Have you ever wondered what a wear ring is and how it affects your centrifugal pump’s performance? In this blog post, we’ll explore the crucial role of wear rings in centrifugal pumps. By the end, you’ll understand how these small components can make a big difference in the efficiency and longevity of your pumping system.

What is a Wear Ring
A wear ring, also known as a wear plate or wear ring insert, is a critical component in centrifugal pumps. It is a replaceable part typically made from materials such as bronze, cast iron, or stainless steel.
Wear rings are designed to be sacrificial components, protecting the more expensive and difficult-to-replace parts of the pump, such as the impeller and casing, from excessive wear. They are installed in the pump casing, surrounding the impeller eye, and sometimes on the impeller itself.
What is the function of the wear ring
- Minimizing leakage: Helps to minimize fluid leakage between the impeller and the casing, improving pump efficiency.
- Maintaining clearance: Ensures a close clearance between the impeller and the casing, essential for optimal performance.
- Protecting the casing: Acts as a sacrificial component, absorbing wear to extend the life of the casing.
- Improving efficiency: Contributes to improved pump efficiency by minimizing leakage and maintaining proper clearance, leading to lower energy consumption and reduced operating costs.
- Simplifying maintenance: Designed for easy replacement when worn, simplifying maintenance and reducing downtime and costly repairs to the casing.
How Wear Rings Work
Wear rings work by creating a close clearance between the rotating impeller and the stationary pump casing.
As the impeller rotates, the high-pressure fluid on the discharge side of the pump tries to leak back to the low-pressure suction side through the clearance between the impeller and the casing. The wear ring acts as a restriction, limiting the amount of fluid that can leak through this clearance.
The close clearance between the wear ring and the impeller creates a thin film of fluid that acts as a hydrodynamic seal.
Types of Wear Rings
- Straight bore wear rings: Simple cylindrical shape, most basic type. Easy to manufacture and replace, making them cost-effective for many applications.
- Stepped wear rings: Feature a step or shoulder on the inner diameter, reducing axial thrust and improving pump efficiency. More complex to manufacture but offer better performance in certain situations.
- Labyrinth wear rings: Have grooves or teeth on the inner diameter, creating a labyrinth seal that minimizes leakage and improves efficiency. More expensive but ideal for high-pressure applications.
- Floating wear rings: Designed to move slightly within the pump casing, allowing adjustment to changes in operating conditions and reducing wear on the impeller and casing.
Locations of Wear Rings in Centrifugal Pumps
- Impeller wear rings: These are located on the impeller hub, just behind the impeller vanes. They provide a seal between the high-pressure and low-pressure sides of the impeller, reducing leakage and improving efficiency.
- Casing wear rings: These are located in the pump casing, surrounding the impeller. They provide a seal between the impeller and the casing, preventing leakage and maintaining the pressure differential necessary for the pump to operate efficiently.
In some cases, wear rings may also be located on the shaft sleeve or other components, depending on the specific design of the pump.
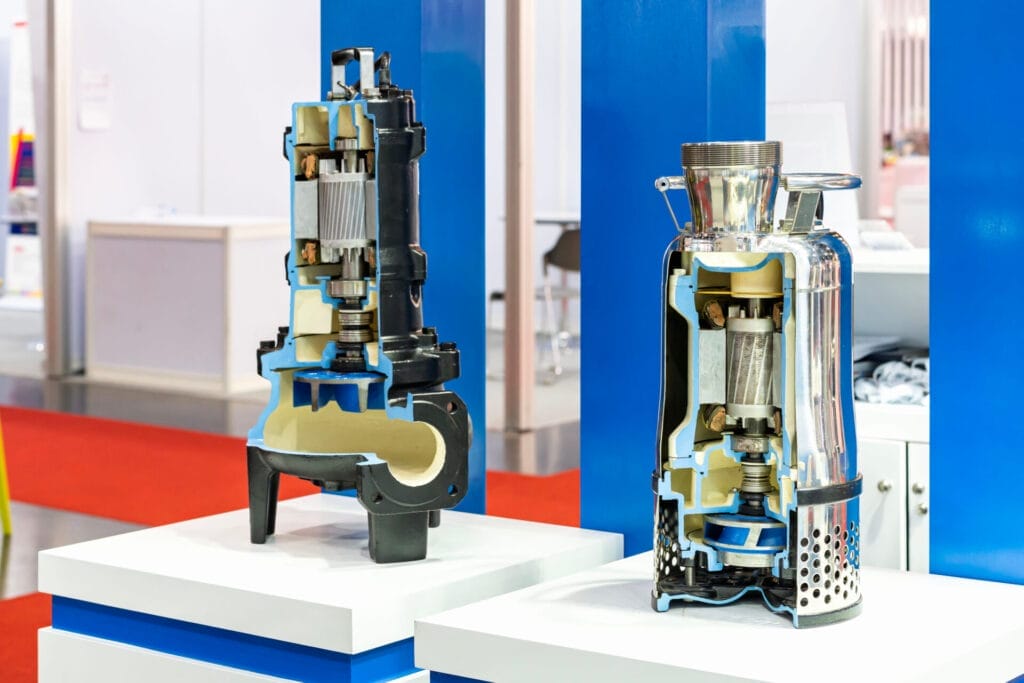
Materials Used for Wear Rings
- Bronze: A popular choice for many applications due to its good wear resistance, corrosion resistance, and relatively low cost.
- Stainless steel: Offers excellent corrosion resistance and is often used in pumps handling corrosive or abrasive fluids.
- Hardened steel: Used in applications where high wear resistance is required, such as in pumps handling slurries or other abrasive fluids.
- Ceramic: Extremely hard and wear-resistant, making it ideal for high-pressure, high-temperature, or highly abrasive applications.
Wear Ring Clearances
Wear ring clearances refer to the gap between the wear ring and the impeller hub or casing in a centrifugal pump.
The primary purpose of wear ring clearances is to minimize the amount of fluid leakage from the high-pressure side to the low-pressure side of the impeller. Excessive clearances can lead to increased fluid recirculation, resulting in reduced pump efficiency and increased wear on pump components.
How to Measure Wear Ring Clearances
First, insert the feeler gauge or position the dial indicator between the wear ring and the impeller hub. Measure the clearance at multiple points around the circumference to account for any variation.
Next, consult the pump manufacturer’s documentation for the recommended wear ring clearance range. Compare the measured values with the specified range to determine if the clearances are within acceptable limits.
How to Change the Wear Ring of a Centrifugal Pump
Step 1. Preparation and Safety Measures
Ensure the pump is isolated from all power sources. Lock out and tag out the electrical supply. Close the suction and discharge valves to isolate the pump, drain the pump casing, and let it cool if recently operated.
Step 2. Disassembly and Wear Ring Removal
Remove the coupling guard and disconnect the coupling between the pump and the motor. Remove bolts securing the bearing housing to the pump casing, then pull out the rotating assembly (impeller, shaft, and bearings). Locate and remove the wear ring, either using a puller/hydraulic press if press-fitted or by removing set screws if present.
Step 3. Installing the New Wear Ring
Clean the impeller hub, repairing or replacing the impeller if needed. If press-fitted, apply oil to the inner surface and press it onto the hub evenly. If held by set screws, position and secure the wear ring, tightening screws in a crisscross pattern.
Step 4. Reassembly and Testing
Reassemble the rotating assembly into the pump casing, ensuring proper alignment and free rotation of the shaft. Reinstall the bearing housing and bolts, reconnect the coupling, and reinstall the guard. Open all valves, prime the pump, and start it. Check for unusual noises, vibrations, or leaks, and adjust as necessary.
FAQs
Can worn-out wear rings cause damage to a centrifugal pump?
Yes, worn-out wear rings can cause increased internal leakage, reduced pump efficiency, and potential damage to other pump components due to increased vibration and bearing loads.
Are wear rings used in all types of centrifugal pumps?
Wear rings are commonly used in many types of centrifugal pumps, particularly in medium to large-sized pumps and those handling abrasive or corrosive fluids.
Can wear rings be adjusted to improve pump performance?
In some cases, the clearance between the wear ring and the impeller can be adjusted to optimize pump performance. However, this should only be done by experienced professionals.
How do I know if my centrifugal pump’s wear rings need replacement?
Signs that wear rings may need replacement include increased vibration, reduced pump performance, and visible wear or damage to the rings during inspection.
In conclusion
Understanding wear rings in centrifugal pumps is crucial for maintaining pump efficiency and preventing costly failures. Regularly inspecting and replacing wear rings when necessary can significantly extend the pump’s lifespan. For expert guidance on wear ring maintenance, consult a professional pump service provider today.