Have you ever wondered how mechanical seals prevent leaks in rotating equipment? Mechanical seals have several critical sealing points that ensure reliable operation and minimize fluid loss.
In this blog post, we’ll explore these sealing points in detail, helping you understand how they work together to maintain the integrity of your machinery and safeguard your processes.
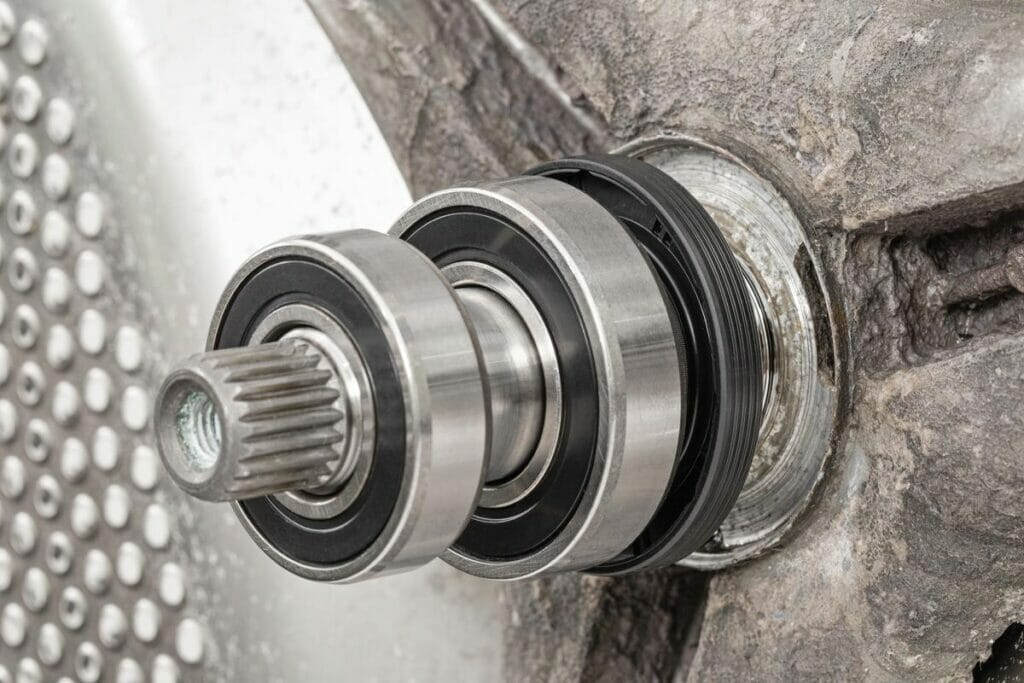
The Three Main Sealing Points
Primary Seal Interface between Rotating and Stationary Faces
The primary seal interface is the most critical sealing point in a mechanical seal. It is located between the rotating and stationary faces of the seal. These faces are precision-machined and lapped to create a flat, smooth surface that allows them to mate together with minimal leakage.
The rotating face is typically made of a hard, wear-resistant material such as silicon carbide, tungsten carbide, or ceramic. The stationary face is usually made of a softer material such as carbon graphite or silicon carbide. The faces are held together by a combination of hydraulic and spring forces, which create a thin fluid film between them.
Static Seal Between Stationary Component and Seal Housing
The static seal between the stationary component and the seal housing is another important sealing point. This seal prevents leakage between the stationary face and the seal housing.
The static seal is typically an O-ring or gasket made of elastomeric material such as nitrile rubber or fluoroelastomer. The O-ring or gasket is compressed between the stationary face and the seal housing to create a leak-tight seal.
Static Seal Between Rotating Component and Shaft
The static seal between the rotating component and the shaft is the final sealing point in a mechanical seal. This seal prevents leakage between the rotating face and the shaft.
The rotating component is typically a sleeve or collar that fits over the shaft. The static seal is usually an O-ring or V-ring that is compressed between the sleeve and the shaft. The material of the O-ring or V-ring depends on the application and can be made of nitrile rubber, fluoroelastomer, or other elastomeric materials.
Factors affecting the performance of sealing points
Seal Face Materials
The chosen materials must possess the necessary hardness, wear resistance, and chemical compatibility to withstand the demands of the specific application.
Surface Finish and Flatness
A smooth and flat surface ensures proper contact between the sealing faces, minimizing leakage and wear. Manufacturers employ precise machining and lapping techniques to achieve the desired surface finish and flatness. Irregularities or imperfections on the sealing faces can lead to increased leakage and reduced seal life.
Seal Face Pressure and Contact
Sufficient contact pressure is necessary to prevent leakage, while excessive pressure can cause accelerated wear and heat generation. The balance between seal face pressure and contact is achieved through proper spring loading and hydraulic pressure management.
Lubrication and Cooling
Lubricating fluids, such as oil or grease, reduce friction and wear between the sealing faces. Cooling mechanisms, such as fluid circulation or heat dissipation features, help manage the heat generated during operation. Proper lubrication and cooling minimize thermal distortion, maintain stable running conditions, and extend the service life of the sealing components.
Environmental Factors
Extreme temperatures can cause thermal expansion or contraction, affecting the clearances and contact between sealing faces. High pressures can lead to increased stress on the sealing components, while aggressive chemicals can degrade seal materials over time.
FAQs
What is the role of lubrication in mechanical seal sealing points?
Lubrication between the sealing faces is crucial to reduce friction, heat generation, and wear, which helps to maintain the integrity of the sealing points and extend seal life.
How often should mechanical seal sealing points be inspected?
Typically every 2-6 months, depending on the application and seal type.
In conclusion
Understanding the sealing points of mechanical seals is crucial for ensuring proper function and preventing leaks. By carefully considering the primary and secondary sealing points, you can select the right seal for your application. Contact our experts today to discuss your specific sealing requirements and find the optimal solution.