Are you struggling with mechanical seal leakage in your industrial equipment? Leaking seals can lead to costly downtime and repairs.
In this ultimate guide, we’ll walk you through the common causes of seal leakage and provide practical solutions to help you troubleshoot and fix the issue.
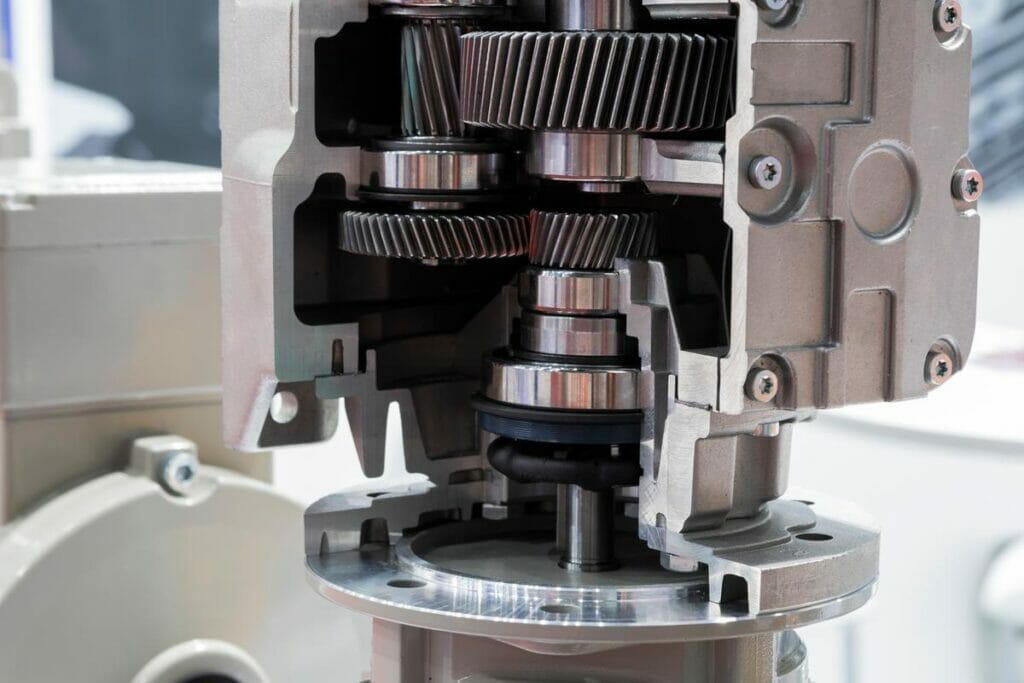
Mechanical Damage and Fatigue
Shaft Misalignment and Eccentricity
Misalignment occurs when the shaft is not properly aligned with the seal faces, causing uneven wear and damage. Eccentricity happens when the shaft is not perfectly centered within the seal, leading to excessive vibration and seal face contact.
To prevent these issues, ensure proper shaft alignment during installation and maintain it through regular checks. Use precision alignment tools and techniques to minimize misalignment and eccentricity.
Excessive Shaft Deflection and Vibration
Deflection occurs when the shaft bends or flexes under load, while vibration is caused by imbalanced rotating components or external forces.
Both deflection and vibration can cause the seal faces to open and close rapidly, leading to accelerated wear and leakage. To mitigate these problems, ensure proper shaft sizing and stiffness, balance rotating components, and isolate the seal from external vibration sources.
Bearing Failures and Shaft/Sleeve Damage
Worn or damaged bearings can cause shaft misalignment, vibration, and excessive runout, while shaft or sleeve damage can create an uneven sealing surface.
Regular bearing maintenance and replacement, along with proper shaft and sleeve protection, can help prevent these issues. Inspect the shaft and sleeve surfaces for damage and repair or replace as necessary.
Seal Face Chipping, Cracking, and Thermal Shock
Chipping and cracking can result from mechanical impact, foreign objects, or excessive stress, while thermal shock occurs when the seal faces are subjected to rapid temperature changes.
To prevent seal face damage, handle seals carefully during installation, ensure proper seal selection for the application, and avoid sudden temperature changes during operation.
Drive Collar Looseness and Set Screw Galling
Drive collar looseness and set screw galling can cause the seal to rotate inconsistently or not at all, leading to leakage and damage. A loose drive collar can allow the seal to wobble or tilt, while galled set screws can prevent the collar from gripping the shaft securely.
Ensure that the drive collar is properly tightened and secured to the shaft, and use appropriate anti-seize compounds on set screws to prevent galling. Regularly inspect the drive collar and set screws for looseness or damage.
Spring Clogging and Breakage
Spring clogging and breakage can compromise the mechanical seal’s ability to maintain proper face contact and alignment. Clogged springs can prevent the seal faces from closing fully, while broken springs can cause the seal to lose compression and leak.
To prevent spring issues, ensure that the seal is properly specified for the application and operating conditions. Regularly inspect the springs for signs of clogging or damage, and replace them as needed. Consider using spring-less seal designs for applications prone to clogging or corrosion.
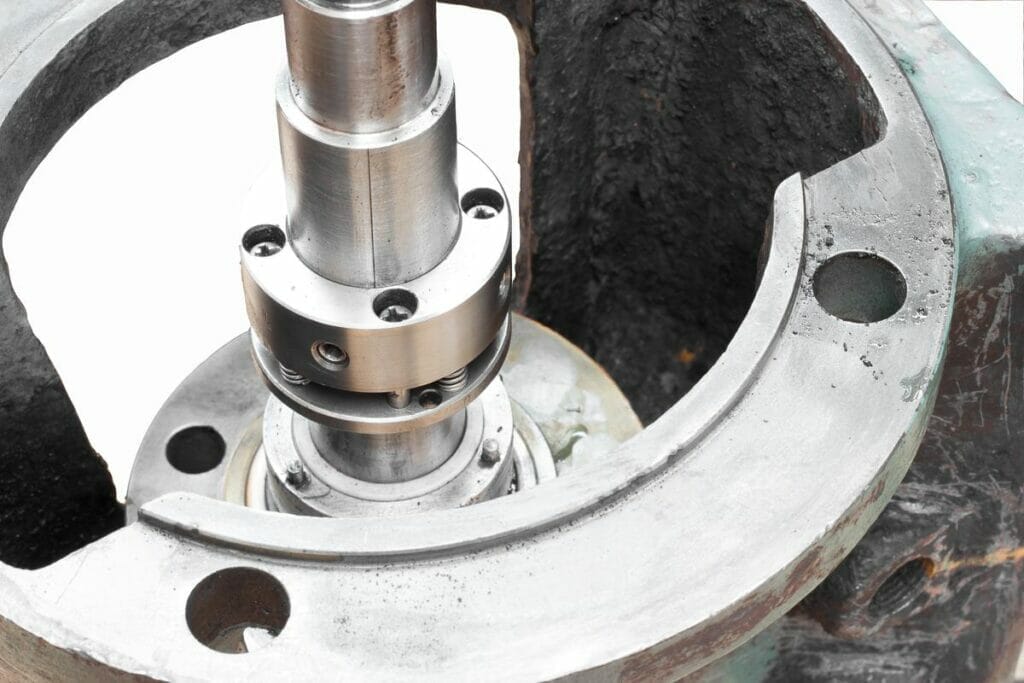
Degradation from Challenging Process Fluids
Abrasive Wear from Slurries and Particulates
Mechanical seals are susceptible to abrasive wear when exposed to process fluids containing slurries or particulates. These abrasive materials can cause rapid deterioration of the seal faces, leading to increased leakage and reduced seal life.
To mitigate abrasive wear, consider using harder seal face materials such as silicon carbide or tungsten carbide. Additionally, ensure proper filtration of the process fluid to remove abrasive particles.
Chemical Attack
Certain process fluids can chemically attack the materials used in mechanical seals, causing degradation and eventual leakage. Chemical attack can lead to softening, swelling, or cracking of seal components, compromising their ability to maintain a proper seal.
To prevent chemical attack, select seal materials that are compatible with the specific process fluid. In some cases, using a barrier fluid or buffer fluid can help isolate the seal from aggressive process fluids.
Flashing and Cavitation
Flashing and cavitation can occur when the pressure of the process fluid drops below its vapor pressure, causing the fluid to vaporize and form bubbles. When these bubbles collapse near the seal faces, they can cause severe erosion and damage, leading to increased leakage.
To prevent flashing and cavitation, ensure that the seal is operating within its recommended pressure and temperature range. In applications prone to flashing or cavitation, consider using seal faces with special geometries or materials that are more resistant to erosion. For example, using a flow-through design or incorporating a cyclone separator can help minimize the impact of flashing and cavitation on the seal faces.
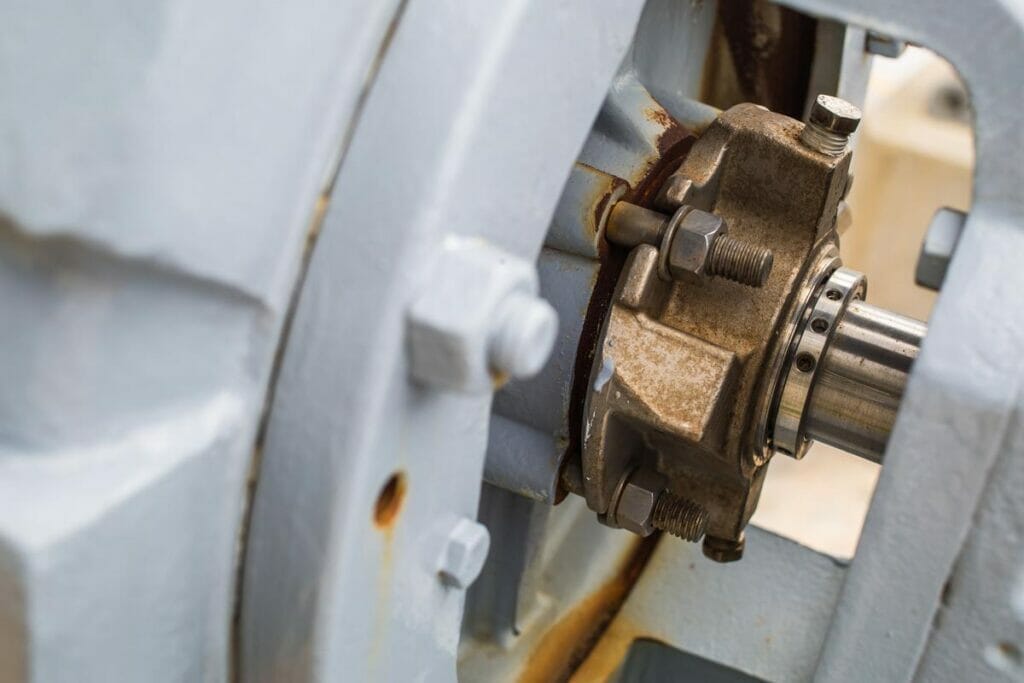
Adverse Operating Conditions Exceeding Design Limits
Higher Temperature and Pressure Challenges
Mechanical seals are designed to operate within specific temperature and pressure ranges. When these limits are exceeded, the seal faces and other components can experience accelerated wear and damage. Higher temperatures can cause thermal expansion, material degradation, and changes in fluid properties, while elevated pressures can lead to increased stress on the seal faces and deformation of the seal components.
To mitigate the impact of higher temperature and pressure, it is essential to select seal materials and designs that are compatible with the expected operating conditions. This may involve using high-performance materials, such as silicon carbide or tungsten carbide, for the seal faces and elastomers with higher temperature ratings for the secondary seals.
Excessive Shaft Speed
Excessive shaft speed can cause increased heat generation due to friction, leading to thermal distortion of the seal faces and potential leakage. High shaft speeds can also result in vibration and shaft misalignment, further compromising the seal’s integrity.
To address excessive shaft speed issues, it is crucial to ensure that the selected mechanical seal is rated for the intended operating speed range. Additionally, proper shaft alignment and balancing should be maintained to minimize vibration and ensure stable operation.
Seal Pot and Barrier Fluid Considerations
Issues with the seal pot or barrier fluid, such as contamination, incorrect pressure, or inadequate circulation, can lead to seal leakage and premature failure.
To prevent these problems, regular monitoring and maintenance of the seal pot and barrier fluid system are essential. This includes ensuring proper fluid levels, maintaining the correct pressure, and regularly replacing the barrier fluid to prevent contamination. The use of filtration systems and heat exchangers can also help maintain the barrier fluid’s quality and temperature.
Lubrication and Dry Running Concerns
Insufficient lubrication can cause increased friction, heat generation, and wear of the seal faces, ultimately leading to leakage. Dry running, which occurs when the seal faces operate without proper lubrication, can cause rapid damage and failure.
To prevent lubrication-related issues, it is essential to ensure that the mechanical seal is properly lubricated during installation and operation. This may involve using a lubricating fluid compatible with the process fluid and the seal materials. In applications prone to dry running, consider using seal designs with features such as bidirectional grooves or micro-channels on the seal faces to enhance lubrication and minimize the risk of damage.
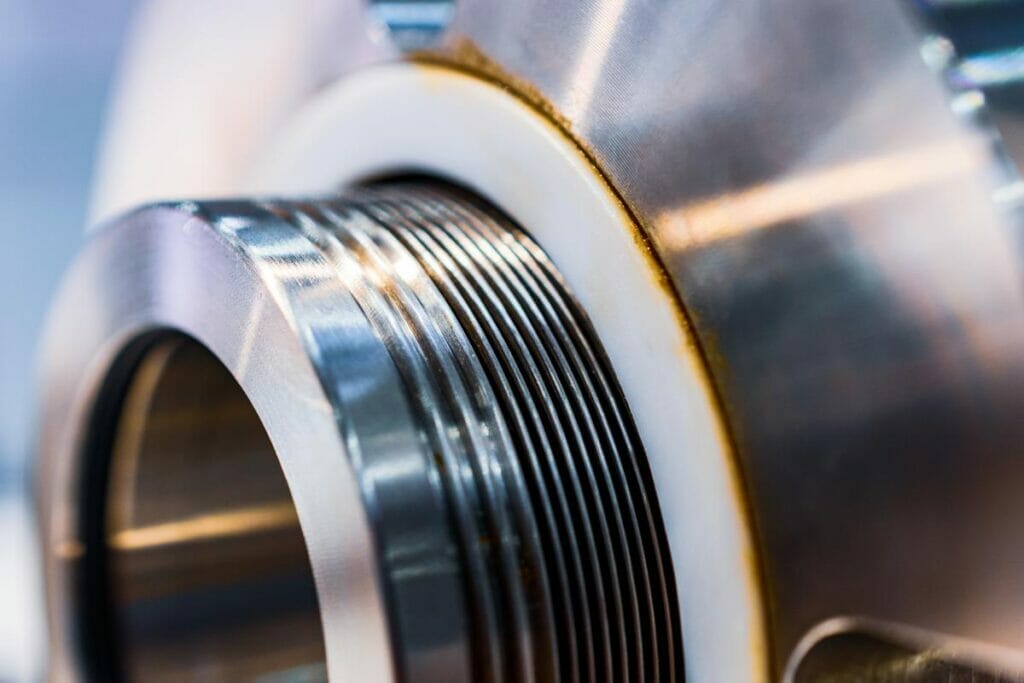
Mechanical Seals Issues
Incorrect Material Selection
Selecting the wrong materials for mechanical seals can lead to premature failure and leakage. The seal faces, O-rings, and other components must be compatible with the process fluid and operating conditions. For example, using a carbon graphite seal face in a highly abrasive slurry can result in rapid wear and leakage.
Improper Seal Selection
Choosing the wrong type of mechanical seal for a specific application can also cause leakage issues. Factors such as temperature, pressure, speed, and chemical compatibility must be considered when selecting a seal. For instance, using a single seal in a high-pressure application that requires a double seal can result in leakage and potentially hazardous conditions.
Improper Installation
Incorrect installation is a common cause of mechanical seal leakage. Improper alignment, insufficient lubrication, and over-tightening can all lead to seal failure. It is essential to follow the manufacturer’s installation instructions carefully and use the correct tools and techniques. Proper training for maintenance personnel is also crucial to ensure that seals are installed correctly and consistently.
Seal Aging
Over time, mechanical seals can degrade due to exposure to process fluids, temperature fluctuations, and other factors. As seals age, they may develop cracks, lose elasticity, or experience changes in material properties that can lead to leakage. Regular inspection and maintenance can help identify signs of seal aging before leakage occurs. Establishing a preventive maintenance schedule that includes seal replacement at recommended intervals can minimize the risk of failure due to aging.
In conclusion
Troubleshooting mechanical seal leakage requires a systematic approach. Identify the cause, implement the appropriate solution, and regularly maintain the seal to prevent future issues. For expert guidance on mechanical seal maintenance and repairs, contact a trusted seal manufacturer or distributor today.