Have you ever wondered what edge welded metal bellows are and how they function?
In this blog post, we’ll dive into the world of these essential components, exploring their unique construction and the critical roles they play in various industries. By the end, you’ll gain a clear understanding of edge welded metal bellows and their importance in modern applications.

What is of Edge-Welded Metal Bellows
Edge-welded metal bellows are flexible, pressure-tight components made by welding thin metal diaphragms at their inner and outer edges. The diaphragms, typically made from stainless steel, Inconel, Hastelloy or titanium, are stacked and welded to create a strong yet flexible bellows assembly.
The edge-welding process joins the individual diaphragms into a continuous, leak-tight unit that can compress, extend, and flex under pressure. This welded construction allows the bellows to contain media and withstand pressure, vacuum, and axial and angular movement.
Advantages of Edge-Welded Metal Bellows
- High Strength and Durability: Welded construction provides excellent strength, withstanding high pressures and extreme temperatures, and enduring repeated cycles without failure.
- Leak-tight Sealing: Continuous welds prevent media from escaping, critical for hazardous materials, high-purity processes, or vacuum environments.
- Flexibility and Motion Capability: Edge-welded bellows can compress, extend, and flex angularly, accommodating misalignment and movement, ideal for moving parts or thermal expansion.
- Compact Design: Thin-wall construction allows for compression to a short length, saving space in applications with tight constraints.
- Customization: Bellows can be designed to specific size, shape, material, and performance requirements, ensuring optimal system integration.
Manufacturing Process of Edge-Welded Metal Bellows:step by step
Step 1: Strip Preparation
Once the material is selected, it is cut into strips of the desired width and thickness. The strips are then cleaned and deburred to ensure a smooth surface for welding. Any imperfections on the strip surface can lead to weak points in the final product.
Step 2: Forming the Diaphragms
The prepared strips are fed into a forming machine that shapes them into individual diaphragms. The forming process involves pressing the strips between two dies to create the desired shape, which is typically a shallow cup or convolution. The number of diaphragms formed depends on the desired length of the bellows.
Step 3: Edge Welding
After the diaphragms are formed, they are stacked together and aligned in a welding fixture. The edges of the diaphragms are then welded together using a precision welding process, such as laser welding, electron beam welding, or TIG welding. The welding process creates a strong, leak-tight seal between each diaphragm.
Step 4: Trimming and Sizing
Once the diaphragms are welded together, the resulting bellows assembly is trimmed to the desired length. This process involves cutting off any excess material at the ends of the bellows. The trimmed bellows are then sized to ensure that they meet the required dimensions and tolerances.
Step 5: Heat Treatment
Depending on the material and the desired properties, the edge-welded metal bellows may undergo heat treatment. This process can help to relieve residual stresses from the forming and welding processes, as well as improve the strength and flexibility of the bellows. Common heat treatment methods include annealing, solution treatment, and aging.
Step 7: Testing and Inspection
Before the edge-welded metal bellows are considered complete, they must undergo rigorous testing and inspection to ensure they meet the required quality standards. This may include leak testing, pressure testing, and cycle testing to verify the integrity and performance of the bellows. Visual inspections and dimensional checks are also performed to ensure that the bellows meet the specified requirements.
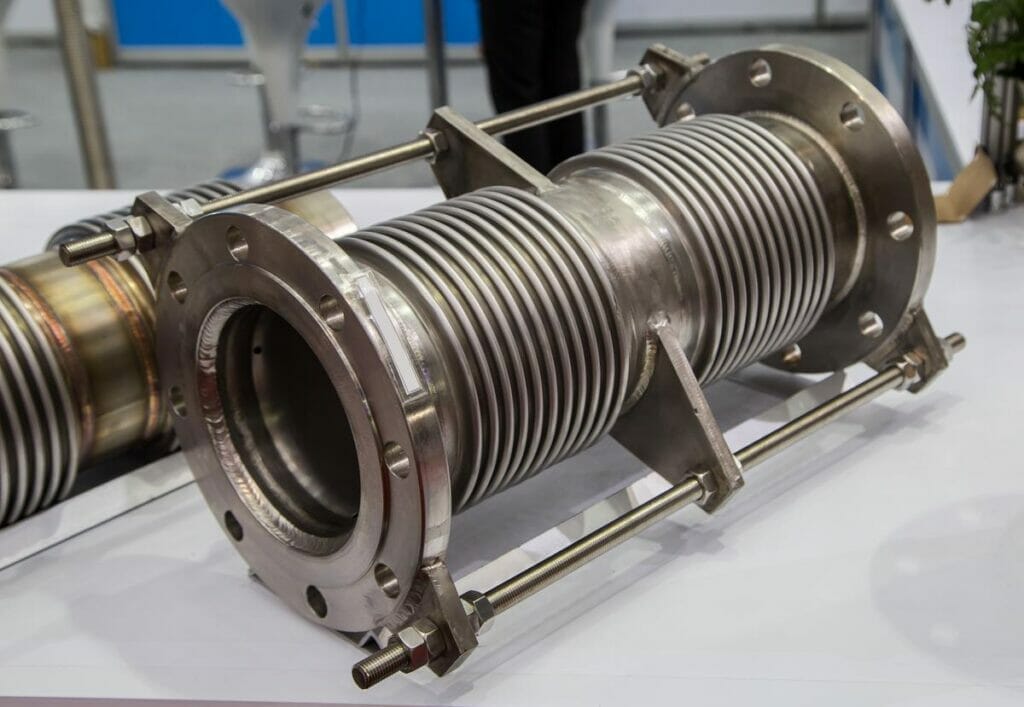
Design Considerations of Edge-Welded Metal Bellows
Diaphragm plate thickness
Thinner plates allow for greater flexibility and movement, but may be more prone to fatigue and failure under high stress or pressure. Thicker plates provide more durability and resistance to pressure, but can limit the bellows’ range of motion.
Diaphragm plate shape
The shape of the diaphragm plates also significantly impacts bellows performance. Common shapes include flat, rippled, and convoluted profiles. Flat plates offer simplicity but may have limited flexibility. Rippled and convoluted designs increase the effective surface area, allowing for greater extension and compression while maintaining strength. The choice of plate shape depends on the desired motion, load capacity, and space constraints of the application.
Vibration Dampeners
In certain applications, edge-welded metal bellows may be subjected to vibrations that can cause premature wear or failure. Incorporating vibration dampeners into the design can help mitigate these issues. Dampeners can include external devices such as springs or elastomeric supports, as well as internal features like multi-ply construction or non-uniform plate thickness. These elements absorb and dissipate vibrational energy, extending the bellows’ service life.
Material selection
The choice of material is crucial for ensuring the performance and longevity of edge-welded metal bellows. Factors to consider include corrosion resistance, temperature tolerance, strength-to-weight ratio, and compatibility with the media being contained or conveyed.
The geometry of the bellows
The overall geometry of edge-welded metal bellows determines their motion capabilities and load capacity. Key parameters include the number of convolutions, convolution pitch, and convolution height. More convolutions generally allow for greater extension and compression, but may reduce lateral stability. Larger convolution pitch and height can accommodate higher axial and angular displacements, respectively. Optimizing bellows geometry involves considering the required range of motion, available space, and anticipated loads.
Spring rates
The spring rate of edge-welded metal bellows refers to the force required to deflect the bellows by a unit distance. It is a function of the material properties, plate thickness, and bellows geometry. Higher spring rates indicate greater stiffness and load-bearing capacity, while lower rates allow for easier flexing and motion. Matching the spring rate to the application is important for ensuring proper functioning and preventing overloading or underperformance of the bellows.
Materials of Edge-Welded Metal Bellows
Edge-welded metal bellows are typically fabricated using thin-gauge metals that exhibit excellent flexibility, durability, and resistance to corrosion. Some of the most common materials used include:
- Stainless steel alloys (300 series, such as 304, 316, 321)
- Nickel-based alloys (Inconel, Hastelloy, Monel)
- Titanium and titanium alloys
- Aluminum alloys
- Copper and copper alloys (beryllium copper, phosphor bronze)
Comparison to Other Bellows Types
Comparison to Formed Bellows
Edge-welded metal bellows offer several advantages compared to formed bellows. The welded construction allows for thinner walls and a greater number of convolutions in a given length, resulting in lower spring rates and greater flexibility. Edge-welded bellows can also be made from a wider variety of materials, including exotic alloys, providing more options for demanding applications.
Comparison to Hydroformed Bellows
While hydroformed bellows are formed from a single piece of material, edge-welded bellows are constructed by welding individual diaphragms together at their inner and outer edges. This welded construction enables edge-welded bellows to have a larger diameter-to-length ratio and to operate at higher pressures compared to hydroformed bellows of similar size.
Comparison to Electroformed Bellows
Electroformed bellows are made through an additive process involving electrodeposition of metal onto a mandrel. In contrast, edge-welded bellows are fabricated by welding stamped or punched metal diaphragms together. Edge-welded bellows generally have a larger diameter and higher pressure capacity than electroformed bellows, but electroformed bellows can achieve very small diameters and extremely thin walls for applications requiring minimal spring rates.
Common Applications of Edge-Welded Metal Bellows
- Aerospace: Used in fuel and hydraulic systems as flexible connectors, compensators, and vibration isolators. Ideal for rocket engines, satellites, and aircraft.
- Semiconductor Manufacturing: Maintain ultra-clean environments in gas delivery systems, vacuum chambers, and wafer handling equipment.
- Medical Devices: Found in pumps, drug delivery systems, and surgical instruments. Offer precise motion control, sealing, and biocompatibility.
- Cryogenic Systems: Accommodate thermal changes in low temperatures. Common in liquid nitrogen, helium lines, and cryogenic storage.
- Vacuum Systems: Serve as seals and motion feedthroughs in high-vacuum environments. Used in particle accelerators, mass spectrometers, and electron microscopes.
- Automotive: Used in exhaust gas recirculation (EGR) and fuel injection systems. Improve engine efficiency and reduce emissions.
- Industrial Automation: Act as flexible couplings, shaft seals, and protective covers. Ensure sealing and motion control in automated machinery.
FAQs
How long do edge-welded metal bellows typically last?
In general, well-designed and properly maintained edge-welded metal bellows in typical industrial applications may last anywhere from 1-30 years or 100,000 to over 10 million cycles.
In conclusion
Edge-welded metal bellows are versatile components with numerous applications across various industries. Their unique design allows for flexibility, durability, and precision in critical systems.
To learn more about how edge-welded metal bellows can benefit your specific application, contact a reputable manufacturer for expert guidance and custom solutions.