Have you ever wondered how mixed flow pumps work? These unique pumps combine the best features of radial and axial flow designs. In this blog post, we’ll explore the working principle behind mixed flow pumps. By the end, you’ll understand how these pumps efficiently move fluids and why they’re the ideal choice for many applications.
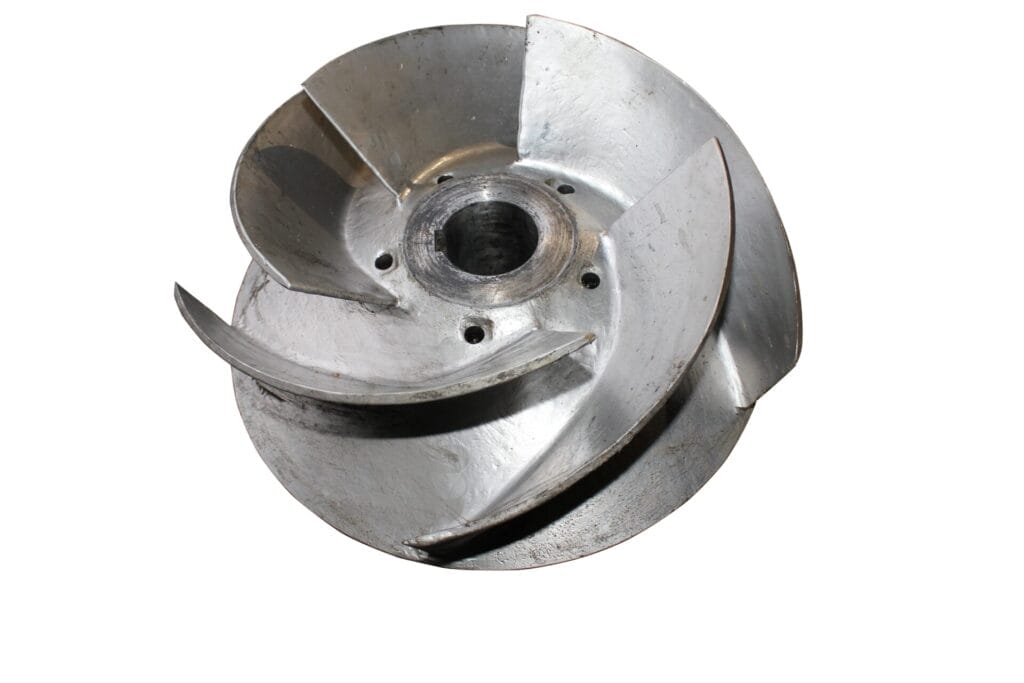
What Is Mixed Flow Pump and Working Principle
A mixed flow pump is a type of centrifugal pump that combines the features of both radial flow and axial flow pumps. In a mixed flow pump, the liquid enters the impeller axially through the eye of the impeller. As the impeller rotates, the liquid is accelerated and flows through the impeller passages, where it is subjected to both centrifugal and axial forces. The liquid then exits the impeller at an angle, typically between 20° and 60° from the pump axis, and enters the casing.
Components of Mixed Flow Pumps
- Impeller: Combines both radial and axial flow characteristics to efficiently transfer energy from the motor to the fluid.
- Pump Casing: Houses the impeller and guides the fluid through the pump, minimizing hydraulic losses and ensuring smooth flow transitions.
- Shaft and Bearings: Support the impeller and maintain its alignment, designed to withstand operational forces.
- Seals: Prevent fluid leakage and maintain pump efficiency, including mechanical seals or packing.
- Drive System: Typically an electric motor that provides the necessary power to rotate the impeller and drive the pumping process.
Advantages of Mixed Flow Pumps
- High Flow Rates at Moderate Pressure Heads: Suitable for systems requiring a balance between flow and pressure.
- Good Efficiency: Especially when operating close to their best efficiency point (BEP).
- Simple Design: Contributes to reliability and ease of maintenance.
- Handles Various Liquids: Can handle low viscosity liquids and small amounts of suspended solids.
- Small Footprint: Advantageous in space-constrained installations.
Disadvantages of Mixed Flow Pumps
- Limited Operating Range: Designed for specific flow rates and pressure heads, efficiency drops outside this range, increasing wear on components.
- Susceptible to Cavitation: More prone to cavitation, especially at low flow rates or high suction lifts, which can damage the impeller and degrade performance.
- Not Suitable for High Viscosity or Suspended Solids: Handling high viscosity fluids or large amounts of suspended solids can cause clogging and reduce efficiency.
Applications of Mixed Flow Pumps
- Water Supply Systems: Used in water supply systems for efficient water distribution.
- Irrigation Projects: Employed in irrigation projects to ensure adequate water flow.
- Sewage Treatment Plants: Utilized in sewage treatment plants for effective wastewater management.
- Firefighting Applications: Crucial in firefighting for delivering high flow rates at moderate heads.
- Pumping Low Viscosity Liquids: Suitable for pumping low viscosity liquids and handling small amounts of suspended solids.
- Chemical Industry: Used for transferring acids, alkalis, and other process fluids.
- Oil and Gas Sector: Beneficial in crude oil transfer and offshore water injection applications.
What Is the Difference between Axial and Mixed Flow Pumps
The primary difference between axial and mixed flow pumps lies in the direction of fluid flow.
In axial flow pumps, fluid moves parallel to the impeller’s rotational axis, resulting in a straight flow path.
Mixed flow pumps combine both axial and radial flow characteristics. The fluid enters axially but is discharged in a radial direction, creating a diagonal flow path. This unique design allows mixed flow pumps to generate higher pressures than axial flow pumps while maintaining a relatively high flow rate.
What Is the Difference between Radial Flow and Mixed Flow Pumps
Radial flow and mixed flow pumps differ in their flow path and pressure generation capabilities.
Radial flow pumps, also known as centrifugal pumps, direct fluid perpendicularly to the impeller’s rotational axis. This design enables them to generate high pressures but limits their flow rate capacity.
Mixed flow pumps incorporate both radial and axial flow characteristics. They provide a balance between pressure and flow rate, making them suitable for applications requiring moderate to high pressures and flow rates. Mixed flow pumps bridge the gap between the high-pressure capabilities of radial flow pumps and the high-flow characteristics of axial flow pumps.
In conclusion
understanding the working principle of mixed flow pumps is crucial for selecting the right pump for specific applications. Mixed flow pumps offer a balance between radial and axial flow, providing efficient performance and versatility. To learn more about mixed flow pumps, consult with a trusted pump manufacturer or supplier.