Ever wondered what sets a mechanical seal apart from a labyrinth seal? Both play crucial roles in preventing leaks, but they operate differently.
In this blog post, we’ll break down the key differences, advantages, and applications of each type. By the end, you’ll have a clear understanding of which seal is best suited for your needs.
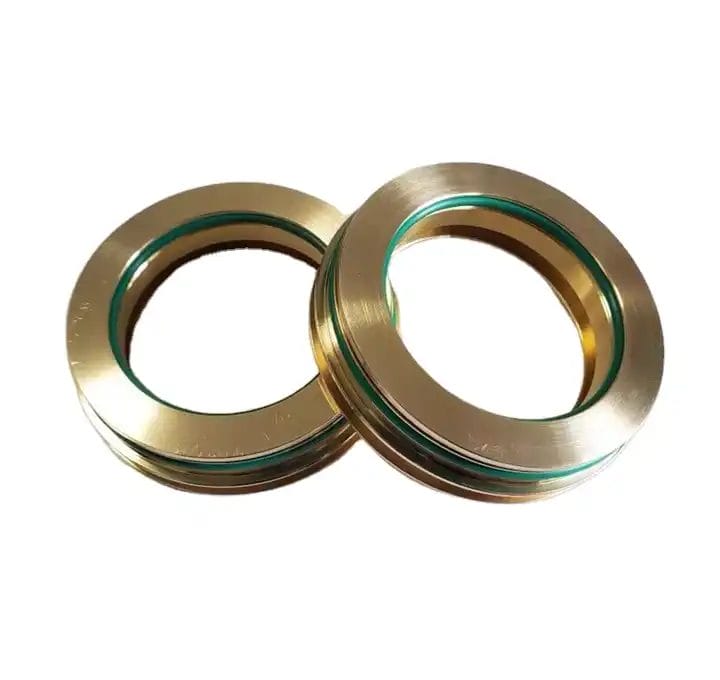
How Mechanical Seals Work
Mechanical seals work by establishing a tight seal between a stationary component and a rotating shaft. This sealing action is achieved through the use of two main parts: a stationary ring and a rotating ring.
The stationary ring is mounted on the equipment housing, while the rotating ring is attached to the rotating shaft. These rings are typically made from materials with excellent resistance to wear, such as carbon or ceramic. The surfaces of these rings are precision-lapped to ensure a smooth, flat interface.
Mechanical seals rely on a thin film of lubrication between the stationary and rotating rings. This film reduces friction and wear, ensuring smooth operation and extending the seal’s life. The film can be composed of the process fluid itself or an external lubricant.
How Labyrinth Seals Work
Labyrinth seals use a series of chambers and grooves to create a complex path for fluids. The design forces the fluid to navigate through multiple turns and narrow gaps. This labyrinthine path significantly reduces the fluid’s pressure and velocity, thereby minimizing leakage.
Unlike mechanical seals, labyrinth seals do not require direct contact between the rotating and stationary components. This non-contact design reduces wear and friction, making them ideal for high-speed applications. The absence of physical contact also means less heat generation, contributing to a longer seal life.
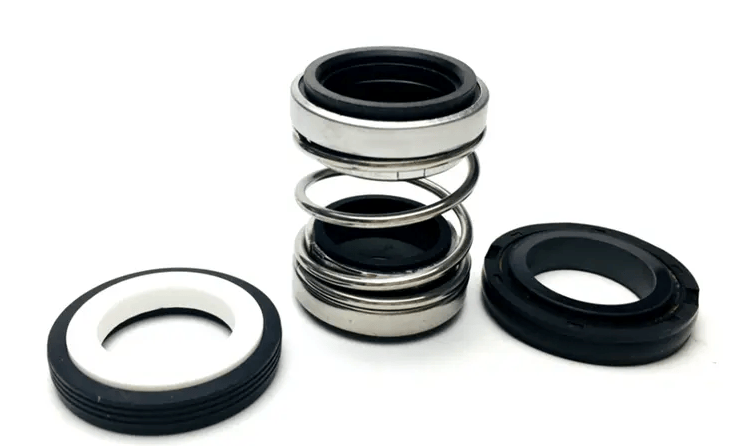
Comparing the Labyrinth Seals and Mechanical Seals
Sealing Mechanism
Mechanical seals use direct contact between the rotating shaft and the stationary component to create a tight seal. This contact prevents fluid leakage.
Labyrinth seals use a non-contact sealing action. They create a tortuous path for fluid flow, making it difficult for fluids to escape. This design relies on a complex path rather than physical contact.
Leakage and Sealing Efficiency
Mechanical seals are highly effective at preventing fluid leakage. Their direct contact design ensures minimal fluid escape, even under high pressure.
Labyrinth seals are less efficient in preventing leakage compared to mechanical seals. Their non-contact design means some fluid leakage is inevitable, especially under high pressure differentials.
Wear, Friction, and Heat Generation
Mechanical seals experience wear and friction due to their contact nature. This can lead to heat generation and eventual seal failure.
Labyrinth seals generate minimal friction and heat. Their non-contact design reduces wear, making them suitable for high-speed rotating equipment.
Contamination Resistance
Mechanical seals offer excellent resistance to contamination. Their tight seal prevents the ingress of contaminants.
Labyrinth seals are also effective at excluding contaminants. However, their non-contact nature means they are less effective in environments with granular contamination.
Speed Capability
Mechanical seals can handle moderate to high rotational speeds. However, their contact design may limit their use in extreme high-speed applications.
Labyrinth seals excel in high-speed applications. Their non-contact design allows for smooth operation at high rotational speeds.
Cost
Mechanical seals tend to be more expensive due to their complex design and materials. They also require more maintenance, adding to the overall cost.
Labyrinth seals are generally more cost-effective. Their simpler design and lower maintenance requirements make them a budget-friendly option.
Pressure Capabilities
Mechanical seals can handle a wide range of pressures, from low to high. Their contact design ensures a tight seal even under high pressure.
Labyrinth seals are better suited for moderate pressure conditions. Their non-contact design may struggle with extreme pressure differentials.
Seal Life
Mechanical seals have a shorter lifespan due to wear and tear from direct contact. Regular maintenance and replacement are often necessary.
Labyrinth seals offer a longer lifespan. Their lack of friction and wear makes them more durable, especially in high-speed and high-temperature environments.
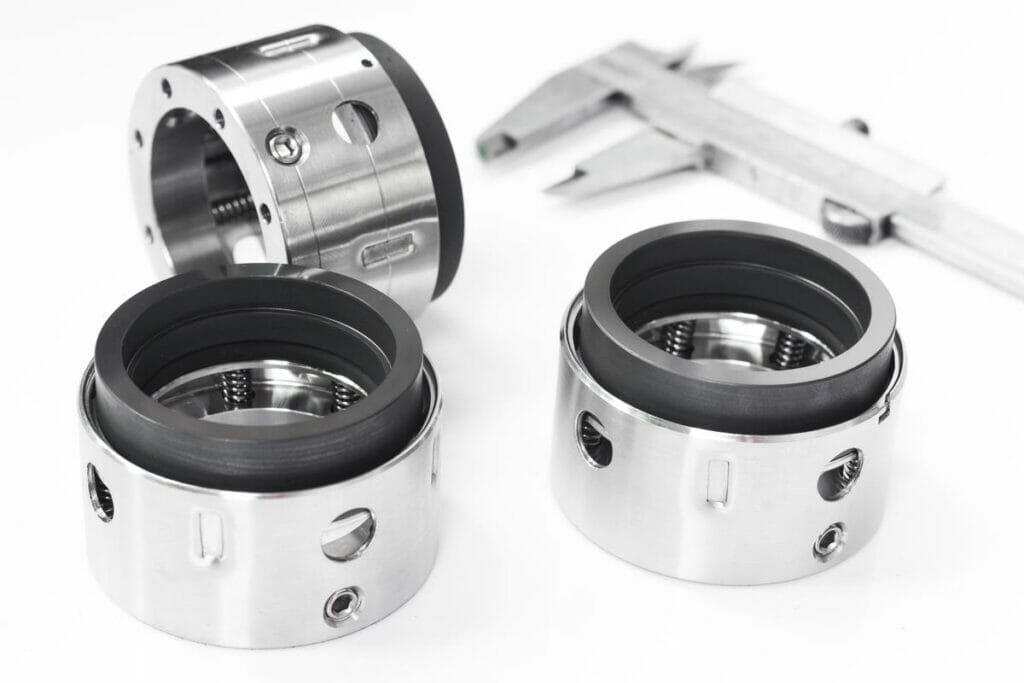
Factors to Consider When Selecting the Right Seal
Application Requirements
Consider the specific requirements of the application. This includes factors such as pressure, temperature, and speed. Mechanical seals are suitable for high-pressure and high-temperature applications. Labyrinth seals are better suited for lower-pressure and lower-temperature applications.
Fluid Characteristics
Evaluate the characteristics of the fluid being sealed. Mechanical seals can handle a wide range of fluids, including corrosive and abrasive media. Labyrinth seals are more suitable for clean, non-abrasive fluids.
Leakage Tolerance
Determine the acceptable level of leakage for the application. Mechanical seals provide a tighter seal and minimize leakage. Labyrinth seals allow for some leakage, which may be acceptable in certain applications.
Maintenance Requirements
Consider the maintenance requirements of each seal type. Mechanical seals require regular maintenance and may need replacement of wear parts. Labyrinth seals have fewer moving parts and generally require less maintenance.
Cost Considerations
Evaluate the cost implications of each seal type. Mechanical seals are typically more expensive than labyrinth seals. However, the long-term cost of maintenance and replacement should also be considered.
Space Constraints
Assess the available space for seal installation. Mechanical seals are more compact and require less space compared to labyrinth seals. Labyrinth seals may require more axial space for effective sealing.
Speed and Rotation
Consider the speed and rotation of the shaft. Mechanical seals can handle higher speeds and are suitable for both unidirectional and bidirectional rotation. Labyrinth seals are more suitable for lower speeds and unidirectional rotation.
Environmental Factors
Evaluate the environmental conditions in which the seal will operate. Mechanical seals can withstand harsh environments and are resistant to contamination. Labyrinth seals may be more susceptible to contamination and require a clean operating environment.
In Conclusion
In summary, while mechanical seals offer superior leakage prevention, labyrinth seals provide reliable performance with minimal maintenance.
For more insights into choosing the right seal for your application, explore our detailed guides. Contact us today for personalized recommendations.