Have you ever wondered what the difference is between mechanical seals and oil seals? While both are designed to prevent leaks, they serve distinct purposes in various applications. In this blog post, we’ll explore the key characteristics, advantages, and use cases of each type of seal, empowering you to make informed decisions when selecting the right sealing solution for your needs.
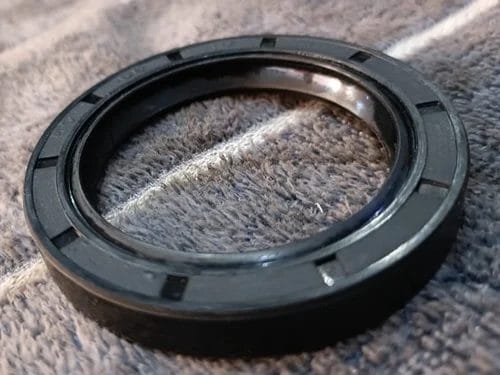
Mechanical Seals
Mechanical seals are specialized sealing devices used in rotating equipment, such as pumps, mixers, and compressors, to prevent leakage of fluids along the rotating shaft. They consist of two main components: a stationary part (stator) and a rotating part (rotor), which form a seal interface when pressed together by spring force and hydraulic pressure.
Oil seals
Oil seals, also known as shaft seals or lip seals, are a type of sealing device used to prevent the leakage of lubricants, such as oil or grease, from rotating equipment while also protecting against the ingress of contaminants. They are commonly found in applications such as gearboxes, engines, and hydraulic systems.
Key Differences Between Mechanical Seals and Oil Seals
Design Differences
Mechanical seals consist of two flat faces, one stationary and one rotating, that are pressed together by springs to create a seal.
Oil seals feature a flexible lip that rides on the shaft to prevent leakage.
Sealing Mechanisms
The sealing mechanism of mechanical seals relies on a thin fluid film maintained between the flat faces. This film prevents direct contact and minimizes wear.
Oil seals seal by allowing the flexible lip to ride on the shaft surface, which can lead to higher friction and wear over time.
Sealing Points
Mechanical seals have three distinct sealing points: a static seal between the stationary components, a rotary seal between the rotating components, and the dynamic seal between the flat faces.
Oil seals only have one sealing point, which is the contact between the lip and the shaft.
Typical Applications
Due to their ability to handle higher pressures and temperatures, mechanical seals are commonly used in demanding applications such as high-pressure pumps, compressors, and reactors.
Oil seals are more suitable for lower-pressure applications, such as gearboxes, engines, and transmissions.
Leakage Rates
Mechanical seals are designed to have very low acceptable leakage rates, often measured in milliliters per day. This is critical for applications where process fluids are expensive, hazardous, or environmentally sensitive.
Oil seals, while still effective, typically have higher acceptable leakage rates compared to mechanical seals.
Pressure Capabilities
Mechanical seals are capable of sealing against much higher pressures than oil seals. They can handle pressures ranging from vacuum to several hundred bar, depending on the design and materials used.
Oil seals are generally limited to lower pressures, typically below 10 bar.
Complexity and Cost
The multi-component design and precise manufacturing requirements of mechanical seals make them more complex and costly than oil seals. Mechanical seals often require specialized installation, monitoring, and maintenance procedures.
Oil seals, with their simpler design, are easier to install and replace and are generally less expensive.
In conclusion
When selecting between mechanical seals and oil seals, consider factors such as the application, environment, and budget. Each type has its advantages and limitations. Choose the seal that best suits your specific requirements. Contact a trusted seal manufacturer for expert guidance in making the right choice.