What happens when a mechanical seal runs dry? This dangerous situation can lead to costly damage and downtime.
In this blog post, we’ll explore the consequences of a dry-running mechanical seal and provide practical tips to prevent this issue. By understanding the risks and implementing proper maintenance, you can ensure the longevity and reliability of your sealing system.
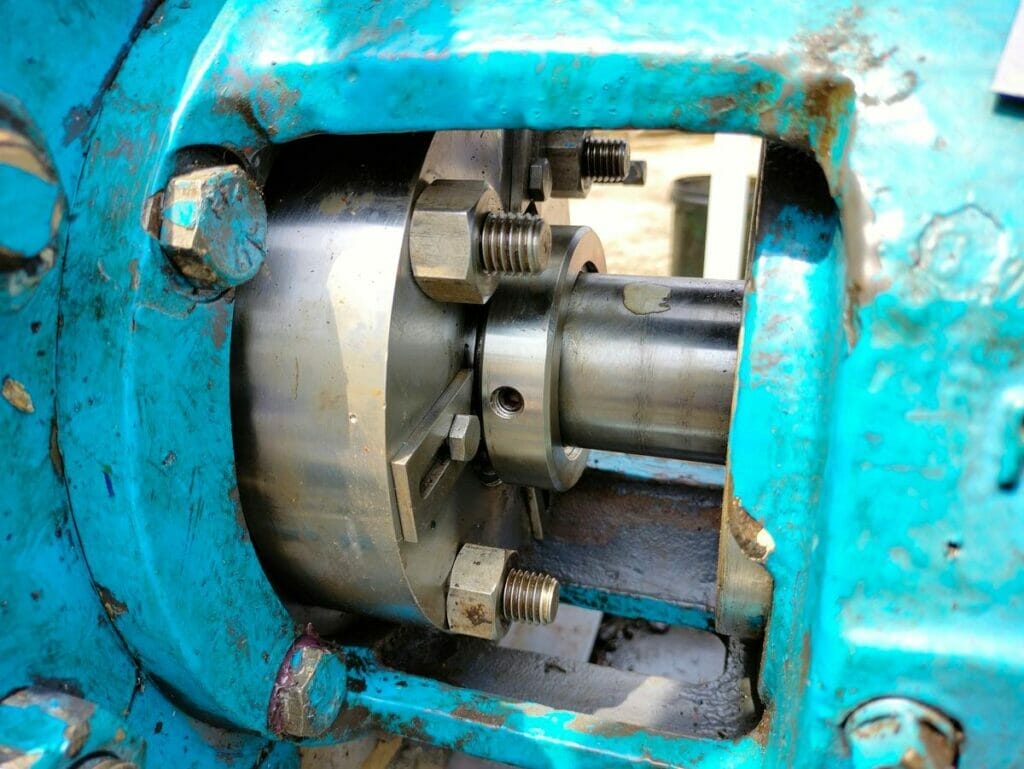
Symptoms of Dry Running Mechanical Seals
Noise
The lack of lubrication causes the seal faces to grind against each other, resulting in a loud, screeching, or grinding sound. This noise is a clear indication that the seal is not functioning correctly and requires immediate attention.
Leakage
Dry running can cause the seal faces to wear out rapidly, leading to increased leakage. As the faces deteriorate, the seal loses its ability to contain the process fluid effectively.
Vibration
The increased friction between the seal faces during dry running can cause vibrations within the sealing system. These vibrations can be felt throughout the pump or equipment, indicating that the mechanical seal is not operating smoothly. Vibrations can also lead to secondary damage to other components, such as bearings and shafts, if left unchecked.
Increased Power Consumption
As the mechanical seal faces experience higher friction due to dry running, the equipment requires more power to maintain its operation. This increased power consumption can be observed through higher energy bills or increased load on the motor. Monitoring power consumption can help identify potential issues with the mechanical seal.
Visible Damage
Upon inspection, a dry running mechanical seal may exhibit visible signs of damage. The seal faces might show scoring, pitting, or cracks due to the lack of lubrication and excessive heat generation. The seal components, such as the elastomers and springs, may also show signs of degradation or deformation.
Smoke or Burning Odor
In severe cases of dry running, the excessive heat generated at the seal faces can cause the sealing materials to burn or melt. This can result in visible smoke or a burning odor emanating from the seal area.
Increased Temperature
Dry running mechanical seals experience a rapid increase in temperature due to the lack of lubrication and cooling. The seal faces generate excessive heat, which can be detected through temperature monitoring devices or by touching the seal housing (with proper safety precautions).

Causes of Dry Running
Insufficient Prime
If the pump is not properly primed before starting, it may run dry until the fluid reaches the impeller.
Low Suction Head
When the liquid level in the suction source is too low, the pump may draw in air instead of fluid, causing dry running.
Cavitation
When the fluid’s vapor pressure is higher than the local pressure in the pump, cavitation occurs, leading to the formation of vapor bubbles. These bubbles can cause dry running when they collapse.
Closed Suction Valve
If the suction valve is closed or not fully open, the pump may not receive an adequate supply of fluid, resulting in dry running.
Air Leaks
Leaks in the suction line or seal can allow air to enter the system, displacing the fluid and causing dry running.
Blocked Suction
If the suction strainer or inlet is blocked by debris, the pump may not receive enough fluid, leading to dry running.
Incorrect System Design
An improperly designed system, such as one with undersized piping or an incorrectly sized pump, can cause dry running.
Operator Error
Human error, such as forgetting to open the suction valve or failing to prime the pump correctly, can lead to dry running.

How to Prevent Mechanical Seal Damage from Dry Running
Proper Installation and Alignment
Ensure that the seal is installed according to the manufacturer’s specifications and that the shaft and seal are properly aligned.
Adequate Lubrication
Ensure that the seal is always supplied with a sufficient amount of clean, compatible fluid. This can be achieved through proper system design, including adequate fluid reservoirs, piping, and pumping systems.
Monitoring and Control Systems
Implementing monitoring and control systems can help detect and prevent dry running conditions. These systems can monitor various parameters such as fluid levels, temperatures, and pressures, and alert operators when conditions are approaching critical levels. In some cases, these systems can automatically shut down the equipment to prevent further damage.
Proper Material Selection
The materials must be compatible with the fluid being sealed and able to withstand the operating conditions of the system. For example, in high-temperature applications, materials with higher heat resistance, such as silicon carbide or tungsten carbide, may be required.
Regular Maintenance and Inspections
Checking for signs of wear, leakage, or damage to the seal faces, as well as ensuring that the seal is properly lubricated and aligned. Establishing a preventive maintenance schedule based on the manufacturer’s recommendations.
FAQs
How long can a mechanical seal run dry before failing?
The time before failure depends on factors like seal material and speed, but dry running can cause seal failure within seconds to minutes.
Can a mechanical seal recover from running dry?
In most cases, dry running causes permanent damage to the seal faces, requiring seal replacement to restore proper function.
What should you do if you suspect a mechanical seal has run dry?
Shut down the equipment immediately, assess the damage, and replace the seal if necessary before resuming operation.
Can certain types of mechanical seals withstand dry running?
Some specialized seals, like those with self-lubricating materials or dry-running capabilities, may tolerate brief periods of dry running, but prolonged exposure can still cause damage.
In conclusion
Mechanical seal running dry can lead to severe damage and failure. To prevent this, ensure proper installation, maintain adequate lubrication, and monitor the seal regularly. By taking these precautions, you can extend the life of your mechanical seal and avoid costly downtime. Contact our experts for personalized solutions.