Have you ever wondered what a labyrinth seal is and how it works?
In this blog post, we’ll break down the basics of labyrinth seals in a clear and professional manner.
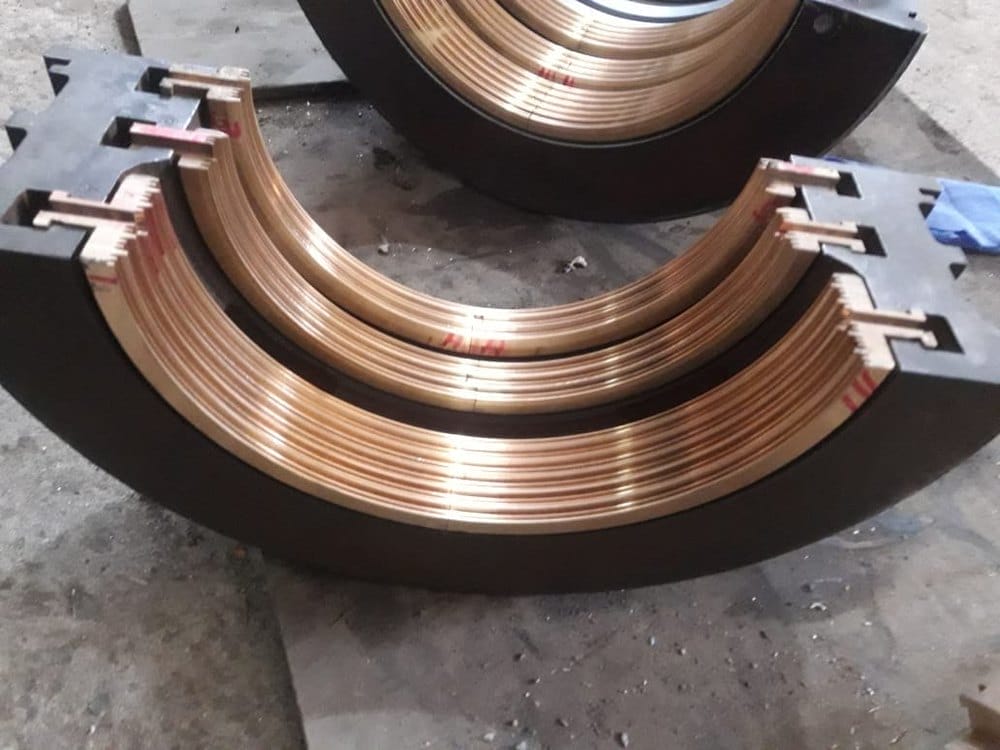
What is a Labyrinth Seal
A labyrinth seal is a type of mechanical seal. It is used to prevent leakage of fluids or gases between rotating and stationary parts. The seal consists of a series of intricate, maze-like grooves or channels.
Working Principle of Labyrinth Seal
The working principle of a labyrinth seal is based on creating a tortuous path for the fluid or gas. As the fluid enters the seal, it encounters the labyrinth-like passages. The fluid loses its kinetic energy as it navigates through the twists and turns. This reduces the pressure and velocity of the fluid, making it difficult for it to escape.
Components of Labyrinth Seal
Stator
The stator is the stationary part of the labyrinth seal. It is typically made of a durable material such as steel or bronze. The stator contains a series of grooves or teeth that form the labyrinth path.
Rotor
The rotor is the rotating component of the labyrinth seal. It is attached to the shaft and rotates with it. The rotor also features a series of grooves or teeth that interlock with those on the stator.
Labyrinth Path
The labyrinth path is created by the interlocking grooves or teeth on the stator and rotor. This maze-like path makes it difficult for fluids or gases to pass through the seal. The complex geometry of the labyrinth path creates a series of pressure drops, which helps to prevent leakage.
Clearance
The clearance is the small gap between the stator and rotor components. This gap allows for the relative motion between the two parts while maintaining a close tolerance. The size of the clearance is critical to the effectiveness of the labyrinth seal.
Sealing Fluid
In some cases, a sealing fluid may be used in conjunction with the labyrinth seal. This fluid, often an oil or grease, helps to further prevent leakage by filling the gaps in the labyrinth path. The sealing fluid also helps to lubricate the moving parts and reduce wear.
Design Considerations of Labyrinth Seal
When designing a labyrinth seal, several factors need to be considered:
- Material selection: The seal materials should withstand the operating conditions.
- Clearance: The clearance should be optimized to minimize leakage while allowing for thermal expansion.
- Number of stages: Increasing the number of labyrinth stages improves sealing effectiveness but increases complexity.
- Groove geometry: The shape and dimensions of the grooves impact the sealing performance.

Types of Labyrinth Seal
Straight-Through Labyrinth Seal
A straight-through labyrinth seal has a simple design. It consists of a series of straight passages. These passages are arranged in a maze-like pattern. The fluid must navigate through the passages to reach the other side. This type of seal is effective for low-pressure applications.
Staggered Labyrinth Seal
A staggered labyrinth seal has a more complex design. It features a series of offset or staggered passages. The fluid must follow a zigzag path through the seal. This design creates more turbulence and resistance to fluid flow. Staggered labyrinth seals are suitable for higher-pressure applications.
Stepped Labyrinth Seal
A stepped labyrinth seal incorporates steps or changes in height within the seal passages. The fluid must navigate through these steps as it passes through the seal. The stepped design helps to dissipate energy and reduce fluid velocity. Stepped labyrinth seals are effective for high-pressure and high-velocity applications.
Honeycomb Labyrinth Seal
A honeycomb labyrinth seal features a honeycomb-like structure. The seal passages are formed by a series of hexagonal cells. This design creates a large surface area and tortuous path for the fluid. Honeycomb labyrinth seals are used in applications requiring high sealing effectiveness and durability.
Interlocking Labyrinth Seal
An interlocking labyrinth seal consists of two or more components that interlock with each other. The interlocking design creates a complex maze of passages for the fluid to navigate. This type of seal provides enhanced sealing performance and is suitable for high-pressure and high-speed applications.
Materials of Labyrinth Seal
Labyrinth seals are typically made from materials that can withstand high temperatures, pressures, and rotational speeds. These materials must also resist wear and corrosion to maintain optimal performance over time.
Common Materials Used
- Metals: Stainless steel and aluminum are frequently used due to their strength and durability. These metals can handle the mechanical stresses and temperatures associated with high-speed rotating bearings and gas turbine engines.
- Ceramics: Ceramic materials are used for their excellent heat resistance and low friction properties. They are particularly useful in applications where high temperatures are prevalent, such as in gas turbines.
- Plastics and Polymers: Advanced plastics like PTFE (Teflon) and PEEK are sometimes used. These materials offer good chemical resistance and low friction, making them suitable for specific industrial applications.
- Composite Materials: Composites that combine metals with other materials can offer a balance of strength, heat resistance, and weight. These are often used in specialized applications where traditional seals might fail.
Special Coatings
- Abradable Coatings: These coatings are applied to the labyrinth fins or threads to allow for a controlled wear process. They help maintain a tight seal even as components wear down over time.
- Rub-Tolerant Coatings: These coatings are designed to withstand direct contact without significant degradation. They are useful in maintaining the effectiveness of the seal under varying operating conditions.
Considerations for Material Selection
- Chemical Properties: The material must be resistant to the process fluids it will encounter. For example, in chemical processing plants, the seal material must resist corrosion from aggressive chemicals.
- Thermal Properties: The material must handle the heat generated by high-speed rotation and friction. Poorer heat dissipation can lead to failure, so materials with good thermal conductivity are preferred.
- Mechanical Properties: The material must withstand mechanical stresses without deforming. High-strength metals and ceramics are often chosen for their ability to handle these conditions.
Advantages of Labyrinth Seals
Labyrinth seals offer several advantages over traditional seals, making them an effective choice for various applications.
Lack of Friction
Labyrinth seals operate without direct physical contact between the rotating shaft and the seal itself. This lack of friction reduces wear and tear, extending the lifespan of the seal and associated machinery.
Effective Sealing
Labyrinth seals provide effective sealing by creating a tortuous path for the fluid flow. This complicated labyrinth reduces leakage flow, ensuring optimal performance of the machinery. The characteristic path and labyrinth chamber create fluid vortices that impede the flow of process fluids.
Reduced Maintenance
Due to the lack of direct contact and minimal wear, labyrinth seals require less maintenance compared to traditional seals. This results in lower operational costs and less downtime for industrial machinery.
High-Temperature Resistance
Labyrinth seals can withstand high temperatures, making them suitable for applications involving extreme heat. This includes gas turbines and steam turbines, where the seals are exposed to high ambient pressure and atmospheric pressure.
Versatility
Labyrinth seals are versatile and can be designed to suit various applications. They can be used in gas turbine engines, boiler feed pumps, and other machinery that requires effective sealing. The design of labyrinth seals can be customized to meet specific requirements, including axial clearance flow and circumferential flow.
Cost-Effective
Investing in labyrinth seals can be a clever investment due to their long lifespan and reduced maintenance requirements. This makes them a cost-effective solution for sealing applications in industrial machinery.
Disadvantages of Labyrinth Seals
Inability to Provide a Completely Fluid-Tight Seal
Labyrinth seals allow for some fluid or gas leakage, especially under high-pressure gradients. This is problematic in applications like gas turbine engines or steam turbines that require absolute sealing.
Complexity of Design
The intricate configuration and precise alignment of labyrinth seals make the manufacturing process challenging and expensive. High-quality materials and precise engineering are necessary, increasing overall costs.
Limitations at High Rotational Speeds
At very high speeds, centrifugal motion and fluid vortices can increase leakage flow, which is a concern in high-performance gas turbines and centrifugal pumps.
Lack of Friction
While the non-contact nature of labyrinth seals prevents wear and tear, it can make them less effective in high-pressure or high-speed applications compared to traditional contact seals like oil seals.
Less Effective in Environments with Significant Pressure Fluctuations
Pressure fluctuations can disrupt pressure equalization across the seal, leading to increased leakage. This is problematic in applications with varying air- and gas pressures, such as gas path sealing.
Material Limitations
Labyrinth seals can struggle with heat dissipation, affecting their longevity and performance in high-temperature applications like boiler feed pumps.
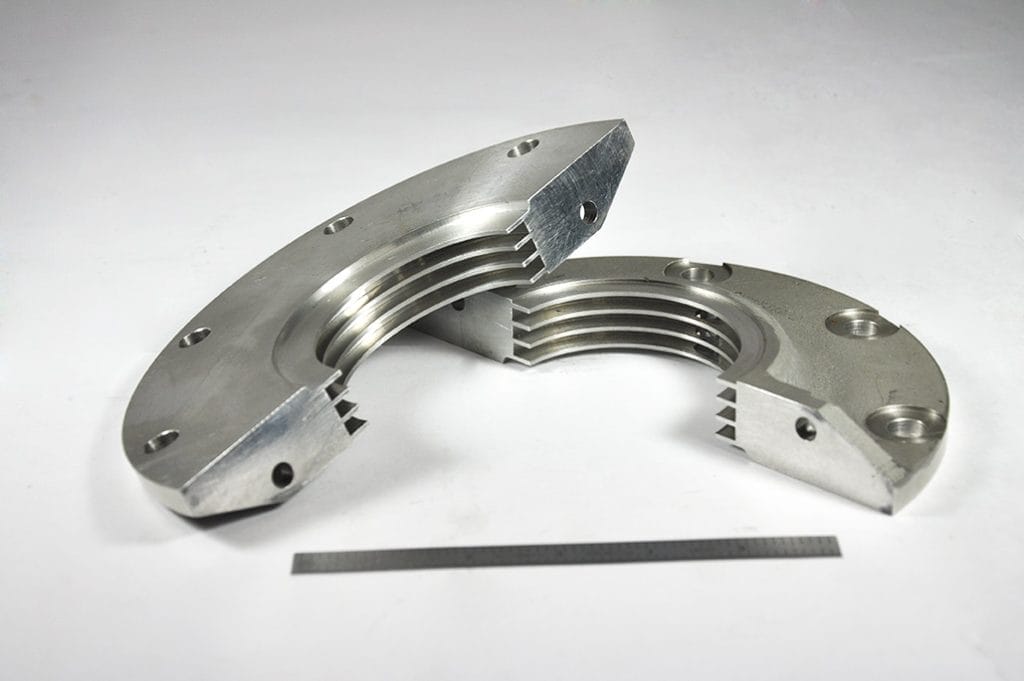
Applications of Labyrinth Seals
Gas Turbine Engines
Labyrinth seals are commonly used in gas turbine engines to prevent fluid leakage, ensuring optimal performance.
Steam Turbines
In steam turbines, labyrinth seals maintain efficiency by managing pressure gradients and reducing leakage between high- and low-pressure sections, essential for smooth turbine operation.
Centrifugal Pumps
Labyrinth seals in centrifugal pumps prevent process fluid leakage by creating a tortuous path for the fluid, reducing the likelihood of leakage.
High-Speed Rotating Bearings
Labyrinth seals are effective in high-speed rotating bearings due to their non-contact design, reducing wear and extending machinery lifespan.
Bearing Chambers
Labyrinth seals in bearing chambers manage flow direction and reduce axial clearance flow, ensuring smooth operation without leakage.
Liquid-Free Sealing Applications
Labyrinth seals are used where a liquid-free seal is needed, preventing fluid leakage without physical contact, suitable for applications without lubrication.
Boiler Feed Pumps
In boiler feed pumps, labyrinth seals prevent process fluid leakage, ensuring efficient pump operation.
FAQs
How do labyrinth seals compare to other types of seals
Labyrinth seals offer better high-speed performance and durability compared to contact seals, but they may have higher leakage rates compared to other non-contacting seals like dry gas seals.
Can labyrinth seals be used in both gas and liquid applications
Yes, labyrinth seals can be used in both gas and liquid applications, but they are more commonly used in gas applications due to their higher efficiency in those conditions.
In Conclusion
In summary, a labyrinth seal is a mechanical seal that uses a series of interlocking channels to prevent fluid leakage. For more insights into industrial sealing solutions, contact us today to learn how labyrinth seals can enhance your machinery’s efficiency.