Have you ever wondered how a pump gets started when it’s dry? Pump priming is the answer.
In this blog post, we’ll explore what pump priming is, why it’s essential, and how it works. By understanding pump priming, you’ll be better equipped to maintain your pumps and ensure their optimal performance.
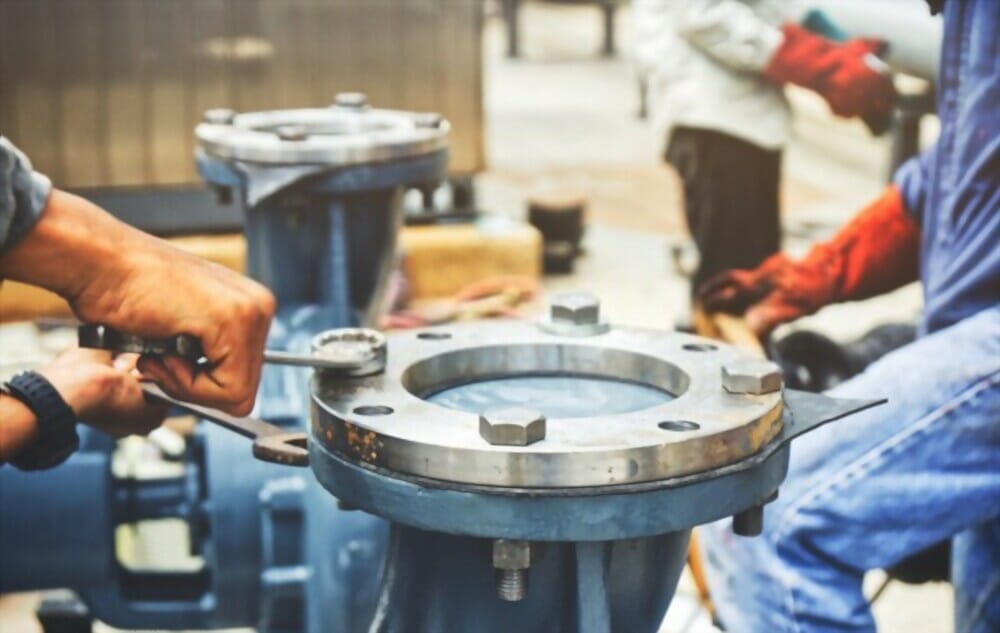
What Is Pump Priming in pump
Pump priming is a technique used to prepare a pump for operation by filling it with liquid before starting. This process ensures that the pump has enough liquid to create suction and maintain flow when it begins running.
In centrifugal pumps, the impeller requires liquid to generate the centrifugal force necessary for pumping. Without proper priming, the pump may not be able to create sufficient suction to draw liquid from the source, leading to reduced performance or failure to operate altogether.
Why Priming is Required
Priming is essential for several reasons:
- Establishing suction: Priming fills the pump and suction line with liquid, allowing the pump to create the necessary suction to draw more liquid from the source.
- Preventing damage: Running a pump dry without priming can cause severe damage to the pump’s internal components, such as seals, bearings, and impellers.
- Improving efficiency: A properly primed pump operates more efficiently, as it can maintain a steady flow of liquid without interruptions caused by air pockets or loss of suction.
- Ensuring reliable operation: Priming helps maintain consistent pump performance and reduces the risk of pump failure due to air entrainment or cavitation.
How to Prime a Pump
The priming process may vary slightly depending on the type of pump and its application, but the general steps are as follows:
- Close the discharge valve: Ensure that the discharge valve is closed to prevent liquid from flowing out of the pump during the priming process.
- Fill the pump with liquid: Pour liquid into the pump casing through the priming port or opening until it is full. Use a liquid that is compatible with the pump materials and the fluid being pumped.
- Fill the suction line: If the suction line is not already filled with liquid, pour liquid into it until it is full. This ensures that there are no air pockets in the line that could disrupt the suction.
- Close the priming port: Once the pump and suction line are filled with liquid, close the priming port or opening to prevent liquid from escaping.
- Start the pump: Turn on the pump and allow it to run for a short period. As the pump operates, it will draw more liquid from the source and establish a steady flow.
- Open the discharge valve: Gradually open the discharge valve to allow the pumped liquid to flow out of the pump and into the system.
When Priming is Not Required
- Submersible Pumps: Pumps already submerged in the liquid they pump. Designed to operate underwater, no manual priming needed.
- Flooded Suction: Pumps below the liquid source level, where liquid flows into the pump by gravity. Ensures constant liquid supply, no priming needed.
- Self-Priming Pumps: Pumps with built-in priming chambers or reservoirs. Prime themselves automatically when started. Used in applications with frequent start-stop cycles or where pumps are above the liquid source.
What Happens if a Pump is Not Primed
Failing to prime a pump before operation can lead to several issues that may cause damage to the pump and hinder its performance.
- Dry running: When a pump runs without any liquid, it experiences dry running. This can cause excessive heat generation due to friction between the pump’s internal components, leading to premature wear and tear, and potentially causing permanent damage to seals, bearings, and other vital parts.
- Cavitation: If a pump is not primed and attempts to draw liquid, it may create a low-pressure zone within the pump casing. This can cause the liquid to vaporize and form bubbles. When these bubbles collapse, they create shock waves that can damage the pump’s impeller, casing, and other components. Cavitation can also lead to increased noise, vibration, and a significant reduction in pump efficiency.
- Loss of prime: In some cases, an unprimed pump may initially be able to draw some liquid due to the residual liquid in the suction line. However, as the pump continues to operate, it may lose its prime, causing a sudden drop in performance and potentially leading to dry running or cavitation.
Methods of Priming a Pump
Priming a pump is essential for its proper operation. There are several methods to prime a pump, depending on the pump type and the application.
Manual Priming
One of the simplest methods of priming a pump is manual priming. This method involves filling the pump casing and suction line with liquid before starting the pump. The liquid can be poured into the pump through a priming port or by removing the top of the pump casing.
Manual priming is suitable for small pumps and applications where the liquid is readily available. However, it can be time-consuming and may not be practical for larger pumps or remote locations.
Priming with a Vacuum Pump
A vacuum pump is connected to the pump’s discharge line, creating a vacuum that draws the liquid into the pump casing and suction line.
Vacuum pump priming is efficient and can be used for larger pumps and applications where manual priming is not practical. However, it requires additional equipment and may not be suitable for all liquids.
Priming with a Jet Pump
A jet pump is installed on the pump’s suction line, creating a high-velocity jet of liquid that draws the liquid into the pump casing and suction line.
Jet pump priming is effective for larger pumps and can be used with a wide range of liquids. However, it requires a separate jet pump and may not be suitable for all applications.
Priming with a Separator
A separator is installed on the pump’s suction line, allowing the liquid to be drawn into the pump while preventing air from entering the system.
Separator priming is useful for applications where air entrainment is a concern, such as in wastewater treatment plants. However, it requires additional equipment and may not be suitable for all liquids.
Installing a Foot Valve
Installing a foot valve on the pump’s suction line is another method of priming a pump. A foot valve is a one-way valve that allows liquid to enter the suction line but prevents it from flowing back out.
Foot valves are simple and effective for maintaining prime in a pump. They are commonly used in applications where the pump is located above the liquid level, such as in well pumps. However, foot valves can become clogged with debris and may require periodic maintenance.
FAQs
What liquids can be used for pump priming?
The liquid used for pump priming should be compatible with the pumped fluid and the pump materials. Water is commonly used.
Can all pumps be primed?
Most pumps require priming, but some types, such as submersible pumps or self-priming pumps, do not need manual priming.
How long does pump priming take?
Pump priming typically takes a few minutes, depending on the size of the pump and the length of the suction line.
How often should a pump be primed?
A pump should be primed before initial startup, after maintenance, or whenever air enters the suction line.
Can a pump lose its prime?
Yes, a pump can lose its prime if air enters the suction line or if the pump is not operated for an extended period.
Conclusion
Pump priming is an essential process for removing air and ensuring proper pump operation. Regularly prime your pumps to avoid issues and maintain efficiency.
For more expert tips on pump maintenance, subscribe to our newsletter and never miss a beat with your pumping systems.