Have you ever wondered how water reaches the top of tall buildings? The answer lies in multistage centrifugal pumps. These powerful machines use multiple impellers to boost water pressure, enabling liquid to travel vast distances and heights.
In this blog post, we’ll dive into the fascinating world of multistage centrifugal pumps and uncover their essential role in our modern infrastructure.
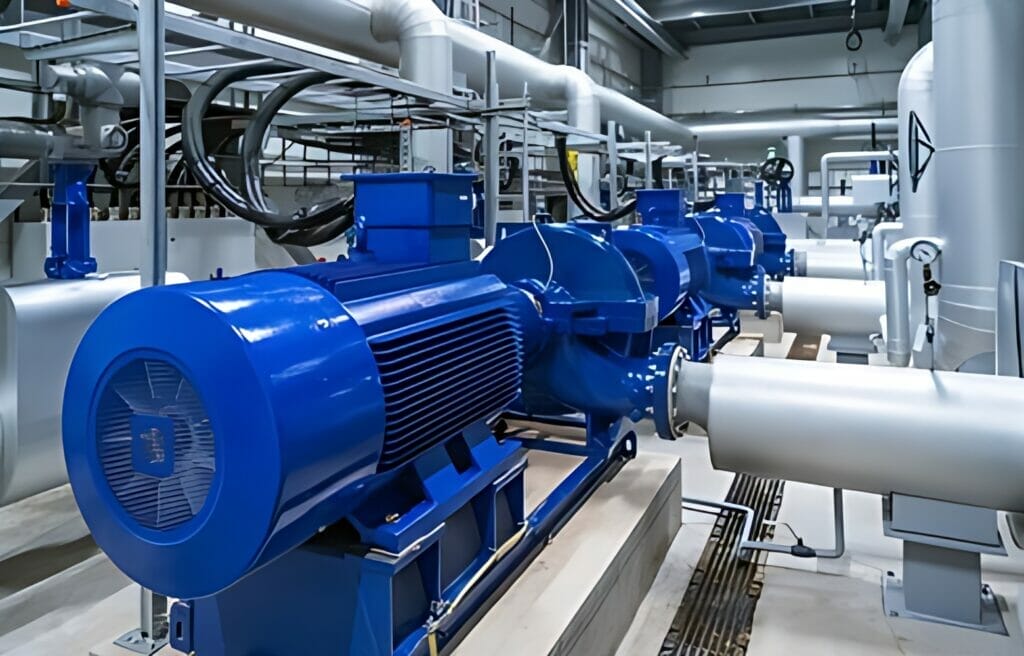
What is a Multistage Centrifugal Pump
A multistage centrifugal pump is a type of pump that uses multiple impellers arranged in series to increase the pressure and flow rate of a fluid. Each impeller is housed in its own casing, called a stage. As the fluid moves through each stage, its pressure and velocity are increased.
Multistage centrifugal pumps are commonly used in applications that require high discharge pressure, such as boiler feed water supply, reverse osmosis systems, and high-pressure cleaning. They are also used in industries such as oil and gas, chemical processing, and power generation.
How Multistage Centrifugal Pumps Work
In a multistage centrifugal pump, the fluid enters the first stage through the suction nozzle and is accelerated by the rotating impeller. The impeller creates centrifugal force, which pushes the fluid outward and into the diffuser.
The diffuser is a stationary component that converts the kinetic energy of the fluid into pressure energy. The fluid then enters the next stage, where the process is repeated. Each subsequent stage further increases the pressure and velocity of the fluid.
The number of stages in a multistage centrifugal pump depends on the required discharge pressure. More stages are added to achieve higher pressures. After the fluid passes through the final stage, it exits the pump through the discharge nozzle.
Components of Multistage Centrifugal Pumps
- Impellers: Rotating components that accelerate the fluid and create centrifugal force. Each stage has its own impeller.
- Diffusers: Stationary components that convert the kinetic energy of the fluid into pressure energy. Each stage has its own diffuser.
- Casing: The outer housing of the pump that contains the impellers, diffusers, and other components. The casing is typically made of metal and is designed to withstand high pressures.
- Shaft: The rotating component that connects the impellers to the motor. The shaft is supported by bearings and sealed to prevent leakage.
- Seals: Components that prevent leakage between the shaft and the casing. Mechanical seals are commonly used in multistage centrifugal pumps.
- Bearings: Components that support the shaft and reduce friction. Bearings are typically lubricated to ensure smooth operation.
Advantages of Multistage Centrifugal Pumps
- High Discharge Pressures: Multistage centrifugal pumps generate high discharge pressures by using multiple impellers in series, boosting the fluid pressure incrementally at each stage.
- Compact Design: These pumps save space by stacking multiple impellers within a single casing, offering a smaller footprint compared to using multiple single-stage pumps in series.
- Excellent Efficiency: The optimized hydraulic design and smooth flow path through the stages minimize energy losses, enhancing efficiency, reducing power consumption, and lowering operating costs.
- Wide Operating Flexibility: They handle a variety of fluids, including clean, slightly contaminated, and low-viscosity fluids.
Disadvantages of Multistage Centrifugal Pumps
- Higher Initial Cost: Multistage centrifugal pumps have a higher initial cost compared to single-stage pumps due to their complex design and additional components.
- Complex Maintenance: These pumps require regular inspection, lubrication, and replacement of wear parts like impellers, seals, and bearings to maintain performance and avoid premature failure.
- Increased Axial Thrust: The increased fluid pressure through each stage can exert axial force on the impellers and shaft, leading to excessive load on bearings and seals if not properly balanced.
- Efficiency Issues: Operating outside their optimal flow range can lead to reduced efficiency, increased hydraulic losses, cavitation, and excessive vibration.
- Susceptibility to Abrasion: Tight clearances between impellers and the casing make these pumps more sensitive to damage from solid particles or abrasive fluids, requiring proper fluid filtration and material selection.
Types of Multistage Centrifugal Pumps
Horizontal Multistage Pumps
Horizontal multistage pumps are designed with multiple impellers arranged in series on a horizontal shaft. The fluid enters the first stage and is progressively pressurized as it passes through each subsequent stage. These pumps are commonly used in applications requiring high pressure, such as boiler feed water systems, reverse osmosis, and high-pressure cleaning.
Vertical Multistage Pumps
Vertical multistage pumps feature multiple impellers mounted on a vertical shaft. The liquid enters at the bottom of the pump and is lifted through each stage by the rotating impellers. As the fluid moves upward, it gains pressure with each stage until it reaches the desired discharge pressure at the top of the pump.
Submersible Multistage Pumps
Submersible multistage pumps are designed to operate fully submerged in the liquid they are pumping. They consist of multiple stages of impellers and a submersible electric motor that is sealed and protected from the liquid. The pump is lowered into the liquid source, such as a well or tank, and the liquid enters the pump at the bottom, passing through each stage before being discharged at the top.
What Is the Difference between a Single Stage Pump and a Multi Stage Pump
Single stage pumps have one impeller and are designed to move fluid through a single stage of pressure increase. They are best suited for lower pressure and head applications.
Multi stage pumps contain two or more impellers arranged in series. The fluid discharged from one impeller flows into the suction of the next impeller, with each stage further increasing the pressure. This allows multi stage pumps to generate higher pressures and work against greater head than single stage pumps.
In conclusion
Multistage centrifugal pumps are powerful and efficient devices for moving fluids in various industries. Their unique design and multiple impellers allow for high pressure and flow rates.
To learn more about how multistage centrifugal pumps can benefit your application, contact a trusted pump supplier today.