. While higher-performance materials may offer better reliability and longer life, they may also come at a higher price.
In conclusion
Selecting the right mechanical seal materials is crucial for optimal performance and longevity. Consider the operating conditions, compatibility, and cost when making your choice. Consult with seal manufacturers or industry experts for personalized recommendations. Take action now to ensure your seals are up to the task.