Do mechanical seals need lubrication? Yes. This is a common question for those working with machinery and equipment.
In this blog post, we will explore the importance of lubrication for mechanical seals. By reading further, you’ll gain valuable insights into how proper lubrication can extend the life of your seals and improve overall machine performance.
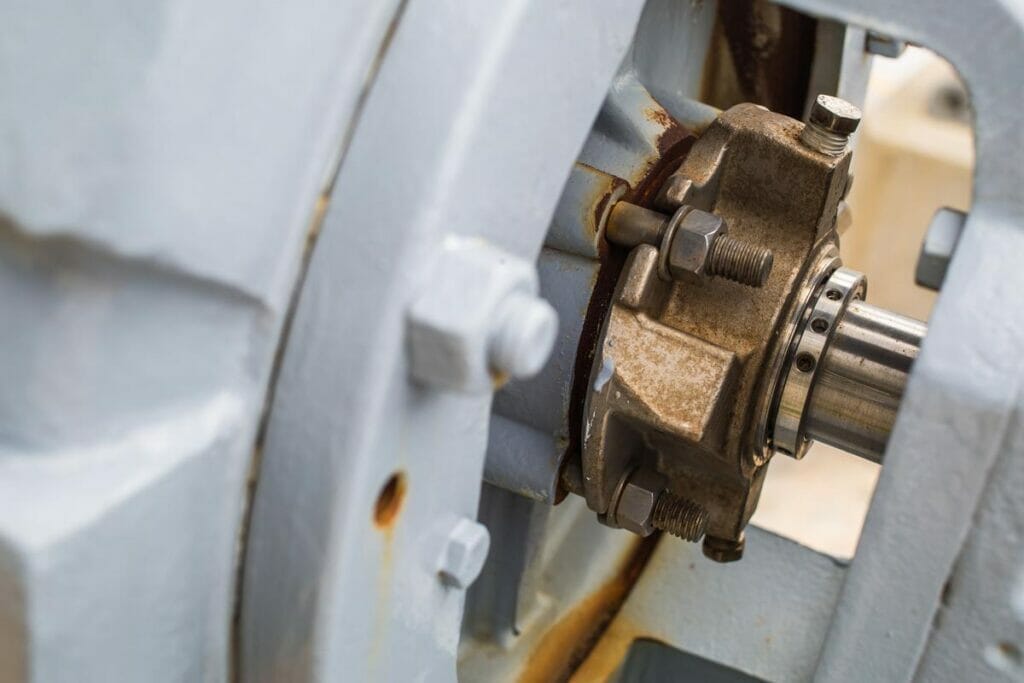
The Role of Lubrication in Mechanical Seals
Lubrication minimizes contact wear between mechanical seal components. It ensures a stable operation by creating a fluid film that separates the contact surfaces. This fluid film reduces the generation of excessive heat, which can lead to premature wear and seal failures. Inadequate lubrication can cause dry running conditions, leading to the failure of the seal.
How to Choose the Right Lubricant
Mechanical seals require proper lubrication to function effectively. The right lubricant helps reduce friction and wear. It also helps dissipate heat.
Consider the Operating Conditions
When selecting a lubricant, consider the operating conditions. These include temperature, pressure, and speed. The lubricant must maintain its properties under these conditions.
Compatibility with Seal Materials
The lubricant must be compatible with the seal materials. It should not degrade or damage the seal faces or elastomers. Consult the seal manufacturer’s recommendations.
Viscosity Requirements
The lubricant’s viscosity is important. It must be low enough to flow easily. But it must be high enough to maintain a lubricating film. The ideal viscosity depends on the operating conditions.
Additives and Properties
Lubricants may contain additives. These can enhance performance and protect against wear, corrosion, or oxidation. Consider the specific properties needed for your application.
Environmental and Safety Concerns
Consider environmental and safety factors. Some lubricants may be toxic or flammable. Others may not be suitable for food-grade applications. Choose a lubricant that meets regulations and safety requirements.
Testing and Monitoring
Regular testing and monitoring are important. This helps ensure the lubricant remains effective over time. Check for signs of degradation, contamination, or leaks. Replace the lubricant as needed.
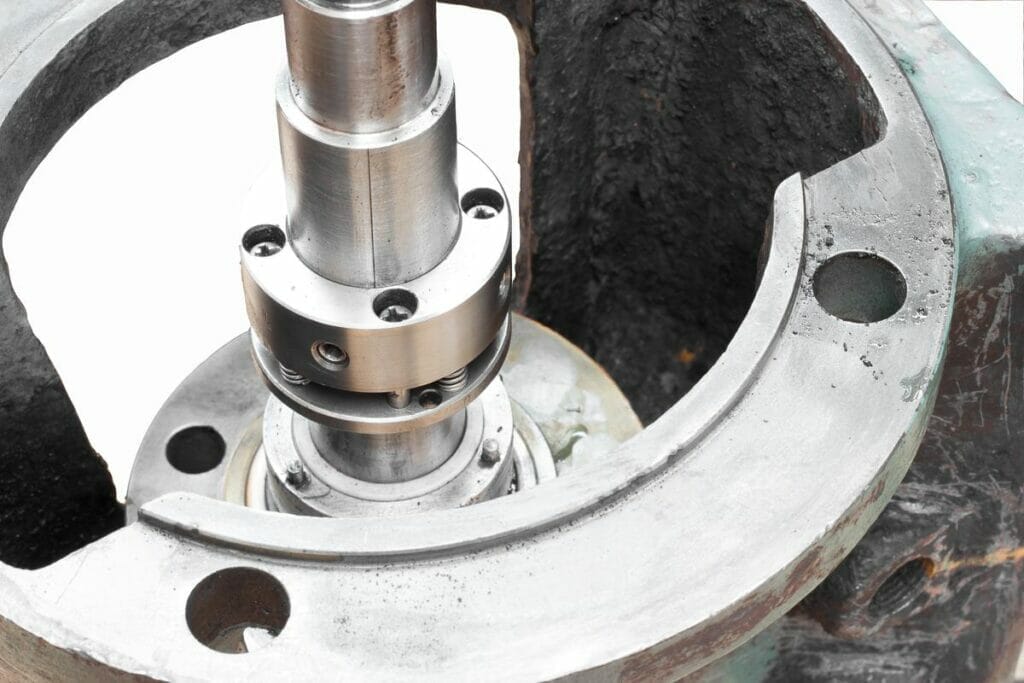
Consequences of Improper Lubrication
Increased Friction and Wear
Without adequate lubrication, the seal faces experience increased friction. This leads to excessive wear on the sealing surfaces. The seal life is significantly reduced as a result.
Heat Generation and Damage
Improper lubrication causes the mechanical seal to generate excess heat. The high temperatures can damage the seal faces and other components. This heat buildup may also cause the sealed fluid to vaporize. Vapor can disrupt the liquid film between the seal faces, further accelerating wear.
Leakage and Environmental Impact
A mechanical seal that lacks proper lubrication is prone to leakage. As the seal faces wear down, they lose their ability to maintain a tight seal. Leaks can lead to product loss and environmental contamination. In some cases, hazardous fluids may escape, posing safety risks.
Frequent Seal Failure and Replacement
Inadequate lubrication shortens the lifespan of mechanical seals. Seals experience accelerated wear and are more likely to fail prematurely. This results in increased downtime for seal replacement. The cost of frequent seal changes can be significant.
Decreased Equipment Reliability
Improper seal lubrication can impact the overall reliability of the equipment. Leaking seals may cause damage to bearings, shafts, and other components. This can lead to unplanned downtime and costly repairs.
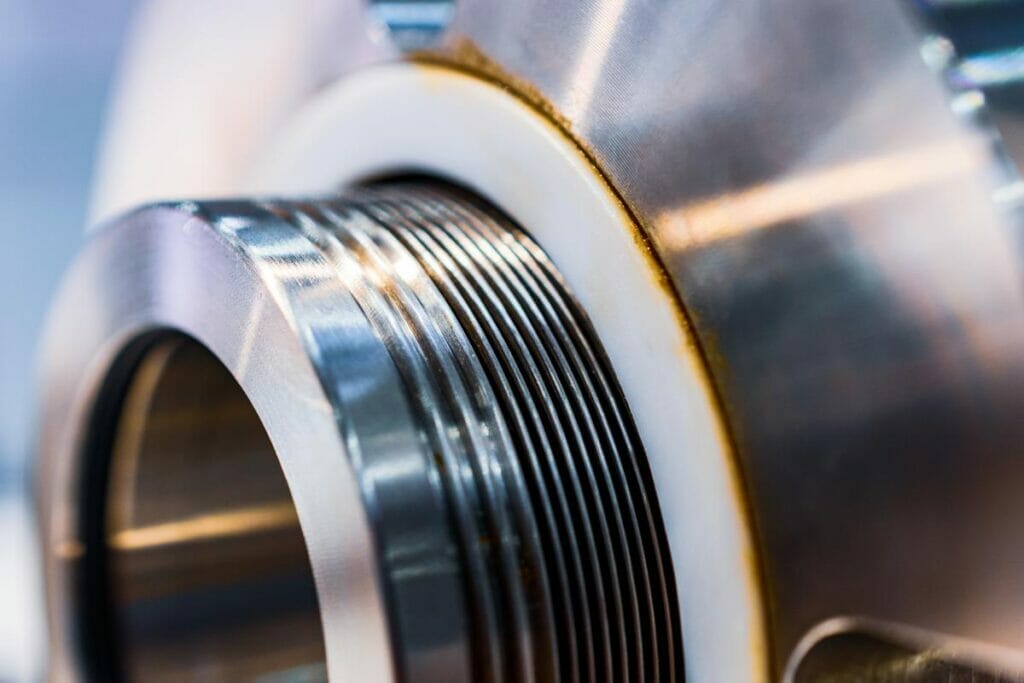
Best Practices for Lubricating Mechanical Seals
Selecting the Right Lubricant
Choose a lubricant that is compatible with the seal material and the process fluid. The lubricant should have the appropriate viscosity and temperature range. Consult the seal manufacturer’s recommendations for the best lubricant options.
Applying the Lubricant
Apply the lubricant sparingly to the seal faces. Excess lubricant can attract contaminants and cause buildup. Use a clean, lint-free cloth or applicator to apply the lubricant evenly.
Monitoring Lubricant Levels
Regularly check the lubricant levels in the seal chamber. Ensure that the lubricant is at the proper level as specified by the manufacturer. Low lubricant levels can lead to inadequate lubrication and seal failure.
Maintaining Lubricant Quality
Keep the lubricant clean and free from contamination. Replace the lubricant if it becomes contaminated or degrades over time. Follow the manufacturer’s guidelines for lubricant replacement intervals.
Proper Storage and Handling
Store lubricants in a cool, dry place away from direct sunlight. Keep containers sealed to prevent contamination. Use clean, designated equipment for handling lubricants to avoid cross-contamination.
FAQs
What types of lubricants are used for mechanical seals?
Common lubricants include oils, greases, and barrier fluids, depending on the application and seal type.
Should Seals Be Lubricated?
Most mechanical seals require lubrication. The lubricant helps reduce friction and wear. It also helps dissipate heat. Proper lubrication is essential for optimal seal performance and longevity. Consult the seal manufacturer’s guidelines for lubrication requirements.
Can Mechanical Seals Run Dry?
Some specialized mechanical seals can run dry for short periods. However, most standard mechanical seals require a lubricating fluid. Running a seal dry will generate excessive heat and friction. This can quickly damage the seal faces and cause failure.
What Is the Best Grease for Mechanical Seals?
The best grease depends on the specific seal and application. Factors include temperature, speed, and chemical compatibility. Silicone grease is a common choice. PTFE or graphite-loaded greases are used for more demanding applications. Always follow the seal manufacturer’s grease recommendations.
How often should mechanical seals be lubricated?
Lubrication frequency depends on factors such as the seal type, operating conditions, and manufacturer’s recommendations. Consult the seal’s documentation for guidance.
Are there mechanical seals that are self-lubricating?
Yes, some mechanical seals incorporate self-lubricating materials like PTFE or graphite, reducing the need for external lubrication.
Can a mechanical seal be over-lubricated?
Yes, over-lubrication can cause issues like increased temperature, reduced sealing effectiveness, and contamination of the process fluid.
Can a seal’s lubrication requirements change over time?
Yes, factors like wear, changes in operating conditions, or process fluid contamination can alter a seal’s lubrication needs. Regular monitoring and maintenance are essential.
In Conclusion
In summary, mechanical seals do require lubrication for optimal performance and longevity.
To learn more about choosing the right lubrication for your mechanical seals, explore our detailed guides. Contact us today for expert advice tailored to your specific needs.