Do you know the difference between static and dynamic seals? Static seals prevent leakage between two stationary surfaces, while dynamic seals stop leakage between moving and stationary parts. In this blog post, we’ll dive into the key distinctions, applications, and selection criteria for each type. By the end, you’ll have the knowledge to choose the right seal for your needs.
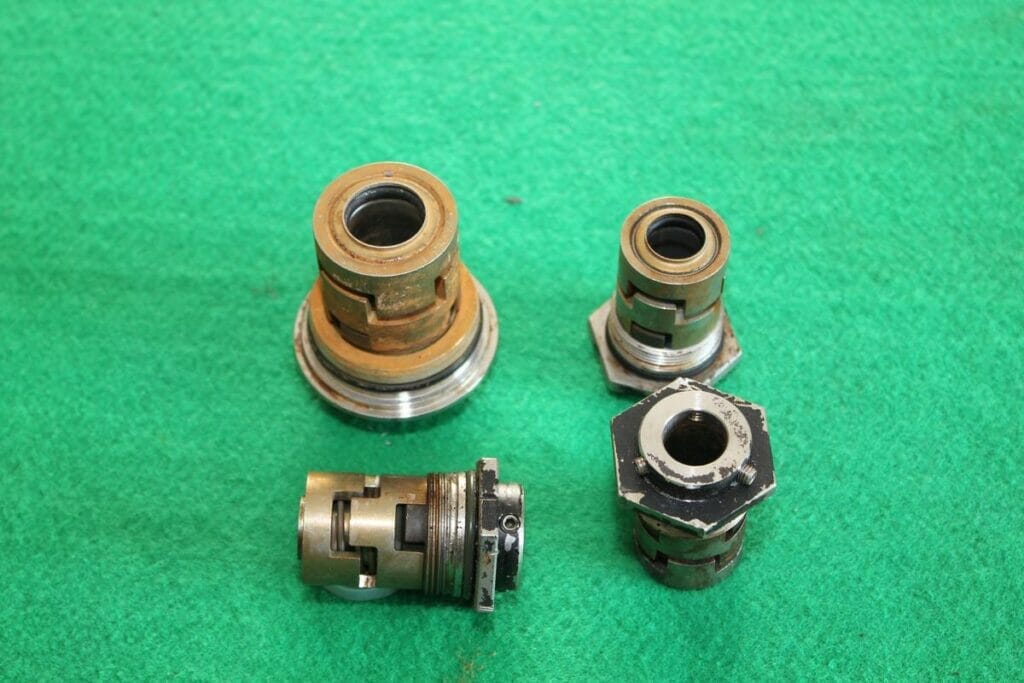
What is a Static Seal
A static seal is a type of seal that prevents leakage between two stationary surfaces. It is designed to maintain a tight seal without any moving parts. Static seals are commonly used in applications where the sealed components remain stationary relative to each other, such as gaskets, O-rings, and sealing washers.
How Static Seals Work
Static seals work by filling the gap between two mating surfaces, preventing any fluid or gas from passing through. The seal is typically made from a soft, pliable material that conforms to the surface irregularities of the mating components. When the seal is compressed between the surfaces, it creates a tight barrier, preventing leakage.
Types of Static Seals
- Gaskets: Flat seals made from materials like rubber, cork, or fibrous composites, used between flanges or mating surfaces.
- O-rings: Round, elastomeric seals that sit in grooves and compress to create a seal between two surfaces.
- Sealing washers: Flat washers with a soft, compressible material on one or both sides, used to seal around bolts or screws.
- Liquid gaskets: Pliable, liquid-applied materials that fill surface irregularities and create a seal upon curing.
What is Dynamic Seal
Dynamic seals are used to prevent leakage between moving parts, such as rotating shafts or reciprocating rods. They are designed to maintain a tight seal while accommodating motion and tolerating a certain degree of misalignment or eccentricity.
How Dynamic Seals Work
Dynamic seals typically consist of a flexible sealing element, such as an O-ring or lip seal, that is held in place by a rigid housing or retainer. The sealing element is in contact with the moving surface, creating a barrier that prevents fluid or gas from escaping. As the moving part rotates or reciprocates, the sealing element maintains contact and adjusts to any changes in the surface, ensuring a consistent seal.
Differences Between Static Seals and Dynamic Seals
Sealing Mechanism
Static seals: Static seals prevent leakage between two stationary surfaces by compression. They rely on compression force to block fluid passage.
Dynamic seals: Dynamic seals prevent leakage between a stationary and moving surface through controlled leakage paths. They utilize a lubricating film to minimize friction and wear.
Motion and Speed
Static seals: Static seals are designed for zero motion between sealing surfaces.
Dynamic seals: Dynamic seals are engineered to accommodate continuous or intermittent motion.
Material
Static seals: Static seals are commonly made from non-metallic materials like elastomers, plastics, and composites that can conform to surface irregularities.
Dynamic seals: Dynamic seals require more durable materials such as PTFE, polyurethane, or specialized elastomers to withstand motion, pressure, and temperature fluctuations.
Maintenance Requirements
Static seals: Static seals generally require less maintenance as they have no moving parts and experience less wear.
Dynamic seals: Dynamic seals demand regular inspection, lubrication, and replacement due to continuous motion and friction, which accelerates deterioration.
Gland Design
Static seals: Gland design for static seals focuses on achieving optimal compression to prevent leakage.
Dynamic seals: Gland design for dynamic seals must account for lubrication, heat dissipation, and allowance for movement. They are more complex and often incorporate multiple components like backup rings and anti-extrusion rings.
Tolerance to Misalignment
Static seals: Static seals can tolerate some degree of misalignment as the compression force can compensate for minor irregularities.
Dynamic seals: Dynamic seals have limited tolerance for misalignment. Excessive runout or shaft deflection can cause rapid wear and leakage.
Heat Generation
Static seals: Static seals generate minimal heat as there is no relative motion between surfaces.
Dynamic seals: Dynamic seals generate significant heat due to friction. This can lead to material degradation, increased wear, and reduced sealing efficiency if not properly managed.
Application
Static seals: Static seals are used in applications with no relative motion between components, such as gaskets, O-rings, and flange seals.
Dynamic seals: Dynamic seals are employed in applications involving linear, rotary, or oscillating motion, including hydraulic and pneumatic cylinders, pumps, and valves.
In summary
Static and dynamic seals each have unique advantages for different applications. Consider factors like pressure, temperature, motion, and cost when selecting the right seal type. To discuss your specific sealing needs, contact our knowledgeable team today for expert guidance and customized solutions.