Have you ever wondered about the differences between PTFE and graphite packing materials? In this blog post, we’ll explore the unique properties and applications of each type. By the end, you’ll have a clear understanding of when to use PTFE or graphite packing in your projects, enabling you to make informed decisions and achieve optimal results.
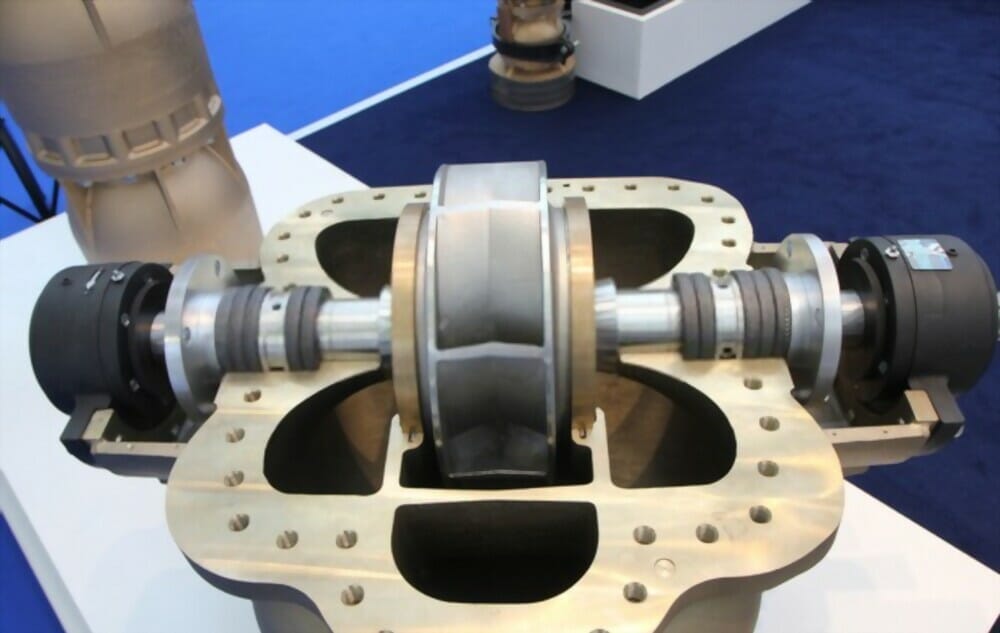
Key Differences Between Graphite Packing and PTFE Packing
Composition and Structure
Graphite packing is made from high-purity graphite, which has a layered, crystalline structure. This structure allows for easy sliding between layers, contributing to its lubricating properties.
PTFE packing is composed of polytetrafluoroethylene, a synthetic fluoropolymer known for its low friction and high chemical resistance. PTFE has a more amorphous structure compared to graphite.
Coefficient of Friction
Graphite packing has a relatively higher coefficient of friction compared to PTFE packing. This means that graphite packing may experience more resistance when in contact with moving surfaces.
PTFE packing, known for its “slippery” properties, exhibits a significantly lower coefficient of friction, making it ideal for applications requiring minimal resistance and smooth movement.
Thermal Conductivity
Graphite packing has a higher thermal conductivity than PTFE packing. This property allows graphite to effectively transfer heat away from the sealing area, making it suitable for applications involving high temperatures.
PTFE packing, while stable at high temperatures, has lower thermal conductivity and may not dissipate heat as efficiently as graphite packing.
Tensile Strength and Abrasion Resistance
PTFE packing generally has higher tensile strength and better abrasion resistance compared to graphite packing. This makes PTFE packing more durable and resistant to wear when subjected to high stresses and abrasive conditions.
Graphite packing, although strong, may be more prone to wear and damage in highly abrasive environments.
Self-Lubrication
Both graphite and PTFE packings exhibit self-lubricating properties. Graphite packing relies on its layered structure, allowing the layers to slide easily against each other and provide lubrication.
PTFE packing’s low friction properties enable it to self-lubricate, reducing the need for external lubricants. However, PTFE packing generally provides better self-lubrication compared to graphite packing.
Pressure Tolerance
Graphite packing can typically withstand higher pressures compared to PTFE packing. The unique structure of graphite allows it to compress and conform to sealing surfaces, maintaining a tight seal even under high-pressure conditions.
PTFE packing, while still effective at sealing, may have limitations in extremely high-pressure applications.
Chemical Resistance and Stability
PTFE packing is known for its exceptional chemical resistance and stability. It can withstand exposure to a wide range of chemicals, including acids, bases, and solvents, without degradation.
Graphite packing, while resistant to many chemicals, may not have the same level of chemical compatibility as PTFE, especially in highly corrosive environments.
Temperature Limits
Both graphite and PTFE packings have wide temperature operating ranges. Graphite packing can typically withstand temperatures up to 650°F (343°C) in oxidizing environments and even higher in non-oxidizing conditions.
PTFE packing is stable from cryogenic temperatures up to around 500°F (260°C).
Sealability and Leakage Control
Graphite packing, due to its ability to conform to sealing surfaces and withstand high pressures, often provides excellent sealability and leakage control. It can effectively prevent fluid leakage and maintain a tight seal over time.
PTFE packing also offers good sealability, but its performance may be slightly lower compared to graphite packing, especially in high-pressure applications.
Shaft Speed Limits
PTFE packing is well-suited for applications involving high shaft speeds. Its low friction properties allow for smooth rotation and minimal heat generation, even at elevated speeds.
Graphite packing, with its higher coefficient of friction, may have lower shaft speed limits compared to PTFE packing to prevent excessive heat buildup and wear.
Shaft Wear and Damage Potential
PTFE packing, being softer and more malleable than graphite packing, is less likely to cause shaft wear or damage. Its low friction properties and ability to conform to shaft surfaces minimize the risk of abrasion or scoring.
Graphite packing, while still relatively gentle on shafts, may have a slightly higher potential for wear due to its higher coefficient of friction.
Applications
Graphite packing finds applications in high-temperature, high-pressure, and chemically demanding environments, such as in valves, pumps, and steam systems.
PTFE packing is widely used in applications requiring low friction, chemical resistance, and high shaft speeds, including rotary seals, reciprocating pumps, and food processing equipment.
Cost
In general, graphite packing tends to be less expensive than PTFE packing due to the lower cost of raw materials and simpler manufacturing processes.
FAQs
Which packing material is more environmentally friendly?
PTFE packing is considered more environmentally friendly than graphite packing, as it does not contain any hazardous materials and is recyclable.
In conclusion
Both PTFE and graphite packing have unique advantages for different applications. Consider factors such as temperature, chemical compatibility, and pressure when selecting the right packing material. Consult with a trusted supplier to find the optimal solution for your specific needs and ensure the best performance.