Have you ever wondered how machines and equipment prevent leaks and maintain optimal performance? The answer lies in mechanical seals.
In this blog post, we’ll explore the various types of mechanical seals and their unique characteristics. By understanding the differences between these seals, you’ll gain valuable insights into selecting the right one for your specific application.
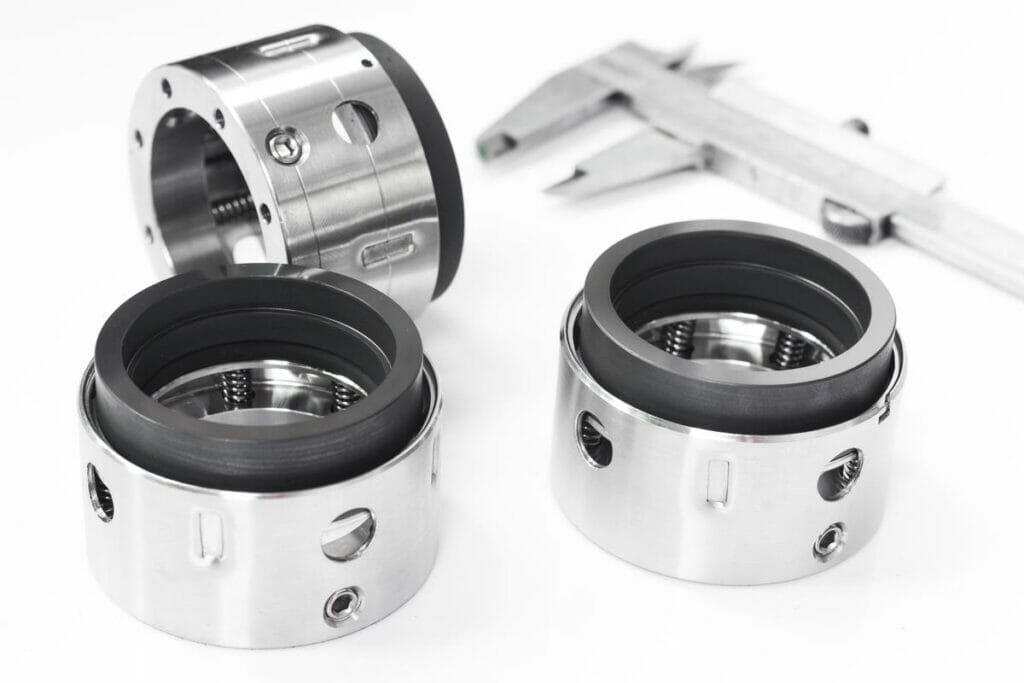
Pusher Seals
Pusher seals are a type of mechanical seal. They are one of the most common types of mechanical seals used in various industries. Pusher seals are designed to handle axial shaft movement and misalignment.
The sealing faces of pusher seals are pushed together by springs. These springs are located behind the stationary face of the seal. The springs provide a constant closing force to keep the sealing faces in contact.
Pusher seals are relatively simple in design compared to other types of mechanical seals. They are often less expensive than more complex seal designs. However, pusher seals may have higher leakage rates than some other seal types.
Non-Pusher Seals
Non-pusher mechanical seals, also known as bellows seals, are a type of mechanical seal that uses a flexible metal bellows to maintain contact between the stationary and rotating seal faces. The bellows eliminates the need for secondary seals and springs, which are used in pusher-type seals.
The metal bellows is welded to the stationary seal face and the gland or housing, creating a leak-tight seal. As the shaft moves axially, the bellows flexes to maintain contact between the seal faces, ensuring a constant sealing pressure.
Non-pusher seals are available in both balanced and unbalanced configurations. Balanced non-pusher seals are designed to minimize the effects of hydraulic pressure on the seal faces, extending seal life and reducing wear.
One of the main advantages of non-pusher seals is their ability to handle higher levels of shaft misalignment and axial movement compared to pusher seals. This makes them suitable for applications with high vibration or where shaft movement is expected.
Balanced Seals
Balanced mechanical seals are designed to equalize the hydraulic forces acting on the seal faces. This is achieved by incorporating a step or groove in the rotating seal face, which balances the hydraulic pressure between the inner and outer diameters of the seal faces.
The balanced design reduces the net closing force on the seal faces, resulting in lower face loads and improved seal performance. This allows balanced seals to operate at higher pressures and speeds compared to unbalanced seals.
Unbalanced Seals
Unbalanced seals are a type of mechanical seal that experiences a higher pressure on the process side compared to the atmospheric side. This pressure imbalance results in a net hydraulic closing force acting on the seal faces. Unbalanced seals are commonly used in applications where the process pressure is relatively low, typically below 100 psi.
In unbalanced seals, the entire process pressure acts on the back of the stationary seal face, creating a higher closing force. This increased closing force helps to prevent leakage and maintain seal integrity. However, it also leads to higher face loads and increased wear on the seal faces, particularly at higher pressures.
Conventional Seals
Conventional mechanical seals are a type of seal that consists of two main components: a stationary seal ring and a rotating seal ring. The stationary seal ring is typically mounted in a gland or housing, while the rotating seal ring is attached to the shaft of the equipment being sealed, such as a pump or compressor.
The two seal rings are held together by a combination of hydraulic pressure and spring force, creating a tight seal that prevents leakage of the process fluid. The seal faces are usually made of hard, wear-resistant materials such as silicon carbide, tungsten carbide, or ceramic.
Conventional mechanical seals are designed to handle a wide range of operating conditions, including high temperatures, high pressures, and aggressive media. They are commonly used in industries such as oil and gas, chemical processing, and power generation.
One of the advantages of conventional mechanical seals is their simplicity and reliability. They have fewer components than other types of mechanical seals, which can make them easier to install and maintain. However, they may require more frequent adjustment and replacement of the seal faces due to wear over time.
Cartridge Seals
Cartridge seals are a type of mechanical seal that comes pre-assembled and ready to install. They are designed to be easily installed and replaced, reducing downtime and maintenance costs.
Cartridge seals consist of a stationary seal face, a rotating seal face, and secondary seals, all contained within a single unit. This unit is mounted on the pump shaft and held in place by a stationary housing.
One of the main advantages of cartridge seals is their ease of installation. Unlike component seals, which require careful alignment and assembly, cartridge seals can be installed quickly and easily without special tools or expertise.
Cartridge seals also offer improved reliability and performance compared to traditional gland packing. They provide a more effective seal, reduce friction and wear, and can accommodate shaft movement and misalignment.
In Conclusion
In conclusion, understanding the various types of mechanical seals is crucial for selecting the most suitable seal for your specific application, ensuring optimal performance, reliability, and longevity.
Consult with a trusted mechanical seal supplier to discuss your requirements and explore the best options for your needs. Don’t hesitate to reach out for expert guidance and support in making an informed decision.