Have you ever wondered what a pumping ring in a mechanical seal does? This small but crucial component plays a vital role in ensuring the smooth operation of your sealing system.
In this blog post, we’ll explore the purpose and function of pumping rings, helping you understand how they contribute to the overall performance and reliability of your mechanical seals.
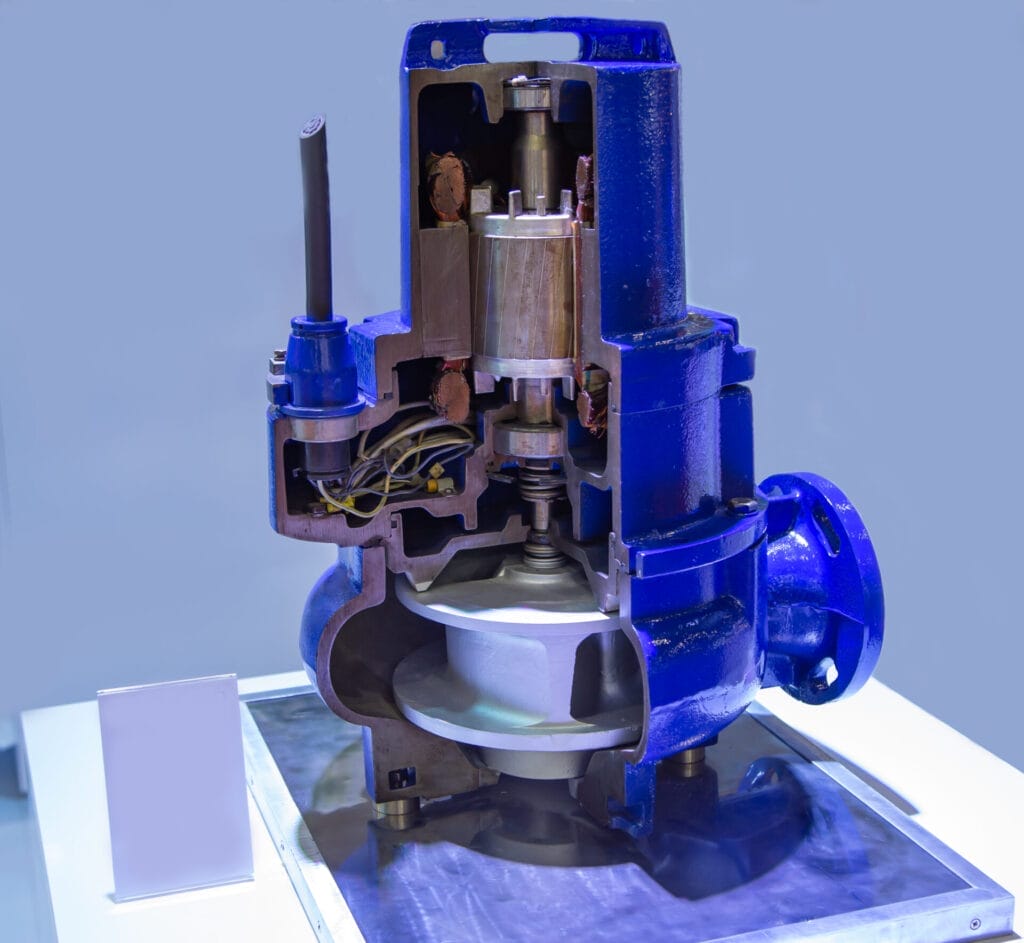
What Is Pumping Ring in Mechanical Seal
A pumping ring is a ring-shaped device that is installed in the seal chamber, typically made from a flexible material such as PTFE or other polymers. The primary purpose of the pumping ring is to enhance the performance and longevity of the mechanical seal by improving fluid circulation within the seal chamber.
How Pumping Rings Work
The pumping action of the pumping ring is driven by the rotation of the shaft. As the shaft rotates, it causes the pumping ring to rotate as well. The grooves or vanes on the surface of the pumping ring are angled in a specific direction, typically at a 45-degree angle.
As the pumping ring rotates, the angled grooves or vanes create a centrifugal force that acts on the fluid within the seal chamber. This centrifugal force causes the fluid to move from the inner diameter of the seal towards the outer diameter. The fluid is then directed back towards the inner diameter, creating a continuous circulation pattern.
Function of Pumping Ring in Mechanical Seal
- Flow control: The pumping ring creates a restriction in the flow path, regulating the flow of the sealed fluid and minimizing turbulence and vortexing within the stuffing box.
- Lubrication and cooling: By directing the sealed fluid toward the mechanical seal faces, the pumping ring ensures adequate lubrication and cooling of the sealing interface.
- Pressure maintenance: The pumping action helps to maintain a higher pressure in the stuffing box compared to the atmospheric pressure. This prevents the ingress of air or vapors into the sealing interface.
- Debris removal: The continuous flow of fluid through the stuffing box, facilitated by the pumping ring, helps to flush away debris and contaminants from the sealing interface.
Types of Pumping Ring
Radial Flow
Radial flow designs in mechanical seal pumping rings are characterized by the fluid moving perpendicular to the shaft axis. These designs include drilled vane impellers, slotted impellers, and paddle-wheel configurations.
Drilled Vane Impellers
Drilled vane impellers are a type of radial flow pumping ring used in mechanical seals. These impellers feature a series of precisely drilled holes or vanes that are evenly distributed around the circumference of the ring. As the impeller rotates, the vanes create a centrifugal force that propels the fluid outward, generating a pumping action.
Slotted Impellers
Slotted impellers are another variation of radial flow pumping rings commonly used in mechanical seals. These impellers feature a series of slots or grooves that are machined into the surface of the ring, typically in a radial or spiral pattern. As the impeller rotates, the slots guide the fluid outward from the center of the seal, creating a pumping effect.
Paddle-Wheel
Paddle-wheel are a distinct type of radial flow pumping ring that resembles the appearance of a traditional water wheel. These impellers feature a series of radially extending paddles or blades that are attached to a central hub. As the impeller rotates, the paddles scoop and propel the fluid outward, creating a strong pumping action.
Axial Flow
Axial flow designs in mechanical seal pumping rings involve fluid movement parallel to the shaft axis. Two common axial flow configurations are spiral groove pumping rings and bi-directional tapered pumping rings.
Spiral Groove
Spiral groove pumping rings feature a series of angled grooves or channels machined into the surface of the pumping ring. These grooves are designed to direct the fluid along the shaft axis as the ring rotates, generating an axial pumping action. The geometry and arrangement of the grooves can be optimized to enhance pumping performance and efficiency.
Bi-directional Tapered
Bi-directional tapered pumping rings have a tapered profile that allows them to generate an axial pumping effect in both directions along the shaft. This design is particularly useful in applications where the shaft may rotate in both clockwise and counterclockwise directions. The tapered profile helps to maintain a consistent pumping action regardless of the direction of rotation.
FAQs
Are pumping rings used in all mechanical seals?
No, pumping rings are typically used in single and double mechanical seals, but not in all seal designs. Some seals rely on other methods for fluid circulation.
Can a damaged pumping ring be replaced?
Yes, a damaged pumping ring can often be replaced without replacing the entire mechanical seal, depending on the seal design and accessibility.
What happens if a pumping ring fails?
If a pumping ring fails, fluid circulation within the seal chamber may be compromised, leading to increased heat buildup, accelerated wear, and potentially premature seal failure.
Can a pumping ring be retrofitted to an existing mechanical seal?
In some cases, a pumping ring can be retrofitted to an existing mechanical seal, but this depends on the seal design and compatibility. Consult with a mechanical seal expert for guidance.
In conclusion
The pumping ring is a crucial component in mechanical seals that helps maintain the seal’s integrity and extend its lifespan. For more information on pumping rings and their role in mechanical seals, contact a trusted seal manufacturer or supplier to discuss your specific needs.