What exactly is a mechanical seal, and how does it work? In this blog post, we’ll break down the basics of these critical components in simple terms. You’ll learn what mechanical seals are used for, the key parts they consist of, and how they prevent leaks. By the end, you’ll have a clear understanding of mechanical seal essentials.
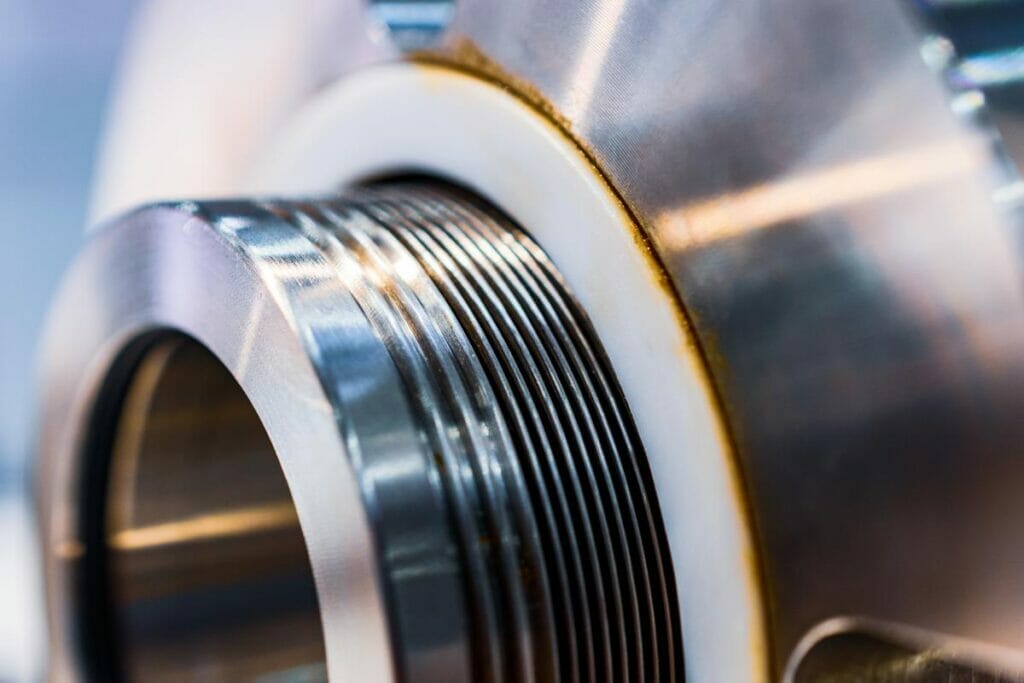
What is a Mechanical Seal
A mechanical seal is a device used to seal the rotating shaft of a pump, compressor, or other machinery to prevent leakage of fluids or gases. It consists of two main components: a stationary part called the seal ring and a rotating part called the seal face.
The seal ring is typically made of a hard, wear-resistant material such as silicon carbide or tungsten carbide, while the seal face is made of a softer material such as carbon or PTFE. The two components are held together by a spring or bellows, which maintains a constant pressure between them to create a tight seal.
How Does Mechanical Seal Work
The mechanical seal works by creating a fluid film between the stationary and rotating components. As the shaft rotates, the seal face moves with it, while the seal ring remains stationary. The spring or bellows applies pressure to the seal face, pushing it against the seal ring.
This creates a thin film of fluid between the two components, which acts as a barrier to prevent leakage. The fluid film is maintained by the pressure differential between the inside and outside of the seal, as well as by the centrifugal force generated by the rotating shaft.
Components of Mechanical Seal
- Seal ring: The stationary part of the seal, typically made of a hard, wear-resistant material.
- Seal face: The rotating part of the seal, made of a softer material that can conform to the seal ring.
- Spring or bellows: Provides the necessary pressure to maintain contact between the seal face and seal ring.
- Secondary seals: O-rings or gaskets that prevent leakage between the seal components and the pump housing.
- Gland plate: Holds the seal assembly in place and provides a mounting surface for the seal.
Sealing Points of Mechanical Seal
A mechanical seal has two main sealing points:
- Primary seal: The interface between the seal face and seal ring, where the fluid film is created to prevent leakage.
- Secondary seal: The point at which the seal components meet the pump housing, typically sealed by O-rings or gaskets.
Fluid Film of Mechanical Seal
The fluid film is a critical component of the mechanical seal, as it provides the barrier that prevents leakage. The film is typically very thin, on the order of a few microns, and is maintained by a combination of factors:
- Pressure differential: The higher pressure inside the pump forces fluid into the gap between the seal face and seal ring, creating the fluid film.
- Centrifugal force: As the shaft rotates, it generates a centrifugal force that helps to maintain the fluid film.
- Surface finish: The seal face and seal ring are carefully machined to have very smooth surfaces, which helps to maintain the fluid film.
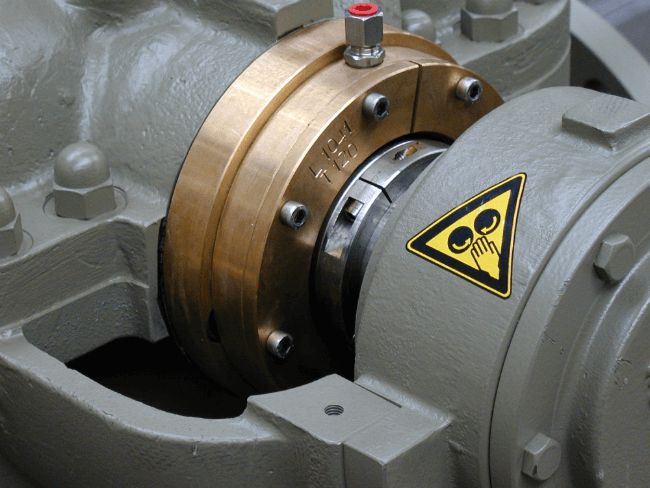
Advantages of Mechanical Seals
- Excellent Sealing Performance: Prevents leaks and effectively contains fluids.
- Durable: Withstands harsh operating conditions, including high temperatures and pressures.
- Minimal Maintenance: Reduces downtime and operating costs.
- Versatile: Suitable for a wide range of applications across industries.
Types of Mechanical Seals
- Single Mechanical Seals: The most common type, consisting of a single set of sealing faces.
- Double Mechanical Seals: Provide additional protection with two sets of sealing faces and a barrier fluid between them.
- Cartridge Mechanical Seals: Pre-assembled units that simplify installation and maintenance.
- Split Mechanical Seals: Allow for seal replacement without disassembling the equipment, reducing downtime.
Applications of Mechanical Seals
- Chemical Processing: Used in pumps to prevent leakage of transported chemicals.
- Oil and Gas: Applied in pumps to stop oil or gas leaks.
- Pharmaceuticals: Utilized in mixers and agitators to maintain product purity and prevent contamination.
- Food and Beverage: Employed in various equipment to avoid leaks and ensure product safety.
- Water Treatment: Implemented in pumps to prevent water leaks.
- Compressors: Contain gases under high pressure.
- Reactor Vessels and Valves: Ensure reliable sealing in rotating equipment.
FAQs
What factors should be considered when selecting a mechanical seal?
When selecting a mechanical seal, consider the fluid being sealed, operating temperature and pressure, shaft speed, environmental conditions, and the seal material’s compatibility with the fluid.
How long do mechanical seals typically last?
Generally, they can last anywhere from a few months to several years.
What are some alternatives to mechanical seals?
Some alternatives to mechanical seals include gland packing, lip seals, magnetic drive couplings, and seal-less pump designs, such as diaphragm or peristaltic pumps. However, these alternatives may not be suitable for all applications.
In summary
Mechanical seals are critical components for preventing leaks in rotating equipment. They provide a reliable seal between rotating shafts and stationary housing. To learn more about selecting and maintaining the right mechanical seals for your application, consult with a trusted seal supplier.