Have you ever wondered why pumps require seal water? In this blog post, we’ll explore the crucial role that seal water plays in maintaining the efficiency and longevity of pumps. By understanding the importance of seal water, you’ll be better equipped to ensure your pumps operate at their best, saving you time and money in the long run.
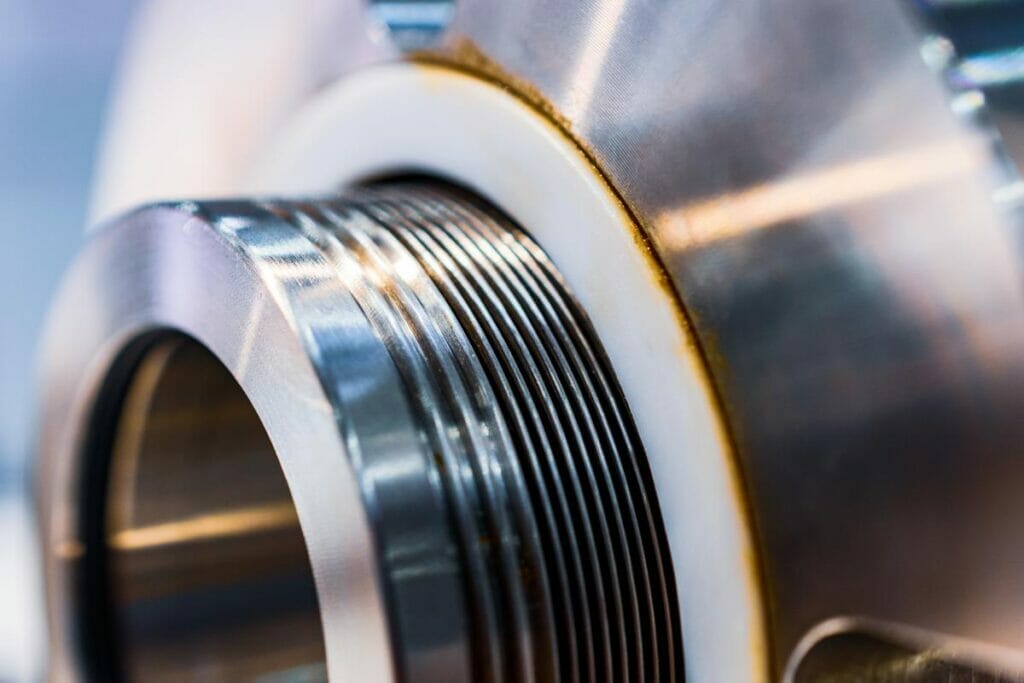
What is Seal Water
Seal water is a crucial component in the operation of pumps, particularly those handling high-temperature or abrasive fluids. It is a clean, cool liquid, usually water, that is injected into the seal chamber of a pump. The seal water serves to lubricate, cool, and flush the mechanical seal, which is responsible for preventing leakage along the pump shaft.
The Purpose of Seal Water
Cooling the Seal Faces and Shaft
The continuous flow of cool water through the seal chamber removes heat generated by friction between the rotating and stationary components. This cooling effect is essential for maintaining the integrity of the seal materials and preventing thermal damage, especially in high-temperature applications.
Lubricating the Interface Between the Seal Faces
Seal water acts as a lubricant between the seal faces, reducing friction and wear. The thin film of water between the faces allows them to slide smoothly against each other, minimizing the risk of damage and extending the seal’s lifespan.
Flushing Away Contaminants and Debris
As the seal water flows through the seal chamber, it carries away any foreign particles that may have entered the system, preventing them from accumulating between the seal faces. This flushing action helps to maintain a clean sealing environment and reduces the risk of seal damage caused by abrasive particles.
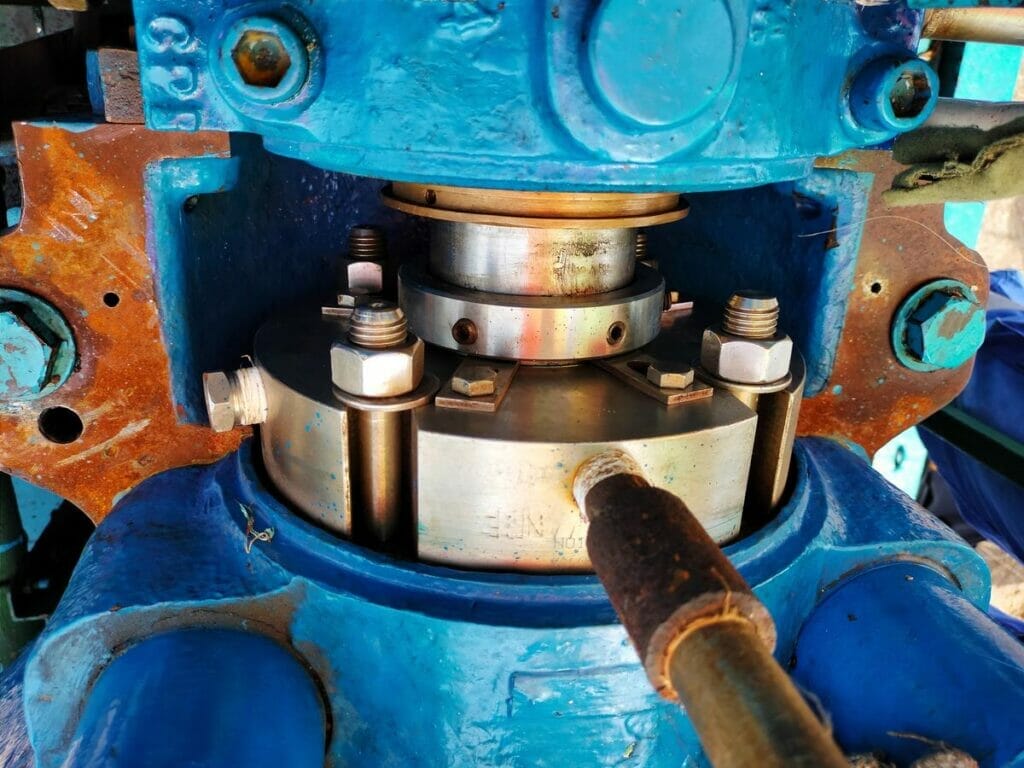
How Seal Water Works in Different Seal Types
Gland Packing Seals
Gland packing seals require a significant amount of seal water to function properly. The water serves multiple purposes, including cooling the packing material to prevent overheating and “burning.”
Additionally, the flowing water helps to flush away any particles or debris that may accumulate near the seal, which could otherwise cause damage or leakage.
Single Mechanical Seals
The water provides essential cooling to the seal faces, preventing overheating and excessive wear. Moreover, the seal water acts as a lubricant between the seal faces, reducing friction and minimizing the risk of damage.
By maintaining a consistent flow of clean, cool water to the seal faces, single mechanical seals can operate efficiently and reliably.
Double Mechanical Seals
Double mechanical seals utilize a barrier fluid, typically seal water, that is introduced between the two seal faces. This barrier fluid serves several important functions.
Firstly, it provides cooling to the seal faces, preventing overheating and thermal damage.
Secondly, the barrier fluid lubricates the seal faces, reducing friction and wear.
Lastly, the presence of the barrier fluid helps to prevent contamination of the sealed fluid by creating a physical barrier between the process fluid and the atmosphere.
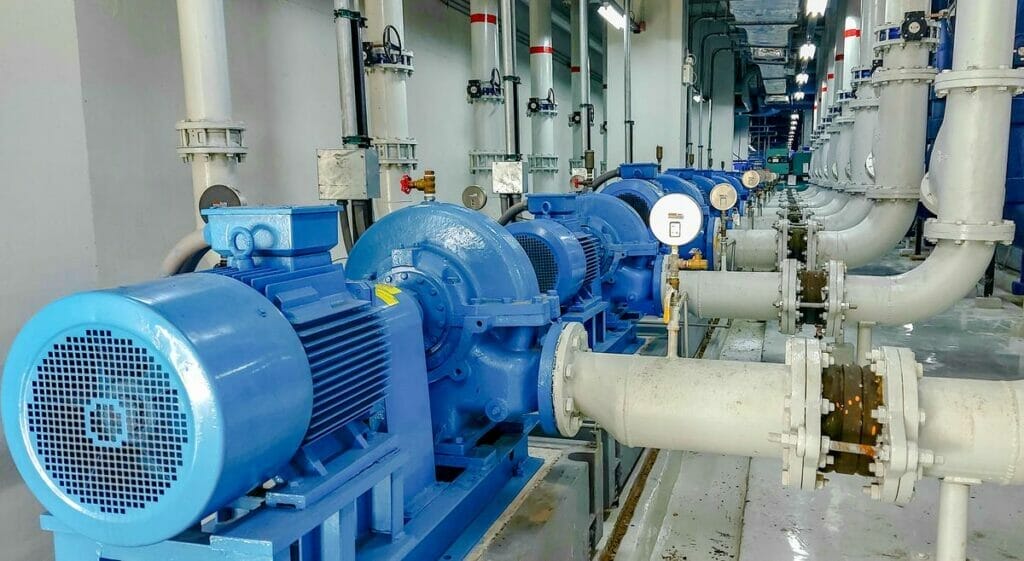
Optimizing Seal Water Usage
Proper Specification of Seal Water Requirements
Flow rate should be sufficient to cool and lubricate the seal faces without causing excessive wear.
Pressure must be high enough to maintain a positive differential across the seal faces.
Temperature should be controlled to prevent thermal shock and maintain stable seal dimensions.
Proper filtration is essential to prevent particulate damage to seal faces.
Flow Control Devices for Seal Water Optimization
Flow control devices such as needle valves, flow meters, and cyclical timers can significantly optimize seal water usage.
Needle valves allow precise adjustment of flow rate to match seal requirements.
Flow meters provide accurate monitoring of seal water consumption, enabling early detection of leaks or excessive flow.
Cyclical timers can be employed to automatically regulate seal water flow based on pump operating conditions, reducing water consumption during idle periods.
Benefits of Smart Seal Water Control Systems
Smart seal water control systems offer numerous advantages over manual control methods. These systems continuously monitor seal water pressure, temperature, and flow rate, automatically adjusting flow to maintain optimal conditions.
This real-time regulation minimizes water consumption while ensuring proper seal lubrication and cooling.
Smart systems can also alert operators to abnormal conditions, enabling proactive maintenance to prevent seal failures and extend pump life.
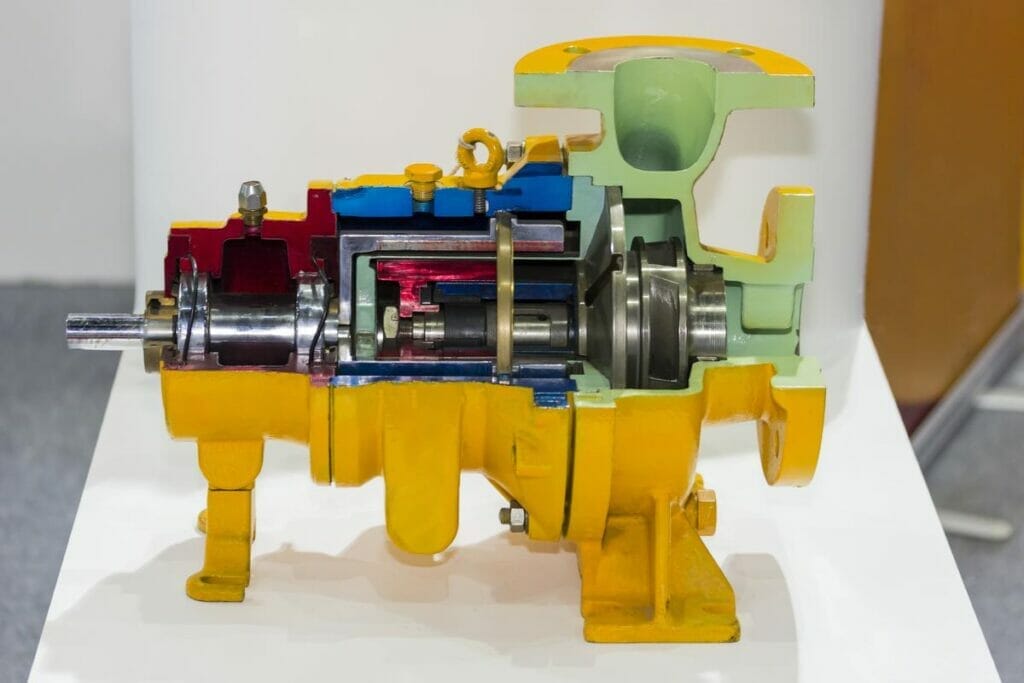
Challenges and Risks of Improper Seal Water Usage
Excessive Water Consumption and Costs
When the flow rate is not properly regulated, pumps may use more water than required for effective sealing and cooling. This not only wastes a valuable resource but also increases operational expenses.
Abrasive Wear and Overheating Risks
When the flow rate is too low, the seals may not receive adequate lubrication and cooling. This can result in increased friction and abrasive wear on the sealing surfaces. Moreover, the lack of proper cooling can cause the seals to overheat, leading to premature failure and unplanned downtime.
Process Fluid Dilution Concerns
If the seal water mixes with the pumped medium, it can dilute the process fluid, altering its composition and properties. This dilution can impact product quality, reaction kinetics, and downstream operations.
Environmental and Wastewater Handling Issues
The excess water must be properly collected, treated, and disposed of in compliance with local regulations. This additional wastewater stream increases the burden on treatment facilities and may require additional infrastructure and resources.
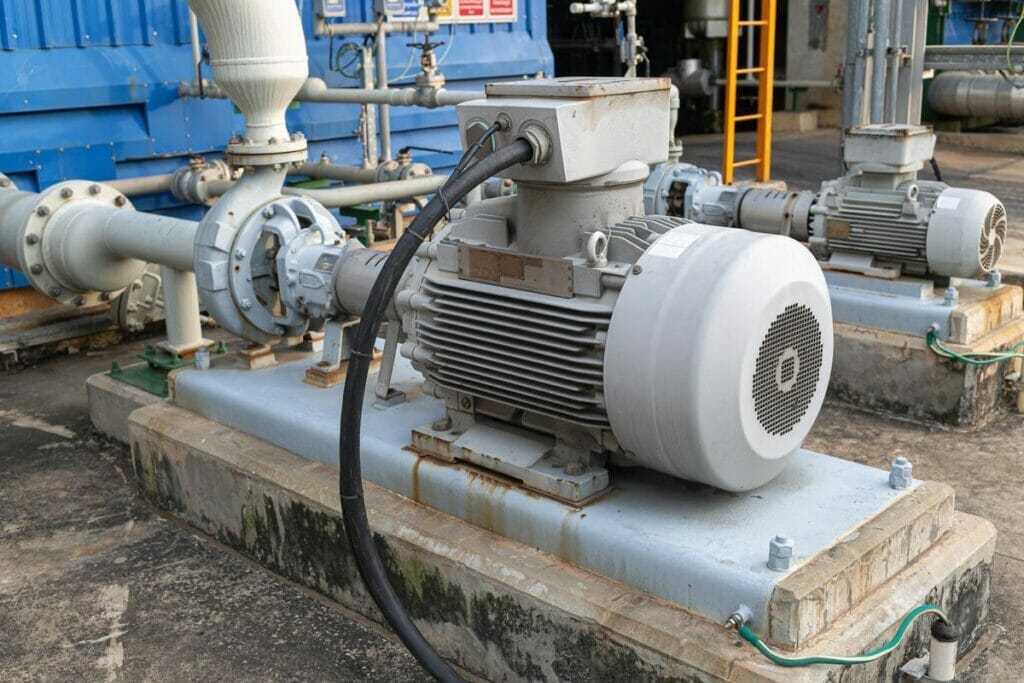
What Is the Difference between Gland Water and Seal Water
Gland Water
Gland water, also known as flush water or quench water, is used to seal and lubricate the packing gland in a pump. The packing gland is a chamber that houses the packing material, which creates a seal around the pump shaft to prevent leakage. Gland water is introduced into the packing gland to keep the packing material cool, lubricated, and free from contaminants. This helps to extend the life of the packing and maintain an effective seal.
Seal Water
Seal water is used in mechanical seals to cool the seal faces and equalize the pressure across the seal. Mechanical seals are a type of sealing device that consists of two flat surfaces (seal faces) that rotate against each other to create a seal. Seal water is circulated through the seal chamber to remove heat generated by friction and to maintain a constant pressure on both sides of the seal faces. This prevents the process fluid from entering the atmosphere and helps to prolong the life of the mechanical seal.
FAQs
What happens if a pump runs without seal water or inadequate seal water supply?
Running a pump without seal water can cause the seals to overheat, leading to rapid wear, leakage, and ultimately, seal failure and pump damage.
Can pumps operate with fluids other than water for seal lubrication?
In some cases, pumps can use other clean, compatible fluids for seal lubrication, such as oil or glycol-based solutions, depending on the application and seal material.
How is seal water pressure maintained in a pump?
Seal water pressure is typically maintained by a separate seal water system, which includes a reservoir, pressure regulating valve, and flow control devices to ensure proper pressure and flow to the seals.
What is the ideal seal water pressure for a pump?
The ideal seal water pressure is typically 10-15 psi (0.7-1 bar) above the pump’s maximum operating pressure to ensure adequate lubrication and cooling without overloading the seals.
How much seal water flow is required for a pump?
Seal water flow requirements depend on factors such as pump size, speed, and operating conditions, but typically range from 0.5 to 3 gallons per minute (1.9 to 11.4 liters per minute).
Can seal water be recycled in a pumping system?
Yes, seal water can be recycled through a closed-loop system with proper filtration, cooling, and pressure regulation to minimize water consumption and environmental impact.
In conclusion
Seal water is essential for the proper functioning and longevity of pumps. It prevents leakage, lubricates moving parts, and maintains pump efficiency. To learn more about pump maintenance and seal water systems, consult with a trusted pump specialist or explore additional resources on the topic.