Are you curious about gland packing seals and how they work? In this comprehensive guide, we’ll dive deep into the world of gland packing seals, exploring their types, applications, and maintenance.
By the end of this blog post, you’ll have a solid understanding of these essential components and how they contribute to the smooth operation of various industrial processes.

What is Gland Packing
Gland packing is a type of seal that provides a flexible and adaptable sealing solution for rotating shafts, such as those found in centrifugal pumps, agitators, and other dynamic sealing applications. It is a cost-effective alternative to mechanical seals, offering reliable performance in a wide range of operating conditions.
Gland packing consists of a set of pliable rings or a braided rope made from various materials, such as graphite, PTFE, aramid fibers, or carbon fibers. These materials are selected based on their chemical resistance, thermal conductivity, and mechanical properties to suit specific application requirements.
How Gland Packing Works
The packing material is compressed inside a stuffing box or gland, which surrounds the rotating shaft. As the gland is tightened, the packing expands radially, creating a tight seal against the shaft and the stuffing box walls. This compression allows the packing to conform to the shape of the shaft, accommodating any irregularities or misalignments.
During operation, the packing material is subjected to friction and heat generated by the rotating shaft. To prevent excessive wear and damage to the packing and shaft, a small amount of leakage is allowed to lubricate and cool the sealing interface. This leakage is controlled by adjusting the gland follower, which applies pressure to the packing rings.
Components of Gland Packing
Gland packing consists of several key components that work together to create an effective sealing solution. The primary components include the packing material, gland follower, gland bolts, and stuffing box.
- Packing Material: The main seal, made from materials like graphite, PTFE, aramid, or carbon fibers, braided for even compression.
- Gland Follower: A metal piece, often stainless or carbon steel, compressing the packing material against the shaft.
- Gland Bolts: Apply pressure to the gland follower for proper sealing and avoiding over-compression.
- Stuffing Box: The cavity in the equipment housing where the packing material is installed.
In addition to these primary components, gland packing seals may also incorporate lantern rings, which are metal spacers placed between packing rings to facilitate lubrication and cooling. Some designs may also include a gland leakage port, which allows for the controlled release of small amounts of process fluid to lubricate the packing and prevent heat buildup.
Types of Gland Packing
There are several types of gland packing materials available, each with its own unique properties and advantages. The selection of the appropriate type depends on factors such as the application, operating conditions, and the specific requirements of the system.
Some common types of gland packing include:
- Graphite packing: Made from flexible graphite or graphite-impregnated fibers, it offers excellent thermal and chemical resistance. Suitable for high-temperature applications and used in pumps, valves, and other rotating equipment.
- PTFE packing: Known for its low friction coefficient and excellent chemical resistance. Ideal for aggressive media and wide temperature range applications. Common in chemical, pharmaceutical, and food industries.
- Aramid fiber packing: Made from synthetic aramid fibers, providing high strength and excellent thermal stability. Resistant to abrasion and high temperatures. Used in demanding applications in pumps, valves, and other rotary equipment.
- Carbon fiber packing: Made from high-quality carbon fibers, offering excellent thermal conductivity and chemical resistance. Suitable for high-temperature applications in pumps, valves, and rotating equipment in oil and gas, chemical processing, and power generation industries.
- Graphite-PTFE packing: Combines advantages of both graphite and PTFE materials. Offers excellent chemical resistance, low friction, and good thermal conductivity. Suitable for a wide range of applications, including pumps and valves in various industries.
- Rope packing: Made from braided or twisted fibers like cotton, hemp, or synthetic materials. A cost-effective option for low-pressure and low-temperature applications, often used in pumps.
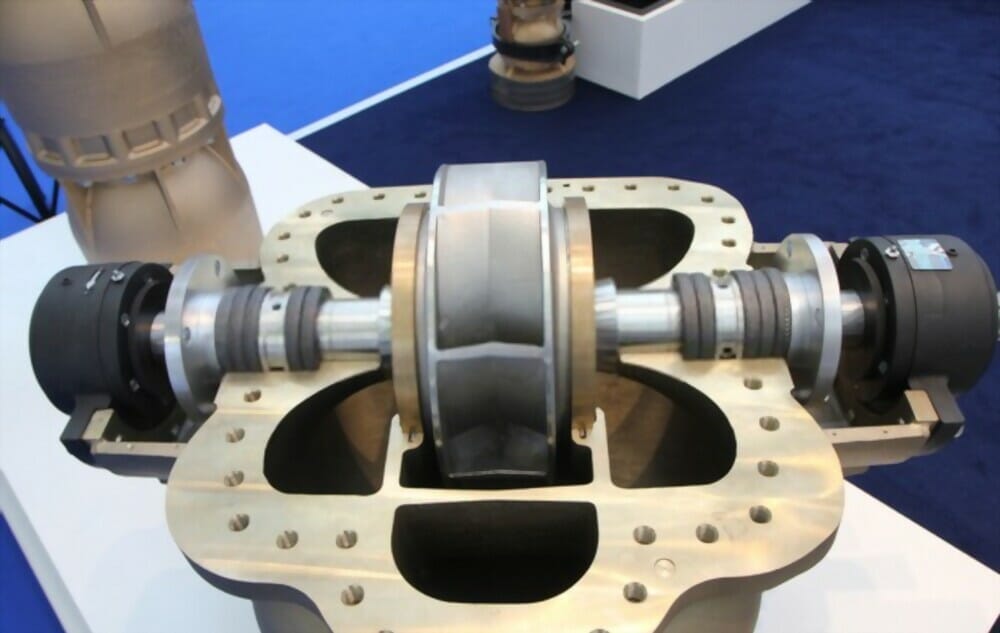
Advantages of Gland Packing
- Low cost: Gland packing is relatively inexpensive compared to other sealing methods. It is a cost-effective solution for many applications.
- Easy to install and maintain: Gland packing is simple to install, does not require special tools or extensive training, and maintenance is straightforward. It can be easily adjusted or replaced as needed.
- Versatile: Gland packing can be used on a wide variety of equipment, including pumps, valves, and other rotating equipment. It can handle a range of temperatures, pressures, and media.
- Reliable sealing: When properly installed and maintained, gland packing provides reliable sealing. It conforms to the shape of the shaft or stem to create a tight seal, preventing leaks and containing process fluids.
- Meets emissions standards: Gland packing can help meet fugitive emissions standards. Low-emission packing materials are available for environmental compliance.
- Long service life: High-quality gland packing can have a long service life, operating for extended periods without needing replacement. Proper installation and maintenance practices help extend packing life.
Disadvantages of Gland Packing
- Constant Adjustment and Maintenance: Gland packing seals need frequent adjustments and maintenance to ensure proper sealing.
- Wear and Tear: The packing material wears down over time, leading to increased leakage and higher maintenance costs.
- Higher Friction and Heat Generation: The friction between the packing material and the rotating shaft generates heat, causing thermal expansion and potential damage.
- Limited Operating Conditions: Not suitable for high-speed, abrasive, or corrosive applications due to excessive wear and potential premature failure.
- Leakage in Sensitive Environments: Inadequate for applications requiring strict leakage control, such as the food industry or hygienic processes.
- Long-term Costs: Frequent maintenance, replacements, and potential downtime make them less economically viable despite a lower initial cost.
- Temperature Limitations: Limited effective temperature range; high temperatures can degrade or burn out the packing material, compromising sealing ability.
Factors Affecting Gland Packing Performance
- Type of Packing Material: The packing material determines the seal’s chemical resistance, thermal conductivity, and mechanical properties.
- Operating Conditions: Temperature, pressure, speed, and the type of fluid being sealed impact seal life and efficiency.
- Design and Installation: Proper installation ensures even compression and effective sealing.
- Compatibility with Equipment: The packing material should be compatible with the shaft or stem material to prevent corrosion.
- Cost Considerations: Initial costs may be lower, but maintenance costs can be higher due to regular adjustments and replacements.
Applications and Industries Using Gland Packing
- Valves: Commonly use gland packing around the valve stem to prevent leaks.
- Pumps: Frequently use gland packing around the pump shaft to create a seal and prevent fluid leakage.
- Mixers and Agitators: Use gland packing around their shafts to seal the equipment and contain the materials being mixed.
- Compressors: Utilize gland packing to seal around the compressor shaft and prevent compressed gas or air from escaping.
- Turbines: Employ gland packing around the turbine shaft to maintain proper sealing and prevent steam or gas leaks.
- Heat Exchangers: With rotating shafts, such as those found in some designs, use gland packing to seal the shaft and prevent fluid leakage between the shell and tube sides.
- Rotating Equipment: Other types, such as blowers, generators, and gear boxes, use gland packing to seal between a stationary housing and a moving shaft.
FAQs
How often should gland packing be replaced?
The replacement frequency of gland packing depends on factors such as operating conditions, fluid type, and packing material. Generally, packing should be replaced when leakage becomes excessive or uncontrollable.
Can gland packing be reused?
In most cases, gland packing should not be reused once removed, as it may have lost its sealing properties and could cause leaks if reinstalled.
Which is Better: Mechanical Seal or Gland Seal?
In general, mechanical seals are preferred for applications that require minimal leakage and can justify the higher initial cost. Gland packing is often used in smaller, lower-speed equipment and in situations where some leakage is acceptable.
In Conclusion
In conclusion, gland packing seals are essential components in various industrial applications, offering reliable sealing solutions and preventing leakage.
Investing in high-quality gland packing seals ensures optimal performance and longevity for your equipment. Contact our expert team today to discuss your specific sealing requirements and discover how we can help you select the perfect gland packing seals for your needs.